wyn
Member
- Messages
- 3,659
- Location
- Cardiff
Now and again i need to notch some tubing at one or two angles and lengths.
I have a standard type notcher but it takes a while to set the tube up to notch it....this job usually needs around 100-150 notches at a time.
This is my attempt to make something to speed it all up.
Machining the bearing block in a small clarke lathe...there are two as i had ideas of notching the two ends of the tube at the same time..gave up on that though.
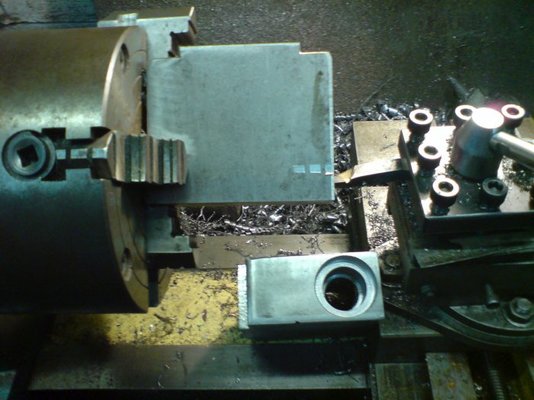
Turning the 20mm silver steel shaft and thread for holesaw
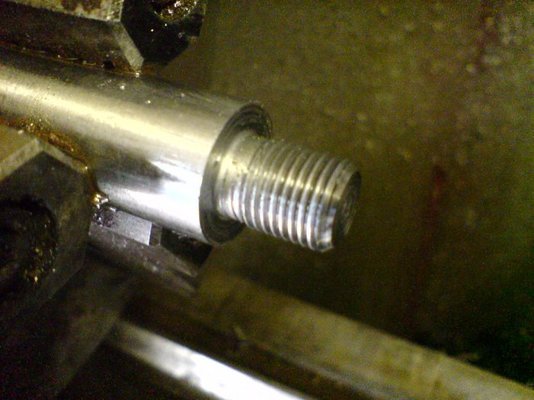
The bearing block with 20mm ID needle rollers. The recess in the end was originaly for a thrust bearing for the double notcher thing, where i was going to have the tube moving instead of the holesaw. It is the right size for an oil seal though so i'll put one in top and bottom.
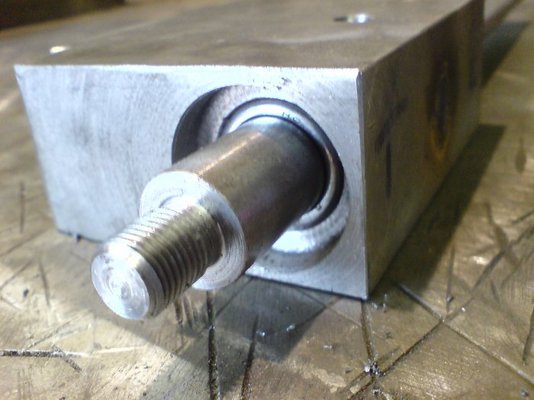
The base of the tube clamp...the middle grooves in the back plate were going to be for a top sliding clamp similar to the bottom.
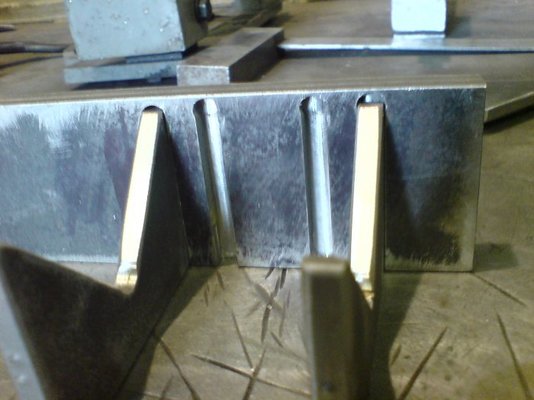
A bit of tig to stick them on. It's a bit undercut as my finger was touching the amp switch on the torch...when i finished i realised it was around 200 amps
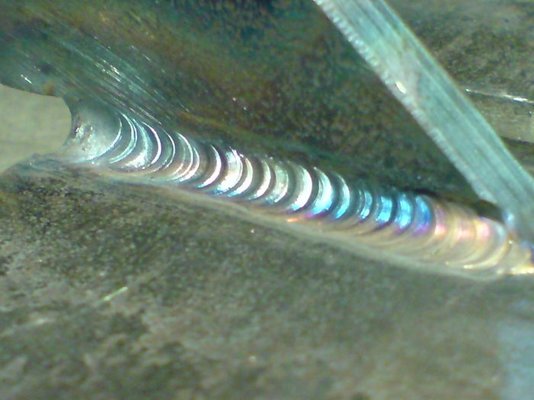
Toggle clamp to hold tube.
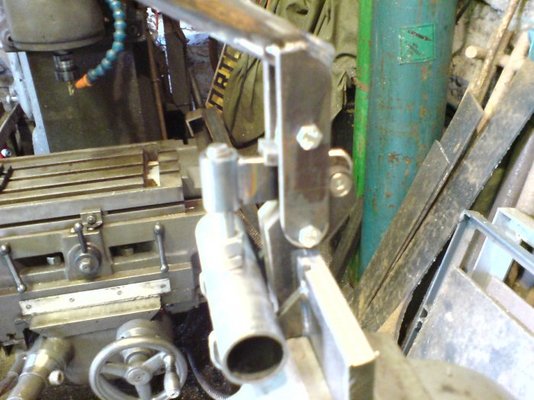
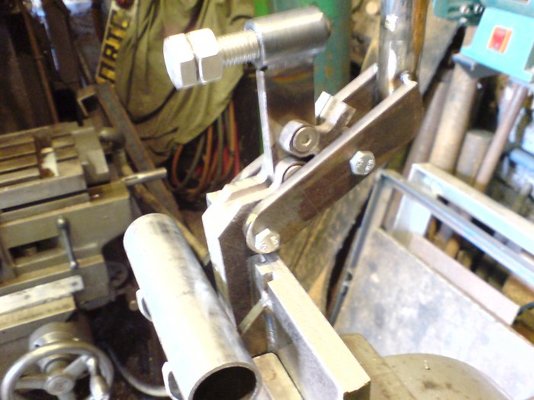
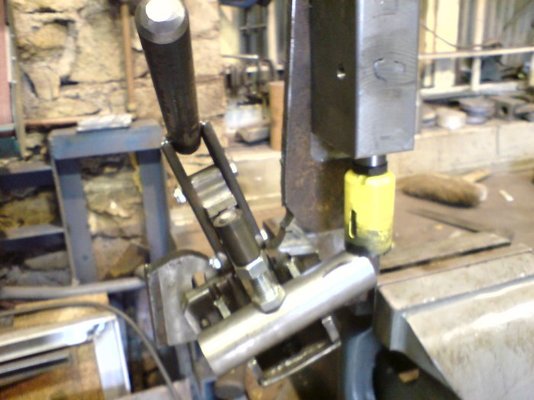
Got it all fixed up to a back plate
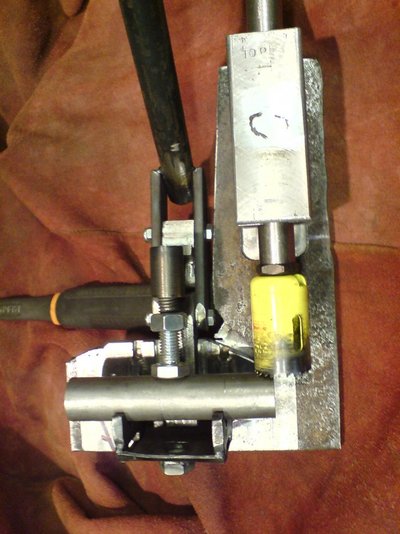
The clamp bolt is a bit wonky
...i think it is down to all the pivot bolts being a bit sloppy as they are pivoting on the threaded bits. I will have to sort some tidier pivots.
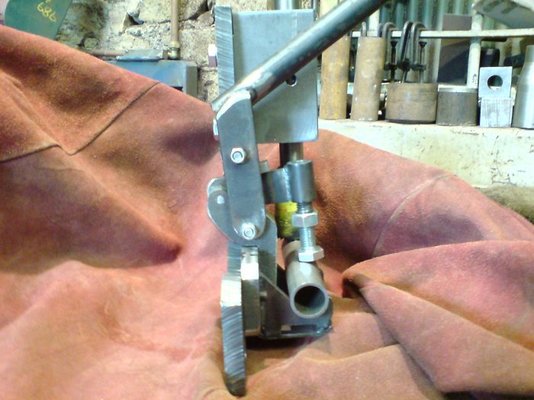
The slot underneath the tube in the "V" bit is for some flat bar that will have some tube welded on to set the distance between the notches.
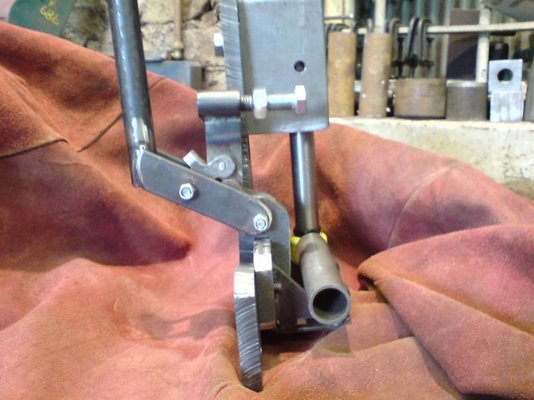
I still need to sort out the bar to get the distance between notches and also make a plate to mount it to a bench drill.
I have a standard type notcher but it takes a while to set the tube up to notch it....this job usually needs around 100-150 notches at a time.
This is my attempt to make something to speed it all up.
Machining the bearing block in a small clarke lathe...there are two as i had ideas of notching the two ends of the tube at the same time..gave up on that though.
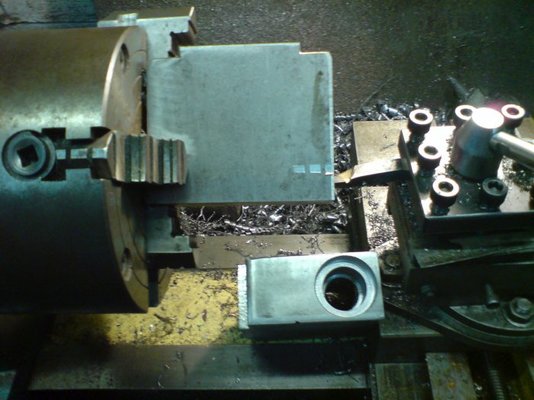
Turning the 20mm silver steel shaft and thread for holesaw
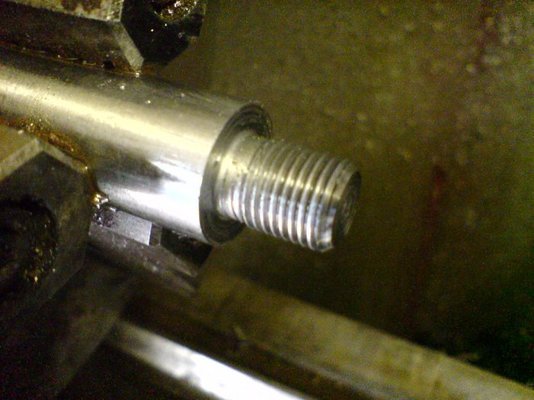
The bearing block with 20mm ID needle rollers. The recess in the end was originaly for a thrust bearing for the double notcher thing, where i was going to have the tube moving instead of the holesaw. It is the right size for an oil seal though so i'll put one in top and bottom.
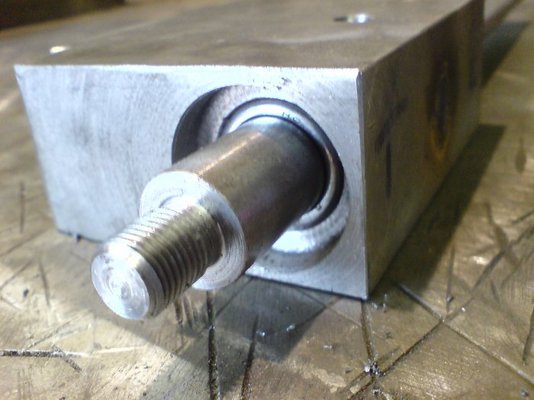
The base of the tube clamp...the middle grooves in the back plate were going to be for a top sliding clamp similar to the bottom.
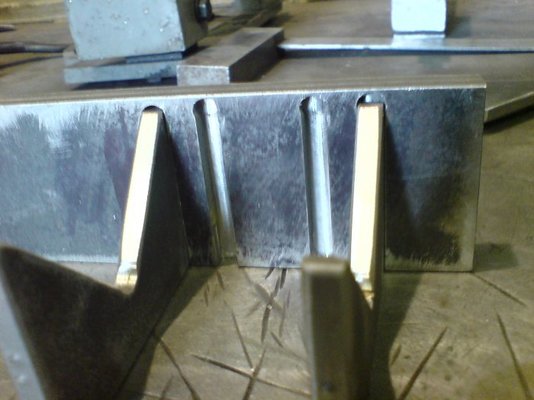
A bit of tig to stick them on. It's a bit undercut as my finger was touching the amp switch on the torch...when i finished i realised it was around 200 amps

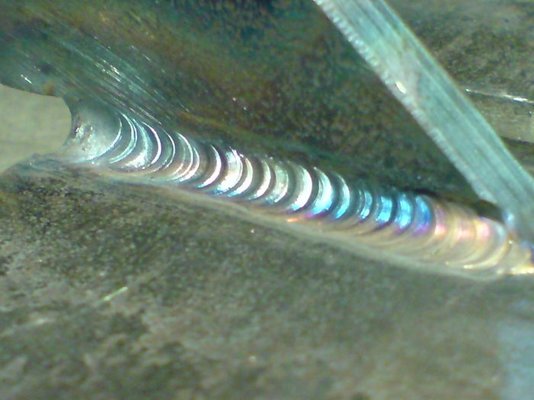
Toggle clamp to hold tube.
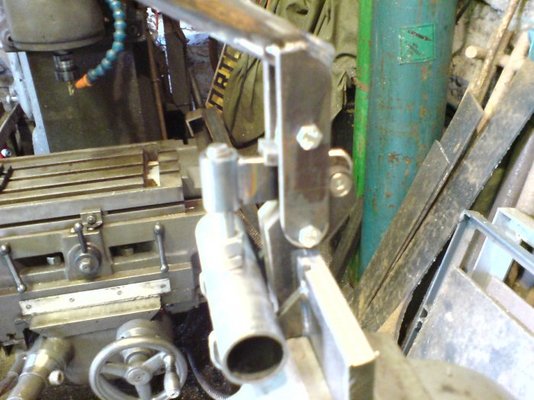
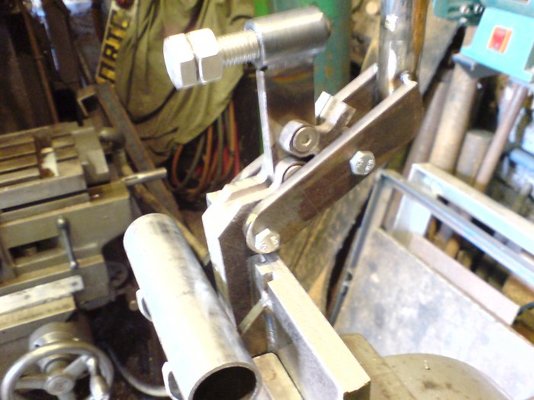
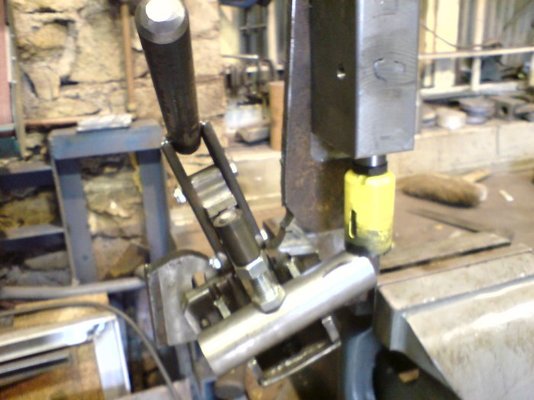
Got it all fixed up to a back plate
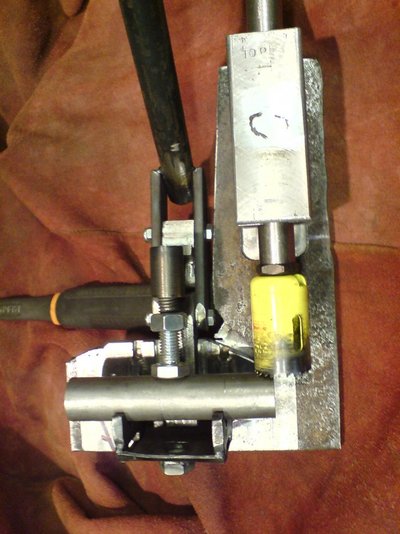
The clamp bolt is a bit wonky

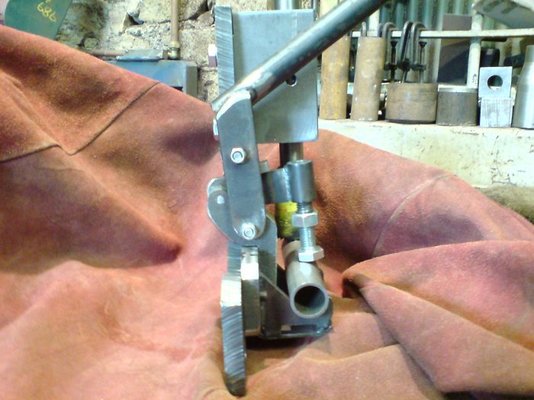
The slot underneath the tube in the "V" bit is for some flat bar that will have some tube welded on to set the distance between the notches.
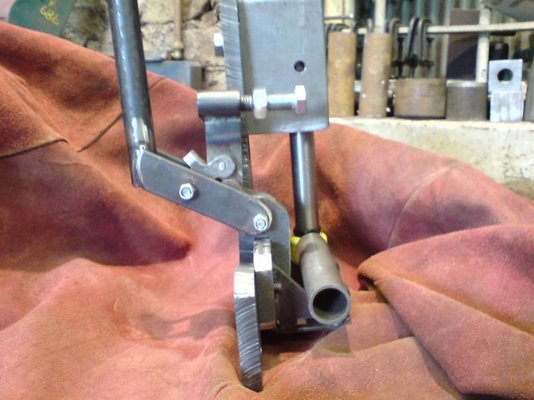
I still need to sort out the bar to get the distance between notches and also make a plate to mount it to a bench drill.