malcolm
& Clementine the Cat
- Messages
- 9,727
- Location
- Bedford UK
The test
Which arc welders are usable and which are horrible? I met up yesterday with aero, snowcat, and GeorgeB to find out. Together we put a varied selection of welders to the test.
This is very much a DIY test - My objective was to find out which machines would be easy to learn with and which might be difficult. Welds in the photos were not done by professionals, and we didn't try anything overhead up a ladder that might really have put the welders to the test.
I've marked the photos with weld position:
1G is horizontal
2F is a fillet welded horizontally
3F is a fillet welded vertically upwards.
The welders
Lorch 220T inverter (run on DC)
Lorch H 150 inverter (DC only)
Sealey inverter (ran out of rime - didn't try this)
W0lf 75 Inverter (DC only)
Oxford oil cooled (AC only)
Cosmo 150 (AC only buzzbox).
Oxford oil cooled vs Lorch 220T (AC vs DC)
One difference between AC and DC became immediately clear before we started running beads (on 6mm plate with 3.2mm rods). It was much more tricky to start the arc on the AC Oxford which needed an accurate wiping motion where the Lorch could be started with a little tap. This is largely a difference between AC and DC. Once we were going the AC was noisier, but was smooth and controllable.
The other advantages of the Lorch were the hot start function that gets rid of the cold bit of weld as you get going, and the crater fill function that gets rid of the depression in the end when you stop. So a lovely weld all the way along without worrying about starts and stops. You can see the difference in starts and stops in the photos below.
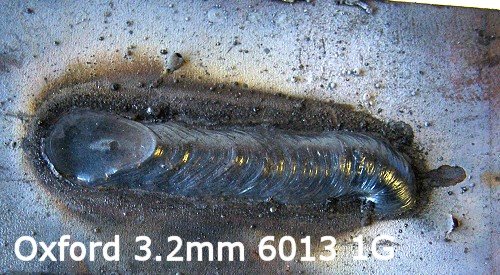
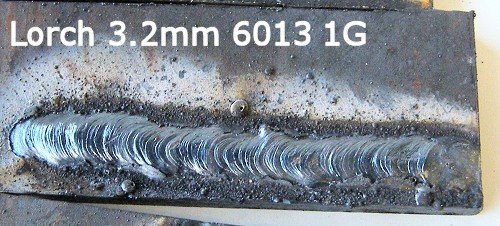
Forgive the weld quality - that was one of mine. I'm very much at the beginner end of beginning, but look at the starts and stops for a beginner.
Oxford
There was some question about whether vertical up would be quite so easy with the Oxford on AC. And I notice some shenanigans went on with the rods being switched from 3.2mm to 2.5mm and from 6013 to 7016. It seemed to manage vertical up quite well.
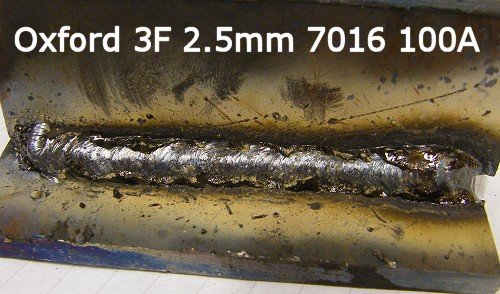
Lorch 220T (Inverter run on DC)
It was lovely to try out an all singing all dancing inverter. The Lorch was the welder I'd have gone home with if only snowcat hadn't been looking. Really this is a TIG machine, but couldn't be faulted on arc. Though we didn't do a lot of arc welding with it.
Lorch H 150 (DC Inverter)
I believe this one had other toys as well such as anti stick, anti-stall. Maybe snowcat can go through those. I managed a vertical up with it! Not a very good vertical up but one with good potential for improvement.
I understand it is quite robust, and that Matt1978's party trick is dropping it off a ladder and then proving it still works. We weren't allowed to try that with snowcat's one.
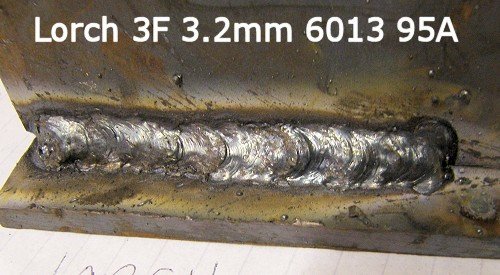
W0lf 75 (DC Inverters)
The surprise of the test was the W0lf inverter actually worked well. This one was only a little one so we were restricted to 2.4mm rods, but it laid beads perfectly well and managed a perfectly respectable vertical up. It's easier to be neat with 2.4mm rods, but they weren't really up to the thickness we were welding.
The W0lf even appeared to have some crater fill at the end of the welds. The main downside of this one was it's lack of output, a bigger one would probably be quite usable.
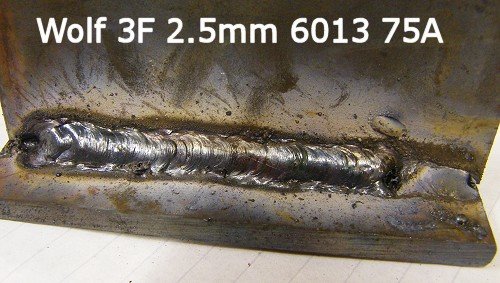
Reliability was something we couldn't test in an afternoon, and again we weren't allowed to drop it, but there's plenty of feedback about reliability of cheap Chinese Inverters elsewhere on the forum. (I've still not forgiven W0lf for repeated attempts at spamming the forum).
Cosmo 150 (AC Buzzbox)
We didn't have much of a chance to try the Cosmo. It didn't have a cooling fan, and it turned out the thermal cutout was set to cut only after the garage filled with acrid smoke. That took aero less than 2 3.2mm rods at 90 amps.
aero reported the arc seemed more harsh than the Oxford welder. Also the welds did seem low on amps, possibly due to the machine losing power with heat, or possibly an inaccurate amp reading. We weren't able to try a vertical up as we broke it too quickly. aero's fillet looked a bit messy (I don't know if you want to put that down to the machine aero?
).
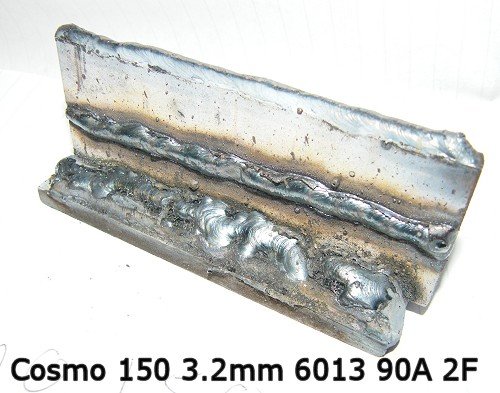
George reports it worked again after it had cooled down which is a relief.
Sections and die pen tests
Snowcat has sectioned a few of the fillet welds. Scroll down to post 8 to see them.
Technique
Snowcat is an excellent teacher. A common fault for the rest of us were holding the rod too far from the work (too much arc length), and running too hot.
Fillets seem much better for practising than flat sheets and joins as there's more scope for things to go wrong. I'd start off pulling the rod, then it would get ahead of me and slag would run ahead and stall the arc. On a butt weld I'd just end up with slag inclusions.
Fillets seem easier for vertical up too. Watching snowcat weld I was surprised to see the slag drip down the weld. That dripping had been putting me off when I tried it, but sure enough once the slag had been chipped off the weld underneath was good.
Which arc welders are usable and which are horrible? I met up yesterday with aero, snowcat, and GeorgeB to find out. Together we put a varied selection of welders to the test.
This is very much a DIY test - My objective was to find out which machines would be easy to learn with and which might be difficult. Welds in the photos were not done by professionals, and we didn't try anything overhead up a ladder that might really have put the welders to the test.
I've marked the photos with weld position:
1G is horizontal
2F is a fillet welded horizontally
3F is a fillet welded vertically upwards.
The welders
Lorch 220T inverter (run on DC)
Lorch H 150 inverter (DC only)
Sealey inverter (ran out of rime - didn't try this)
W0lf 75 Inverter (DC only)
Oxford oil cooled (AC only)
Cosmo 150 (AC only buzzbox).
Oxford oil cooled vs Lorch 220T (AC vs DC)
One difference between AC and DC became immediately clear before we started running beads (on 6mm plate with 3.2mm rods). It was much more tricky to start the arc on the AC Oxford which needed an accurate wiping motion where the Lorch could be started with a little tap. This is largely a difference between AC and DC. Once we were going the AC was noisier, but was smooth and controllable.
The other advantages of the Lorch were the hot start function that gets rid of the cold bit of weld as you get going, and the crater fill function that gets rid of the depression in the end when you stop. So a lovely weld all the way along without worrying about starts and stops. You can see the difference in starts and stops in the photos below.
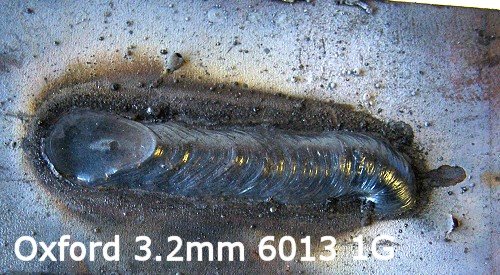
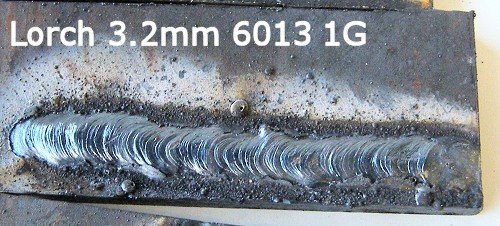
Forgive the weld quality - that was one of mine. I'm very much at the beginner end of beginning, but look at the starts and stops for a beginner.

Oxford
There was some question about whether vertical up would be quite so easy with the Oxford on AC. And I notice some shenanigans went on with the rods being switched from 3.2mm to 2.5mm and from 6013 to 7016. It seemed to manage vertical up quite well.
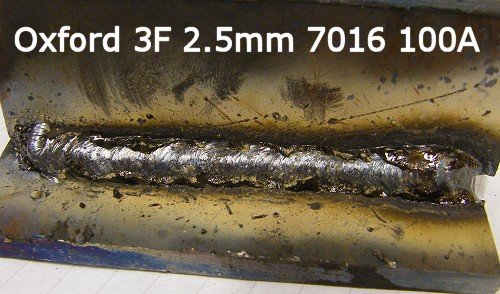
Lorch 220T (Inverter run on DC)
It was lovely to try out an all singing all dancing inverter. The Lorch was the welder I'd have gone home with if only snowcat hadn't been looking. Really this is a TIG machine, but couldn't be faulted on arc. Though we didn't do a lot of arc welding with it.
Lorch H 150 (DC Inverter)
I believe this one had other toys as well such as anti stick, anti-stall. Maybe snowcat can go through those. I managed a vertical up with it! Not a very good vertical up but one with good potential for improvement.
I understand it is quite robust, and that Matt1978's party trick is dropping it off a ladder and then proving it still works. We weren't allowed to try that with snowcat's one.
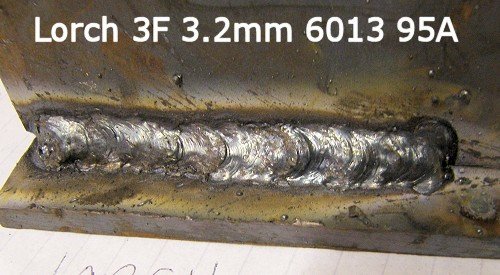
W0lf 75 (DC Inverters)
The surprise of the test was the W0lf inverter actually worked well. This one was only a little one so we were restricted to 2.4mm rods, but it laid beads perfectly well and managed a perfectly respectable vertical up. It's easier to be neat with 2.4mm rods, but they weren't really up to the thickness we were welding.
The W0lf even appeared to have some crater fill at the end of the welds. The main downside of this one was it's lack of output, a bigger one would probably be quite usable.
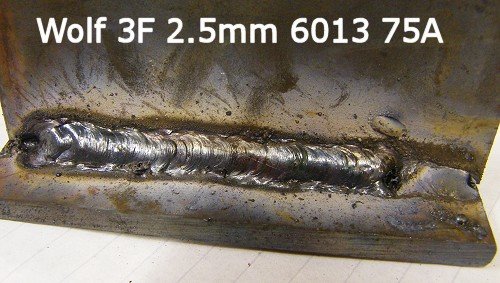
Reliability was something we couldn't test in an afternoon, and again we weren't allowed to drop it, but there's plenty of feedback about reliability of cheap Chinese Inverters elsewhere on the forum. (I've still not forgiven W0lf for repeated attempts at spamming the forum).
Cosmo 150 (AC Buzzbox)
We didn't have much of a chance to try the Cosmo. It didn't have a cooling fan, and it turned out the thermal cutout was set to cut only after the garage filled with acrid smoke. That took aero less than 2 3.2mm rods at 90 amps.
aero reported the arc seemed more harsh than the Oxford welder. Also the welds did seem low on amps, possibly due to the machine losing power with heat, or possibly an inaccurate amp reading. We weren't able to try a vertical up as we broke it too quickly. aero's fillet looked a bit messy (I don't know if you want to put that down to the machine aero?

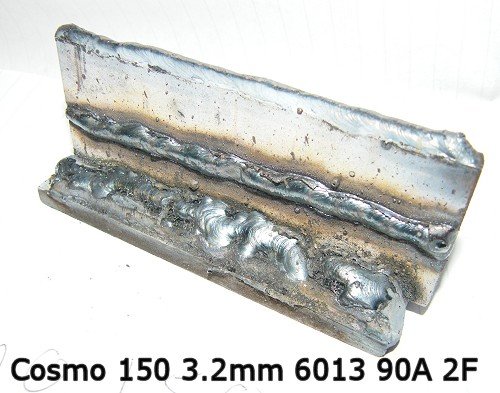
George reports it worked again after it had cooled down which is a relief.
Sections and die pen tests
Snowcat has sectioned a few of the fillet welds. Scroll down to post 8 to see them.
Technique
Snowcat is an excellent teacher. A common fault for the rest of us were holding the rod too far from the work (too much arc length), and running too hot.
Fillets seem much better for practising than flat sheets and joins as there's more scope for things to go wrong. I'd start off pulling the rod, then it would get ahead of me and slag would run ahead and stall the arc. On a butt weld I'd just end up with slag inclusions.
Fillets seem easier for vertical up too. Watching snowcat weld I was surprised to see the slag drip down the weld. That dripping had been putting me off when I tried it, but sure enough once the slag had been chipped off the weld underneath was good.
Last edited: