- Messages
- 22,241
- Location
- Birmingham
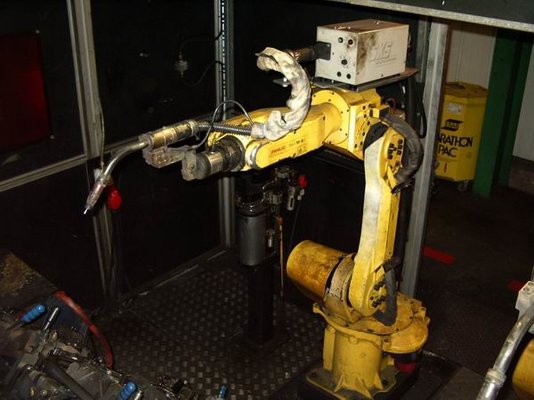
A welding robot, most robot manufacturers produce something similar. 6 axis powered by 6 servo controlled electric motors capable of carrying 5-10 Kg at about 2500mm per second with an accuracy of 0.1mm.
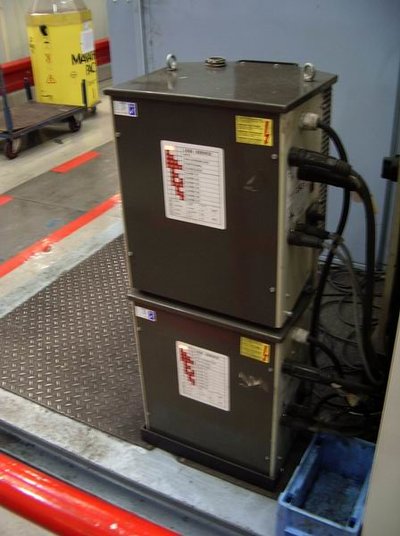
Welding power source can deliver 5 - 480 amps.
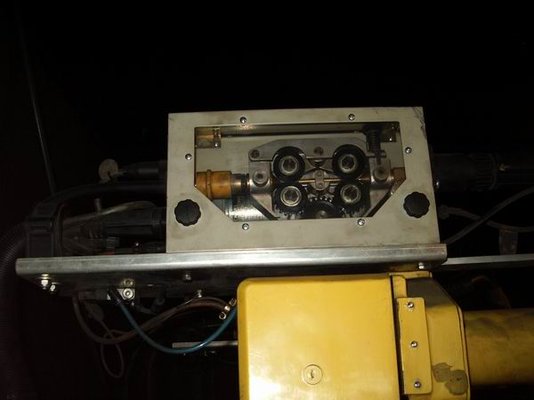
Wire feed unit mounted on top of robot supplied with wire from a 475Kg bulk pack and plumbed in gas.
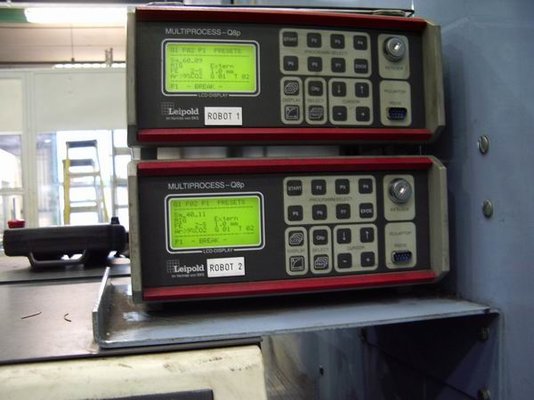
Weld controller, the "brain" stores the weld parameters for each individual weld. When the robot is ready to start a weld the controller switches on the power source and wire feed unit then monitors the weld characteristics.
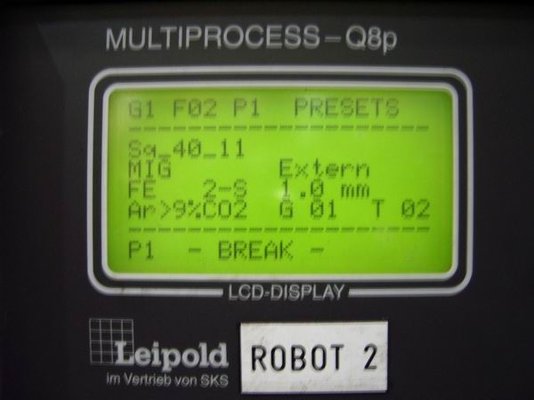
Close up of weld controller screen.
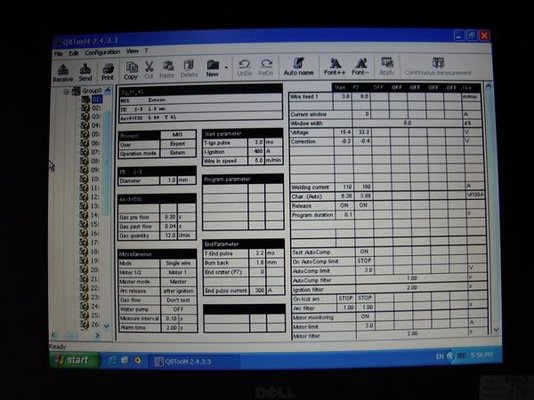
Weld controllers are networked to a central PC to allow process monitoring and changes to be made.
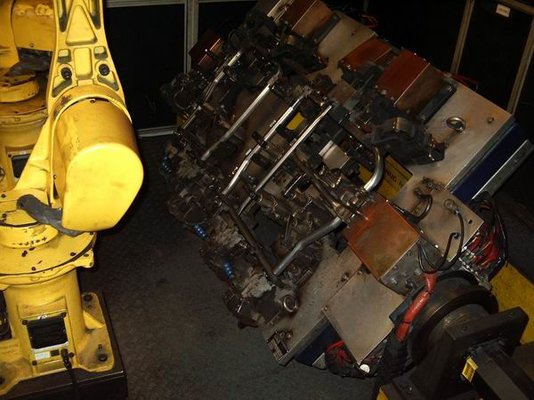
Components are loaded into a fixture then indexed 180° to face the robots.
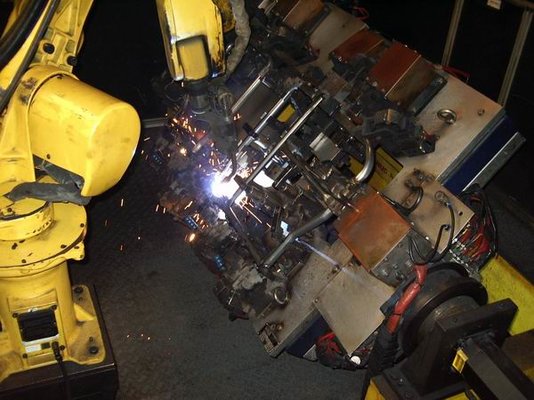
Component is welded by 2 robots to reduce cycle time.
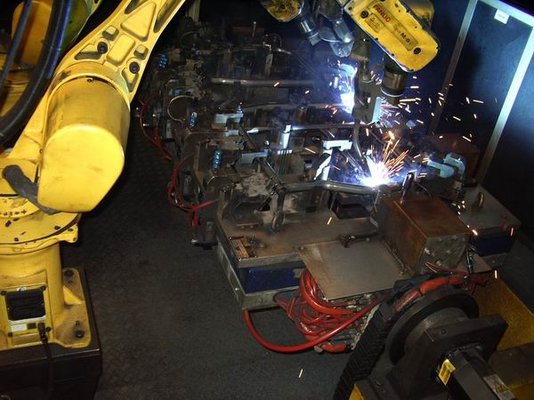
Fixture position is controlled by master robot to give best access to welds.
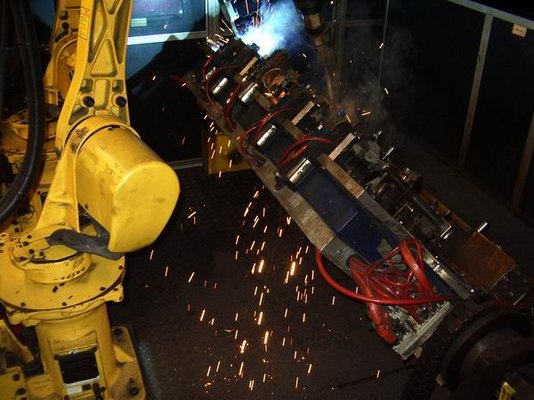
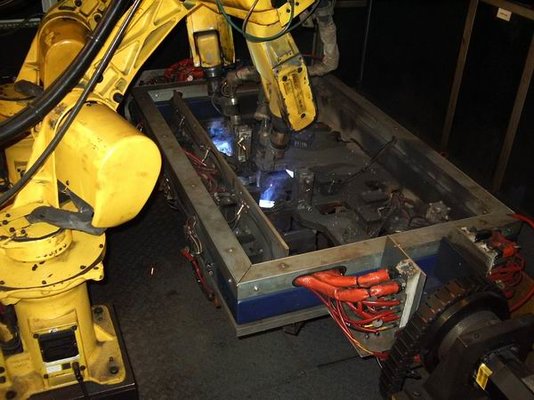
Fixture can be rotated upto 360°.
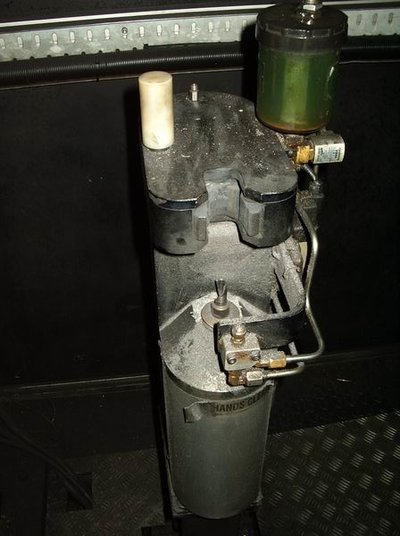
Every 3rd cycle the robots go to a torch cleaning station to have spatter removed by a reamer and a squirt of anti-spatter, there is also an air blast through the torch to remove any bits.
Each welding cell is controlled by a PLC (industrial computer) any weld failures are detected and flagged up to the operator.
Some of our cells have nearly 100 welds per cycle!
Thanks to Keiper UK for allowing me to photograph equipment.