Paul.
Moderator
- Messages
- 7,052
- Location
- Northampton. UK
A couple of people have recently asked me if I could give a few details of some of the stainless work that I produce, so without giving away too many trade secrets or boring you with basic stuff, here is a few pictures of the manufacture of a small stainless handrail come barrier.
This railing is made from 2" dull polished tube, the joints will be made from pre formed dairy fittings,
when there are several joints its best to make up small sub assembly's and clean them up while they are easy to handle, so first the tee in the middle, welded appearance not important here as its being cleaned off, but a full weld profile with no undercut or crevices is essential, I don't want to be welding up pinholes that may appear when polishing,
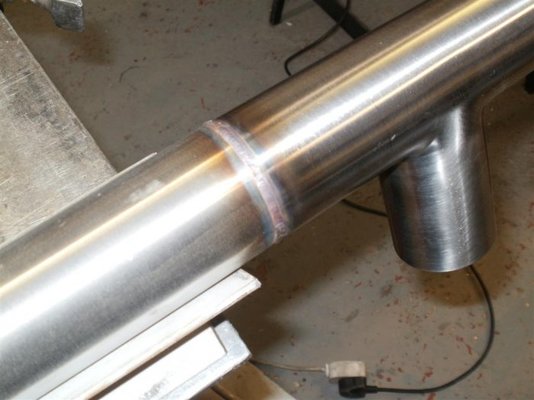
Then I work some magic on it, with a flap wheel in the die grinder, can you see the join.
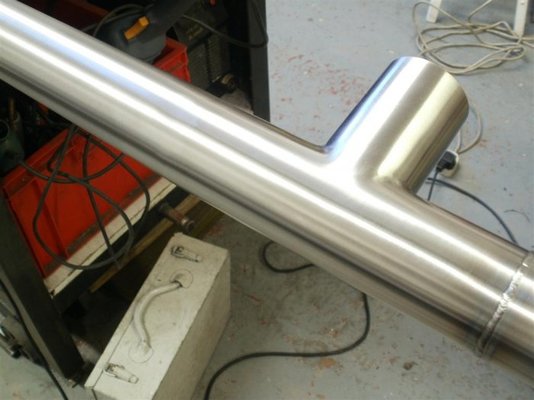

same with the bends for the ends,
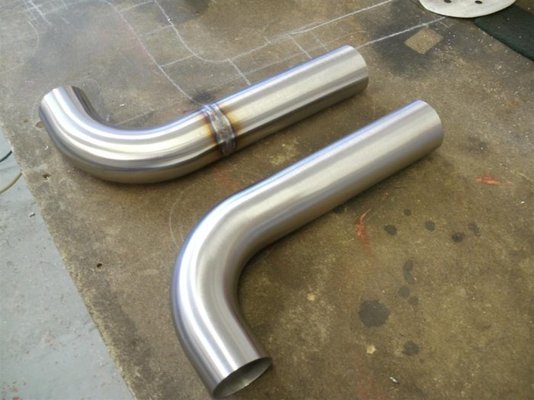
The legs need to be notched to form a nice tight joint, a bit of careful setting up with a 2" holesaw in the bench drill is all you need,
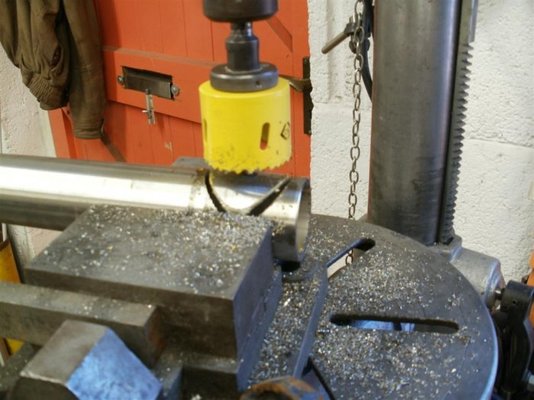
A touch with a flapdisk to finish them off, and ready for assembly.
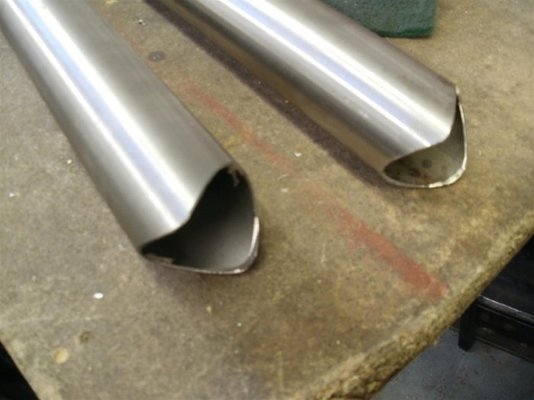
I knew those angle clamps would come in handy.
The mounting plates are 3mm thick, bent on the flypress, then deburred and dull polished
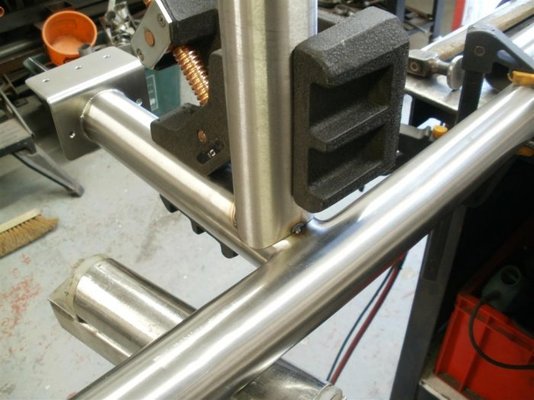
The finished item, final cleaning just done with soapy water and scotchbrite working with the grain, a couple of places needed a rub with a garryson abrasive block to remove some minor scratches,
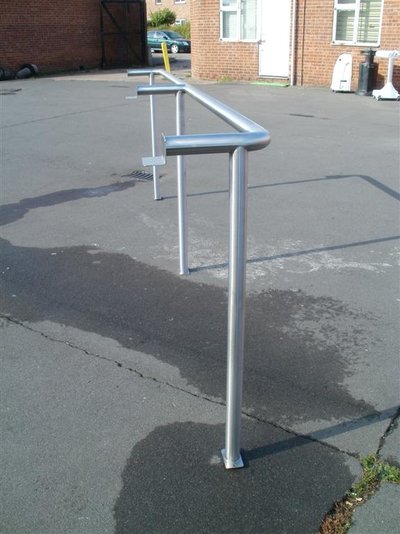
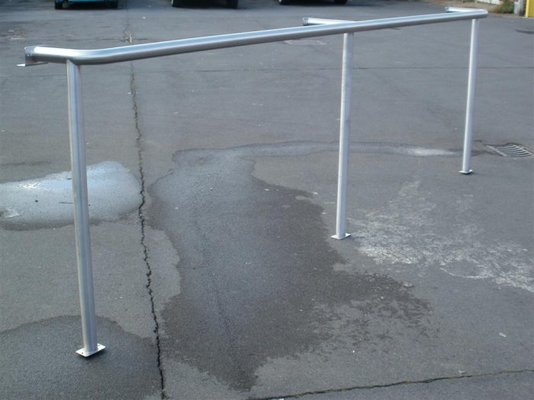
It's to fit in front of a reception counter at a clinic, they have had problems with clients leaning over the the counter to reach paperwork etc, and on a couple of occaisions even spitting at the staff. so hopefully this will keep them a bit further away.
This railing is made from 2" dull polished tube, the joints will be made from pre formed dairy fittings,
when there are several joints its best to make up small sub assembly's and clean them up while they are easy to handle, so first the tee in the middle, welded appearance not important here as its being cleaned off, but a full weld profile with no undercut or crevices is essential, I don't want to be welding up pinholes that may appear when polishing,
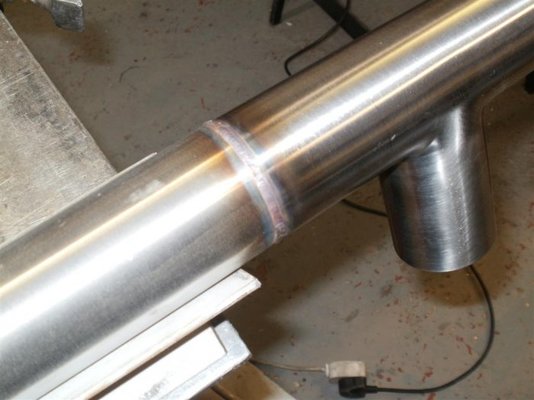
Then I work some magic on it, with a flap wheel in the die grinder, can you see the join.
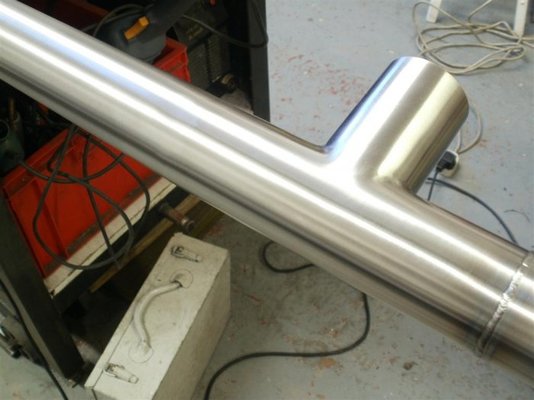

same with the bends for the ends,
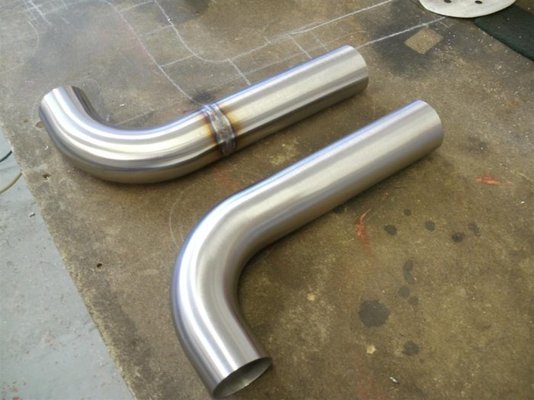
The legs need to be notched to form a nice tight joint, a bit of careful setting up with a 2" holesaw in the bench drill is all you need,
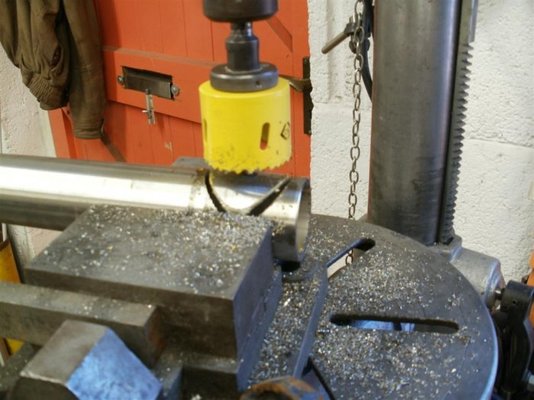
A touch with a flapdisk to finish them off, and ready for assembly.
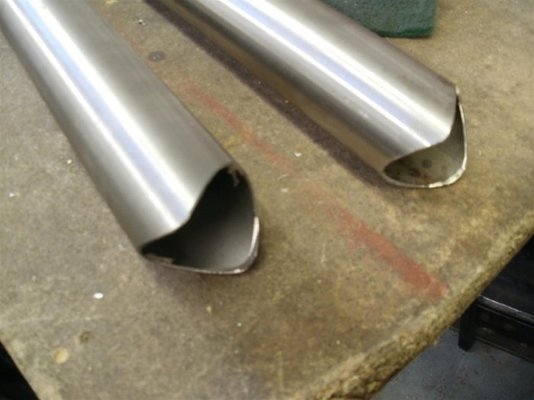
I knew those angle clamps would come in handy.
The mounting plates are 3mm thick, bent on the flypress, then deburred and dull polished
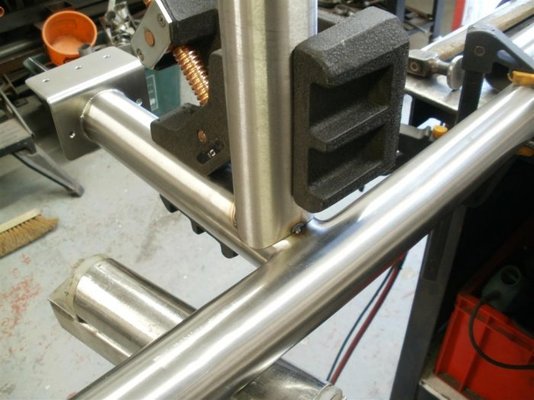
The finished item, final cleaning just done with soapy water and scotchbrite working with the grain, a couple of places needed a rub with a garryson abrasive block to remove some minor scratches,
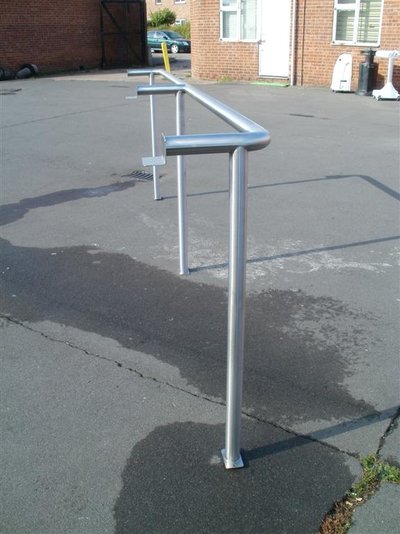
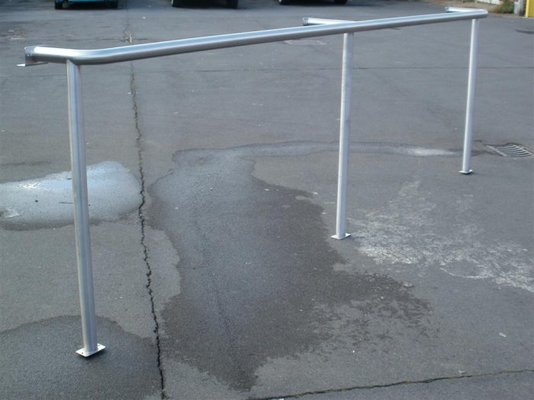
It's to fit in front of a reception counter at a clinic, they have had problems with clients leaning over the the counter to reach paperwork etc, and on a couple of occaisions even spitting at the staff. so hopefully this will keep them a bit further away.