Paul99
Member
- Messages
- 606
This thread is a follow up on an old thread where I was asking for advice on sourcing a CV joint for our Pel-job Dumper: http://www.mig-welding.co.uk/forum/threads/cv-joint-help.47287/
Since then I have had a few PMs from others who had suffered the same failure (looks to be a common fault in old age) and were struggling also to find a solution and I promised if I ever did come up with something I would put it up here as it may just help others out...
A mechanic friend had been saving up all his scrap CV joints for me to try - we ruled out a few different makes and models over the last few months and had all but given up on finding a matching spline configuration. Yesterday I called in again to try a few more but failed again at which point he takes a better look at it and says "that looks like a Vauxhall fit to me" well less than a minute later he had called one of his motor factor suppliers confirmed the size and number of internal splines and had got them to send one out on the van to be delivered that afternoon :O - I was pretty skeptical that it was any good but said no matter they'll take it back with them if it's no good. I had to leave the shaft with him and get off to work. Well it turned up and unbelievably the splines are a perfect fit on the pel-job shaft... happy days
For those that maybe reading and want to do the same the CV Joint was for a
2001 2.0l Vauxhall Vectra - though I got the impression from the mechanic it would fit many vauxhall models. Anyway the link to exact one here:
http://www.eurocarparts.com/ecp/c/V...82c0792d8ada38840926cea0f49b389bdcf3f4&000095
What you get (and the old parts on the right):
Model / part number:
And so with at least a decent fitting CV joint to work with I get onto modifying it to fit...
A 100m diameter flange plate is needed - not wanting to cut the old broken CV joint up (in-case I had to look at getting it rebuilt if this experiment didn't work) I roughed out a disc from some 10mm MS Plate with the plasma cutter. I drilled out the center to take a 16mm bolt to be able to mount it in the lathe and turn it down to a decent circle I then bored out (actually cheated and used a hole saw) the center to 30mm or so to clear the nut on the transfer box. I had also at this point tapped off the ABS ring to give better access for welding later:
I then cut off the outer splined shaft with the grinder and faced the end in the lathe - It's case hardened and was a major struggle with my old underpowered lathe but got there eventually:
Having disassembled the joint in case the welding heat damaged the cage or bearings somehow it was time to weld it the flange on - I mounted it all in the lathe used a jacobs chuck in the tailstock to apply pressure and after a few adjustments and using a dial gauge got it fairly well centered before tacking it in place - TBH that was overkill as having welded it up fully I chucked up the CV joint and then skimmed a bit off the flange to true it up and then faced it off too. That done I marked the holes center punched and then drilled out the holes:
The first picture shows that the mounting bolts will be a tight fit - I did have to shorten them up a bit to get them through - it works but If I had to do it again I'd probably cut the flange off the old joint and weld that on to give a bit more room to get the bolts through.
That was the hard part done now just time to re-assemble the joint, grease it, clip it onto the shaft add the gaiter:
And just to show that it does fit:
A quick test on full lock both ways - no clicking, grinding and 4WD is definitely working again - couldn't have wished for a better outcome for £30. I can't see any reason why it wouldn't stand up to hard work - only time will tell but TBH for that sort of money I don't mind if I have to repeat the process every few years.
Hopefully this will have been of some help to others out there who have the same problem...
Paul.
Since then I have had a few PMs from others who had suffered the same failure (looks to be a common fault in old age) and were struggling also to find a solution and I promised if I ever did come up with something I would put it up here as it may just help others out...
A mechanic friend had been saving up all his scrap CV joints for me to try - we ruled out a few different makes and models over the last few months and had all but given up on finding a matching spline configuration. Yesterday I called in again to try a few more but failed again at which point he takes a better look at it and says "that looks like a Vauxhall fit to me" well less than a minute later he had called one of his motor factor suppliers confirmed the size and number of internal splines and had got them to send one out on the van to be delivered that afternoon :O - I was pretty skeptical that it was any good but said no matter they'll take it back with them if it's no good. I had to leave the shaft with him and get off to work. Well it turned up and unbelievably the splines are a perfect fit on the pel-job shaft... happy days
For those that maybe reading and want to do the same the CV Joint was for a
2001 2.0l Vauxhall Vectra - though I got the impression from the mechanic it would fit many vauxhall models. Anyway the link to exact one here:
http://www.eurocarparts.com/ecp/c/V...82c0792d8ada38840926cea0f49b389bdcf3f4&000095
What you get (and the old parts on the right):
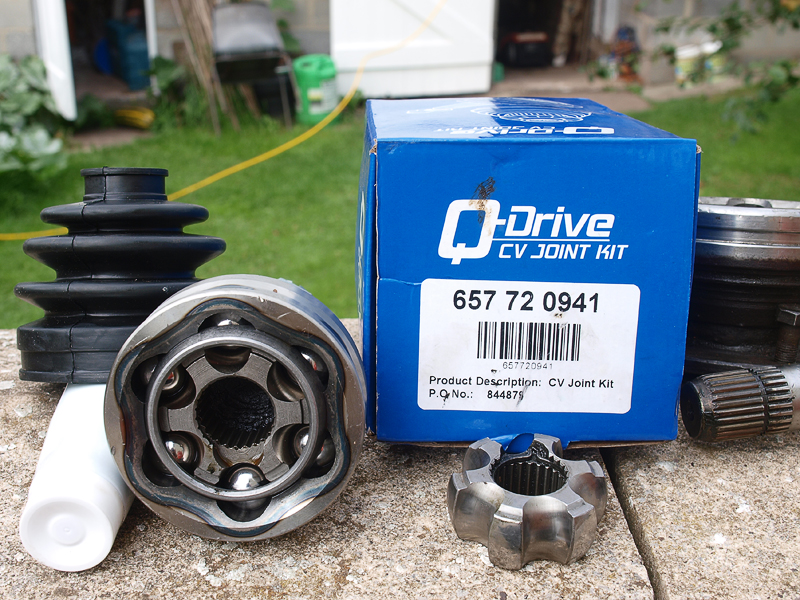
Model / part number:

And so with at least a decent fitting CV joint to work with I get onto modifying it to fit...
A 100m diameter flange plate is needed - not wanting to cut the old broken CV joint up (in-case I had to look at getting it rebuilt if this experiment didn't work) I roughed out a disc from some 10mm MS Plate with the plasma cutter. I drilled out the center to take a 16mm bolt to be able to mount it in the lathe and turn it down to a decent circle I then bored out (actually cheated and used a hole saw) the center to 30mm or so to clear the nut on the transfer box. I had also at this point tapped off the ABS ring to give better access for welding later:

I then cut off the outer splined shaft with the grinder and faced the end in the lathe - It's case hardened and was a major struggle with my old underpowered lathe but got there eventually:

Having disassembled the joint in case the welding heat damaged the cage or bearings somehow it was time to weld it the flange on - I mounted it all in the lathe used a jacobs chuck in the tailstock to apply pressure and after a few adjustments and using a dial gauge got it fairly well centered before tacking it in place - TBH that was overkill as having welded it up fully I chucked up the CV joint and then skimmed a bit off the flange to true it up and then faced it off too. That done I marked the holes center punched and then drilled out the holes:

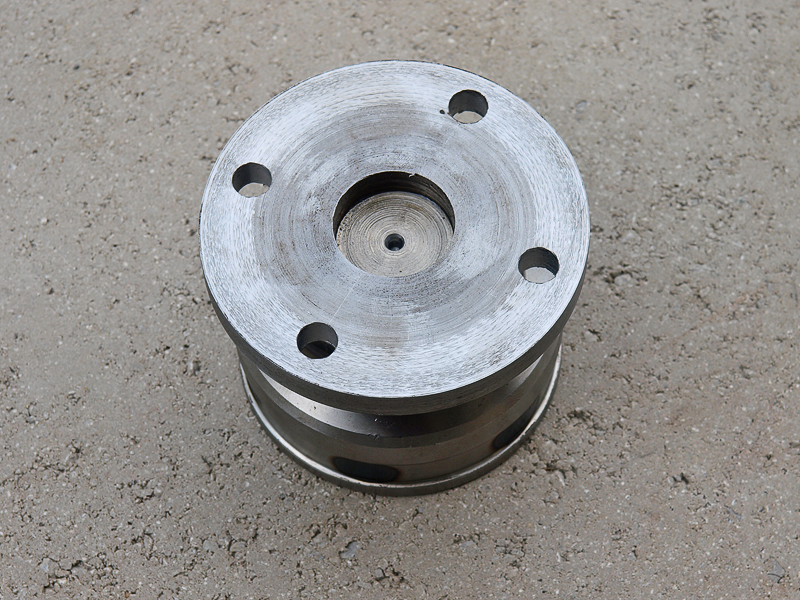
The first picture shows that the mounting bolts will be a tight fit - I did have to shorten them up a bit to get them through - it works but If I had to do it again I'd probably cut the flange off the old joint and weld that on to give a bit more room to get the bolts through.
That was the hard part done now just time to re-assemble the joint, grease it, clip it onto the shaft add the gaiter:

And just to show that it does fit:

A quick test on full lock both ways - no clicking, grinding and 4WD is definitely working again - couldn't have wished for a better outcome for £30. I can't see any reason why it wouldn't stand up to hard work - only time will tell but TBH for that sort of money I don't mind if I have to repeat the process every few years.
Hopefully this will have been of some help to others out there who have the same problem...
Paul.
Last edited: