shenion
Tool Pack Rat
- Messages
- 7,586
- Location
- Stone Mountain, GA USA
Been discussion on the lathe forums about using Treadmill motors. Thought this might be interesting to others.
Neighbor threw out a Proform Treadmill. Needed new belt and control panel a bit beat up, but it worked.
Took it apart and found the motor and controller basically worked standalone and did not need all the rest of the control panel. Only control is the speed pot.
On the back of the controller is a choke. The controller is an MC-60 and is straightforward. Two AC in lines, +/- to motor and 3 lines to the speed pot.
The motor is 130VDC, 2 1/4HP, 6500 RPM. With the controller, it looks to only reach about half speed.
Shaft is an odd size and too big for the drill press pulley. So it was chucked up in the lathe. The bearing worked well with the steady rest:
I made a fan out of sheet metal and welded it to a collar. Note the motor has a flywheel with a centrifugal fan. It got in the way.
This really pulls a lot of air through the motor; most does go straight out the sides.
Will need to make some sleeves to support the flange properly:
Final result with controller mounted in an old ammo box:
Old motor was made into a bench grinder.
Has much more torque, less vibration and slower speed. Can finally drill steel without melting bits.
First time I felt my $0.99 ebay deal was worth using
Neighbor threw out a Proform Treadmill. Needed new belt and control panel a bit beat up, but it worked.
Took it apart and found the motor and controller basically worked standalone and did not need all the rest of the control panel. Only control is the speed pot.
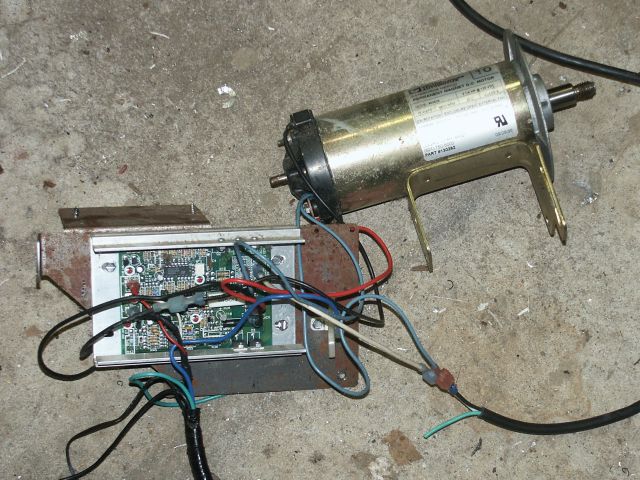
On the back of the controller is a choke. The controller is an MC-60 and is straightforward. Two AC in lines, +/- to motor and 3 lines to the speed pot.
The motor is 130VDC, 2 1/4HP, 6500 RPM. With the controller, it looks to only reach about half speed.
Shaft is an odd size and too big for the drill press pulley. So it was chucked up in the lathe. The bearing worked well with the steady rest:
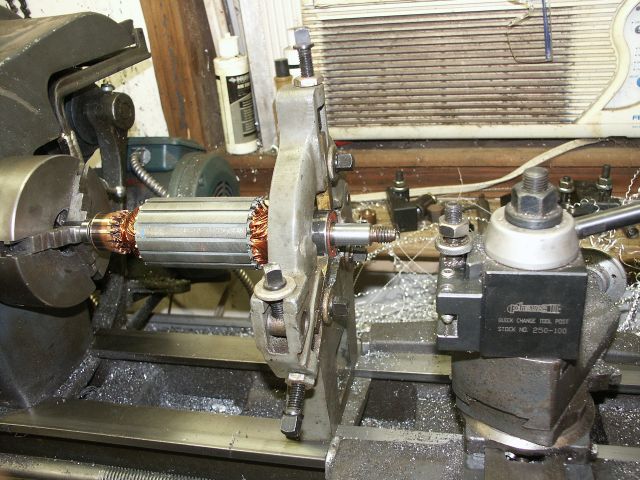
I made a fan out of sheet metal and welded it to a collar. Note the motor has a flywheel with a centrifugal fan. It got in the way.
This really pulls a lot of air through the motor; most does go straight out the sides.
Will need to make some sleeves to support the flange properly:
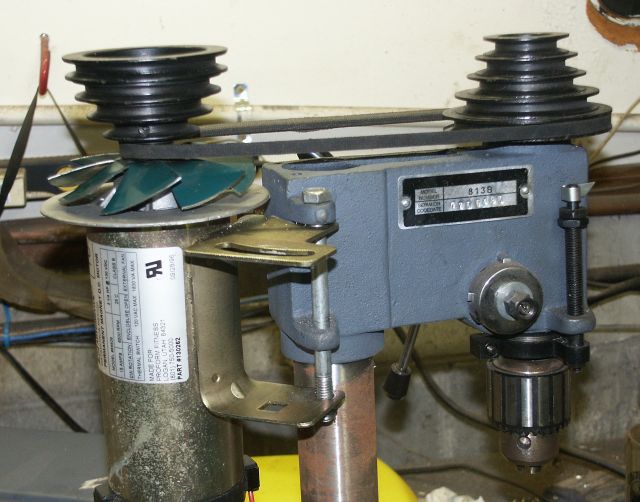
Final result with controller mounted in an old ammo box:
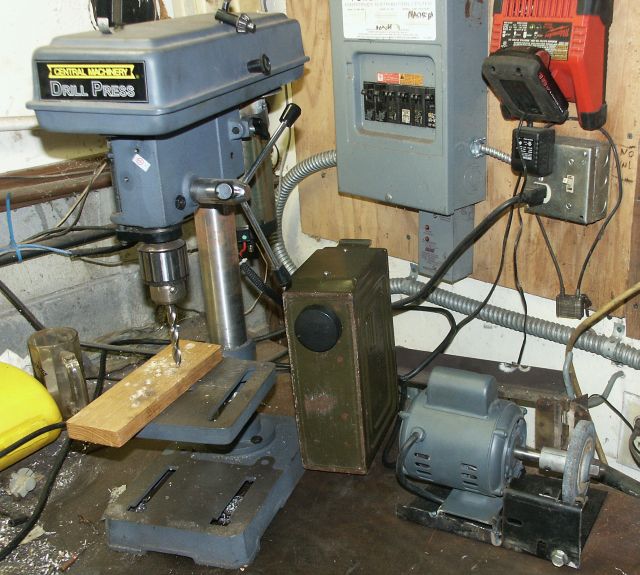
Old motor was made into a bench grinder.
Has much more torque, less vibration and slower speed. Can finally drill steel without melting bits.
First time I felt my $0.99 ebay deal was worth using
