Well here is a project I did in my last year at school. I've been meaning to put some photo's up for a while but I've only just got hold of some. This consumed mine and a friends lives for the best part of a year. We were so determined to finish it before we left that we were still tinkering an hour before our maths A-Level! 
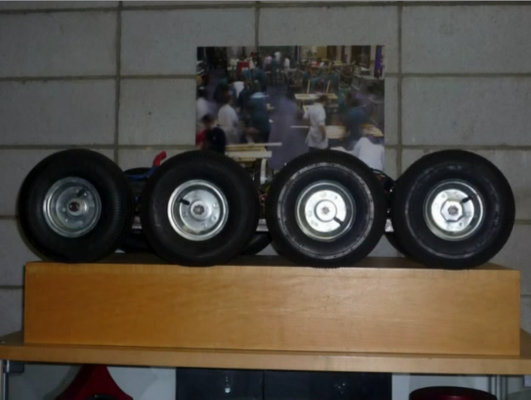
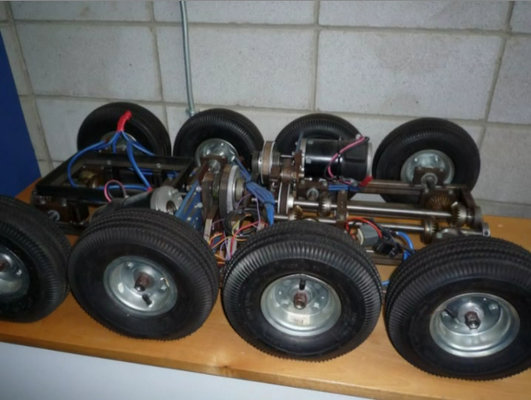
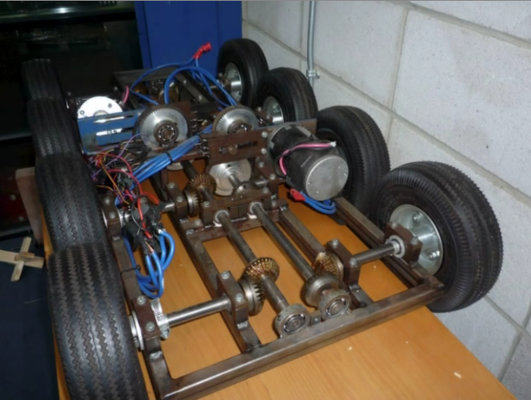
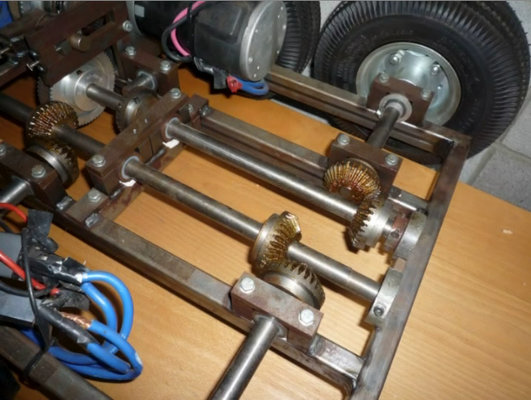
Basically, it's a model argocat, about the length of the average office desk. It's powered by a car battery and two electric motors. Pretty much anything you can see was made by me or my mate. All the electrical components were bought, as were the bearings at the ends of the long shafts, the wheels and the belts and pulleys.
Things we made included the chassis, 16 steel bushes with nylon inserts, all shafts and stub axles, oversize aluminium washers, PVC wheel hub inserts, motor mounting plates and, belt tensioners, the biggest labour of love, 16 bevel gears. Actually I lie, we made 15 bevel gears and broke the involute cutter on the 16th. By that time we were so fed up of them we left it so one wheel is just free spinning!
Due to the constraints of time and , probably more importantly, money there are many things that are less than perfect. For example, we couldn't afford electronic speed controllers and didn't have time to build one from scratch so there aren't any. The motors are controlled by a relay and a microswitch taped to the side of a servo off a model car. This means there are three separate circuits which is less than ideal. It also means there is a huge starting torque which caused the belts to slip initially.
One of the other biggest problems was the type of motors. I salvaged them from something else but they had long, thin shafts, rather than short fat ones that would have been better suited. Consequently, the thing only ever ran for 30 mins total since the shaft snapped off one of the motors.
The long shafts flexed in the middle so we had to add extra bushes to keep them in line.
We both learnt an enormous amount while building this thing. One of those lessons (with all these lessons learned I could be a politician) was not to weld too much on one side of your chassis! Did you notice the wedges under the bushes in the centre of the longitudinal shaft? Well they're there because the whole chassis is bowed out by about 5mm either end after I got carried away welding on the 'bridge' over the top. What can I say, I was having fun!
Needless to say, I'd love to build it again and put all the things right. Unfortunately I no longer have all the kit available to me that I did at school so it'll have to wait. Probably until my retirement.
P.S Spot the novel use of Jubilee clips.

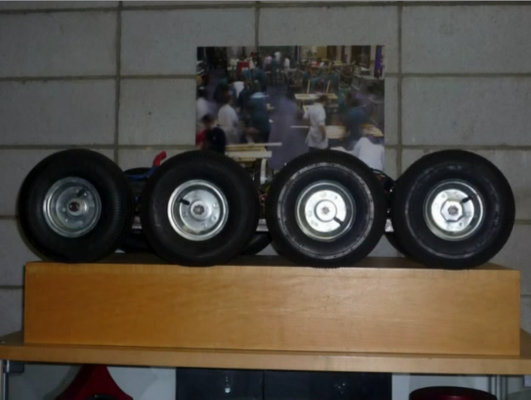
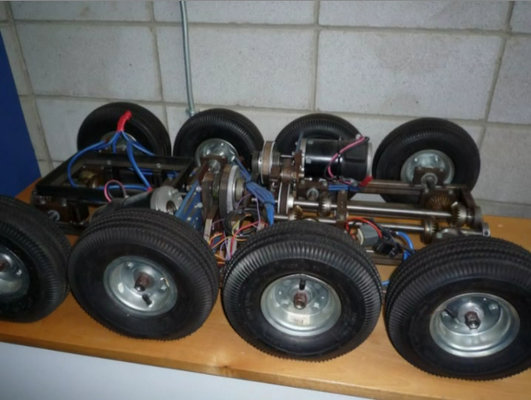
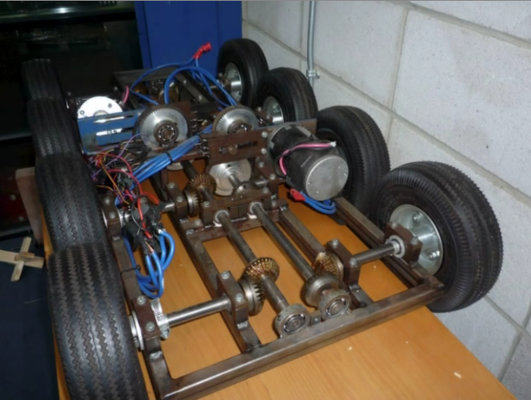
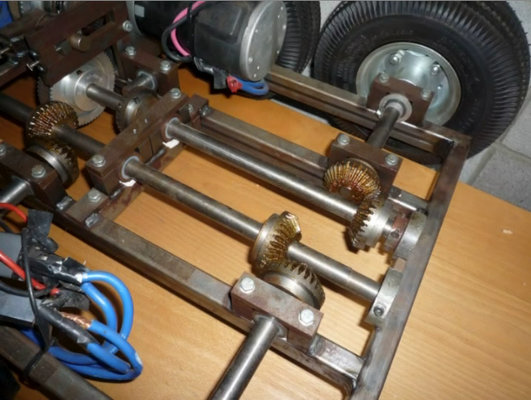
Basically, it's a model argocat, about the length of the average office desk. It's powered by a car battery and two electric motors. Pretty much anything you can see was made by me or my mate. All the electrical components were bought, as were the bearings at the ends of the long shafts, the wheels and the belts and pulleys.
Things we made included the chassis, 16 steel bushes with nylon inserts, all shafts and stub axles, oversize aluminium washers, PVC wheel hub inserts, motor mounting plates and, belt tensioners, the biggest labour of love, 16 bevel gears. Actually I lie, we made 15 bevel gears and broke the involute cutter on the 16th. By that time we were so fed up of them we left it so one wheel is just free spinning!
Due to the constraints of time and , probably more importantly, money there are many things that are less than perfect. For example, we couldn't afford electronic speed controllers and didn't have time to build one from scratch so there aren't any. The motors are controlled by a relay and a microswitch taped to the side of a servo off a model car. This means there are three separate circuits which is less than ideal. It also means there is a huge starting torque which caused the belts to slip initially.
One of the other biggest problems was the type of motors. I salvaged them from something else but they had long, thin shafts, rather than short fat ones that would have been better suited. Consequently, the thing only ever ran for 30 mins total since the shaft snapped off one of the motors.
The long shafts flexed in the middle so we had to add extra bushes to keep them in line.
We both learnt an enormous amount while building this thing. One of those lessons (with all these lessons learned I could be a politician) was not to weld too much on one side of your chassis! Did you notice the wedges under the bushes in the centre of the longitudinal shaft? Well they're there because the whole chassis is bowed out by about 5mm either end after I got carried away welding on the 'bridge' over the top. What can I say, I was having fun!

Needless to say, I'd love to build it again and put all the things right. Unfortunately I no longer have all the kit available to me that I did at school so it'll have to wait. Probably until my retirement.

P.S Spot the novel use of Jubilee clips.
