MattH
Member
- Messages
- 4,522
- Location
- Cornwall
I need to mount a new water cooled spindle onto my Tekcel CNC router, replacing the Perske spindle with its terrible Syoz collets.
The new spindle is round and came with a mounting clamp but it is in a rough cast form.
I need to machine the base of the clamp flat and parallel and add a key way and mounting holes. I then need to machine a new spindle plate to bolt everything to.
First problem, how to clamp the mount securely for milling:
This was a mockup of the clamping, I have a set of 6" vee blocks but they are not a matched pair and therefore the spindle is not parallel. The tiny vee blocks in the pic are all I have and are not big enough to secure the spindle and clamp. I could buy some new vee blocks but I felt it would be better to build a jig out of some 5" round material.
I wanted some steel pipe that I could weld a piece of angle onto each end and then shim to true but I couldn't find any. I did get a peice of 6" aluminium billet so I have started to machine that.
First is to turn it down to 125mm diameter:
Then I added a M16 threaded hole:
With that work done I need to attach my large 4 jaw chuck and turn the peice around to complete the turning on the other end.
In this pic you can see the old spindle and plate in the background:
More to follow tomorrow.
The new spindle is round and came with a mounting clamp but it is in a rough cast form.
I need to machine the base of the clamp flat and parallel and add a key way and mounting holes. I then need to machine a new spindle plate to bolt everything to.
First problem, how to clamp the mount securely for milling:
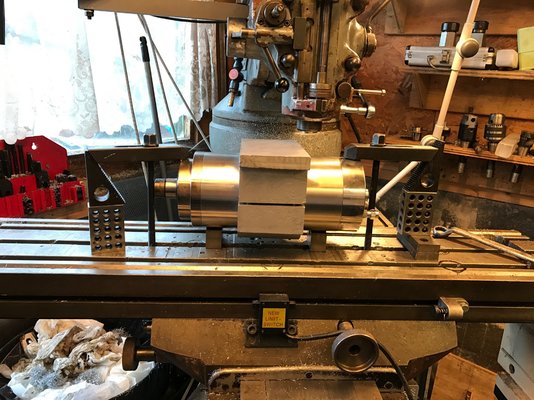
This was a mockup of the clamping, I have a set of 6" vee blocks but they are not a matched pair and therefore the spindle is not parallel. The tiny vee blocks in the pic are all I have and are not big enough to secure the spindle and clamp. I could buy some new vee blocks but I felt it would be better to build a jig out of some 5" round material.
I wanted some steel pipe that I could weld a piece of angle onto each end and then shim to true but I couldn't find any. I did get a peice of 6" aluminium billet so I have started to machine that.
First is to turn it down to 125mm diameter:
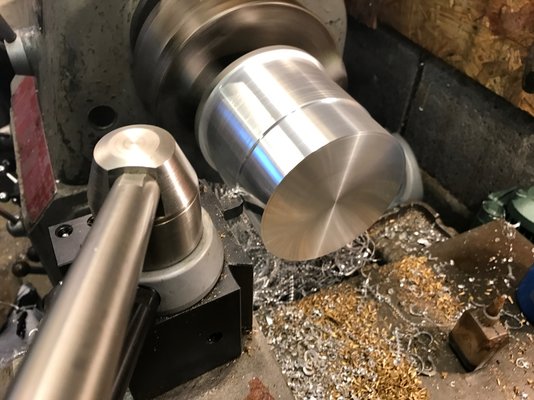
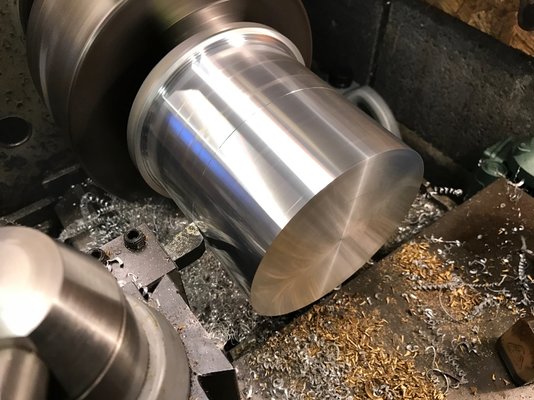
Then I added a M16 threaded hole:
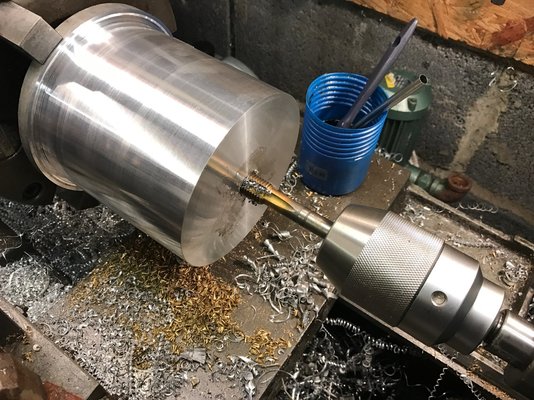
With that work done I need to attach my large 4 jaw chuck and turn the peice around to complete the turning on the other end.
In this pic you can see the old spindle and plate in the background:
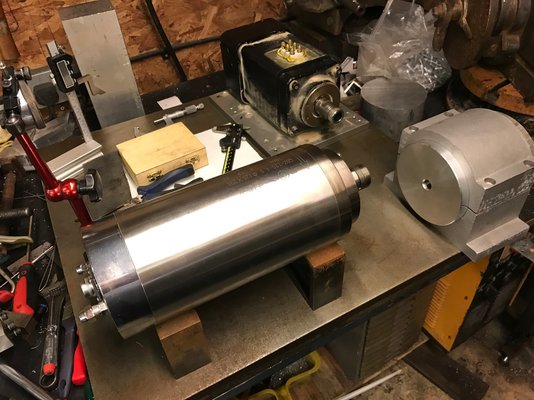
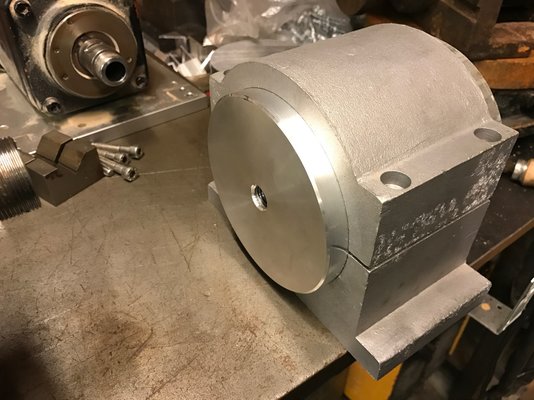
More to follow tomorrow.