wyn
Member
- Messages
- 3,656
- Location
- Cardiff
Picked up an old compressor from work that was going to be chucked away and thought it would be a good one for my shed. It was a bit heavy so had to take the pump off the top of the receiver to shift it home. It was labeled up as a Tecalemit but thanks to "eil" i now know it's an Ingersoll Rand T30. Made in 1968.
When the pump was off i could see the pulley was a bit wobbly and on a bit of further inspection the shaft was a bit out. So i stripped it down and "adjusted" it a bit on the lathe to get it a bit better.
I'm now at the stage where it has been rebuilt and cleaned up and also had it running over the last couple of days.
Here are a couple of pics .
This is a pic of the pump on it's way to it's new home
Striping it down on the bench
The pressure unloader governor thingy
When the pump is running the weights on the end of the shaft are thrown outwards and a valve that goes up against the centre of the shaft is held closed.
When the pump stops, via the electrical pressure switch, the weights are pulled in on a spring and the valve is allowed to open. this then unloads the pressure from the tubing from the pump to the check valve in the top of the receiver
The pump going back together.
Didn't think i would be able to get proper gaskets so just got gasket material and cut them to shape.
The little aluminium plate holds in a shim that was needed since the shaft had been machined smaller to get it straight
The receiver was a bit rusty inside so i welded a bit of tube each end, set them up on axle stands and put a few bits of scrap inside the tank. The scrap was put in through the inspection hatches and i sat there and turned it over and over for about half an hour.
This got rid of any loose rust. I was thinking of tipping some sort of sealer in when the rust was out, and giving it a spin to seal it. But i thought this was a bit over the top as the receiver is about 8 - 10 mm thick and the rust wasn't too bad. I worked it out as being around a 142 litre capacity ( it only had imperial dimensions on the data plate)
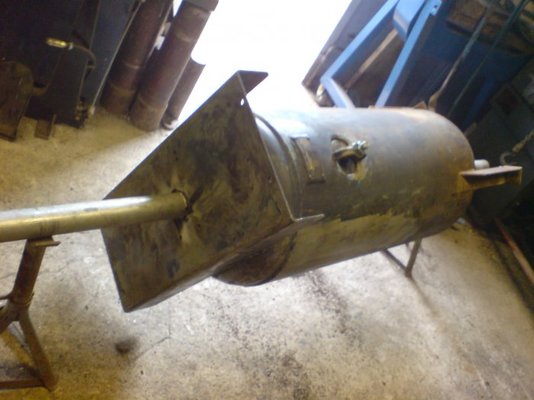
I was thinking about painting it in that sort of old machine tool grey but couldn't get any locally.....so matt black it was.
It seems to go ok with the polished brass and copper bits.
The gap between the cylinders was looking a bit sort of empty, so filled it up with a new air filter and intake manifold
Ready for the motor
3 hp Motor on
Testing it out.
The receiver was marked up as being good for 200 psi, but because it's knocking on a bit i'll keep it under 150 psi.
I'm now making up a guard for it. When it's in position i may link it to a propane bottle, i also have a couple of large industrial filters that will be plumbed in straight after the receivers.
More pics when it's in position and done.
A couple more pics Here.
When the pump was off i could see the pulley was a bit wobbly and on a bit of further inspection the shaft was a bit out. So i stripped it down and "adjusted" it a bit on the lathe to get it a bit better.
I'm now at the stage where it has been rebuilt and cleaned up and also had it running over the last couple of days.
Here are a couple of pics .
This is a pic of the pump on it's way to it's new home
Striping it down on the bench
The pressure unloader governor thingy
When the pump is running the weights on the end of the shaft are thrown outwards and a valve that goes up against the centre of the shaft is held closed.
When the pump stops, via the electrical pressure switch, the weights are pulled in on a spring and the valve is allowed to open. this then unloads the pressure from the tubing from the pump to the check valve in the top of the receiver
The pump going back together.
Didn't think i would be able to get proper gaskets so just got gasket material and cut them to shape.
The little aluminium plate holds in a shim that was needed since the shaft had been machined smaller to get it straight
The receiver was a bit rusty inside so i welded a bit of tube each end, set them up on axle stands and put a few bits of scrap inside the tank. The scrap was put in through the inspection hatches and i sat there and turned it over and over for about half an hour.
This got rid of any loose rust. I was thinking of tipping some sort of sealer in when the rust was out, and giving it a spin to seal it. But i thought this was a bit over the top as the receiver is about 8 - 10 mm thick and the rust wasn't too bad. I worked it out as being around a 142 litre capacity ( it only had imperial dimensions on the data plate)
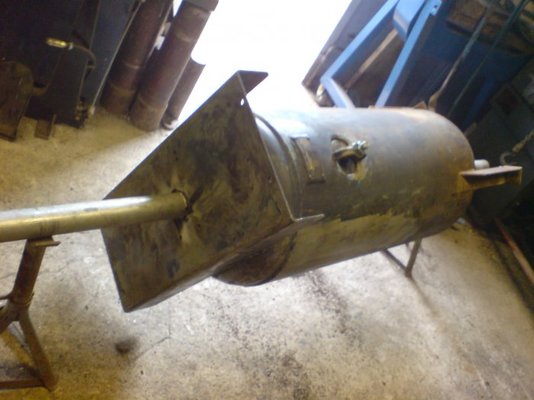
I was thinking about painting it in that sort of old machine tool grey but couldn't get any locally.....so matt black it was.
It seems to go ok with the polished brass and copper bits.
The gap between the cylinders was looking a bit sort of empty, so filled it up with a new air filter and intake manifold
Ready for the motor
3 hp Motor on
Testing it out.
The receiver was marked up as being good for 200 psi, but because it's knocking on a bit i'll keep it under 150 psi.
I'm now making up a guard for it. When it's in position i may link it to a propane bottle, i also have a couple of large industrial filters that will be plumbed in straight after the receivers.
More pics when it's in position and done.
A couple more pics Here.