OK I found an exhaust manifold that was tig welded a long time ago. And it cracked as many times as it was repaired (a long time ago too)
So i was observing this mani today, and i was wondering, what made some welds crack right next to the welds, while the next weld had cracked right in the middle. And why overall it cracked ? I only know that this manifold is 304 stainless.
IS this all because of :....
1) the famous carbide precipitation, (sensitization), chrome depletion, etc ?
2) Exceeding the heat stress capability of the parent metal ? (ok why it didnt crack somewhere along the pipe ?)
3) Poor root of the weld ?
4) Poor filler deposition (undersized welds) ?
5) Hardening of the weld ? (why?)
Here are some pics.
So i was observing this mani today, and i was wondering, what made some welds crack right next to the welds, while the next weld had cracked right in the middle. And why overall it cracked ? I only know that this manifold is 304 stainless.
IS this all because of :....
1) the famous carbide precipitation, (sensitization), chrome depletion, etc ?
2) Exceeding the heat stress capability of the parent metal ? (ok why it didnt crack somewhere along the pipe ?)
3) Poor root of the weld ?
4) Poor filler deposition (undersized welds) ?
5) Hardening of the weld ? (why?)
Here are some pics.
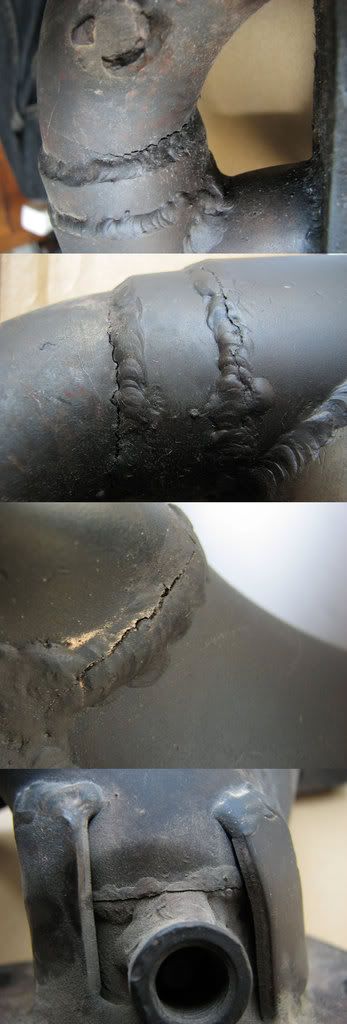