BChild
SIP - enough with the mods!!!!
- Messages
- 1,023
Background
So I borrowed an ancient Opel/Vauxhall tool to extract the door pins so I could remove the doors on my current track car project - 43 years they'd been in and they'd defeated the usual cranked arm machine mart tool (never found them to survive more than a couple of doors before they break) so I borrowed a better tool from a mate.
It's effectively a slide hammer on a thin steel rod with a removable end cap that is slightly under the size of a door pin hole and a few cracks on the slide hammer extracts the door pin easily
Three components
1 - steel shaft approx 60 cm long 10 mm Diameter tapering to 4-5 mm Diameter threaded at the end
2 - Slide hammer weight (approx 1 kg)
3 - Pin extraction tip (10 cm long diameter just under 8 mm threaded internally)
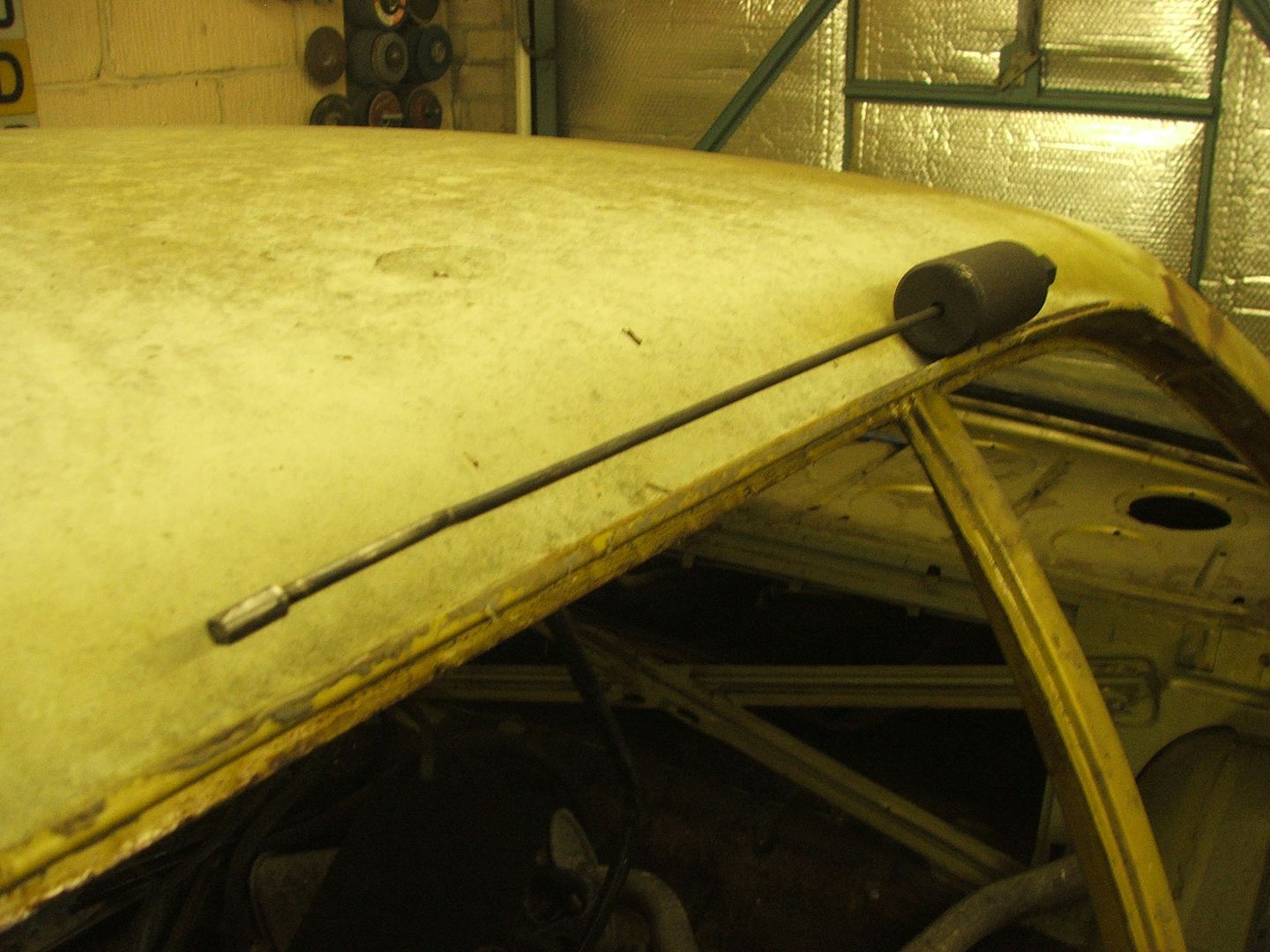
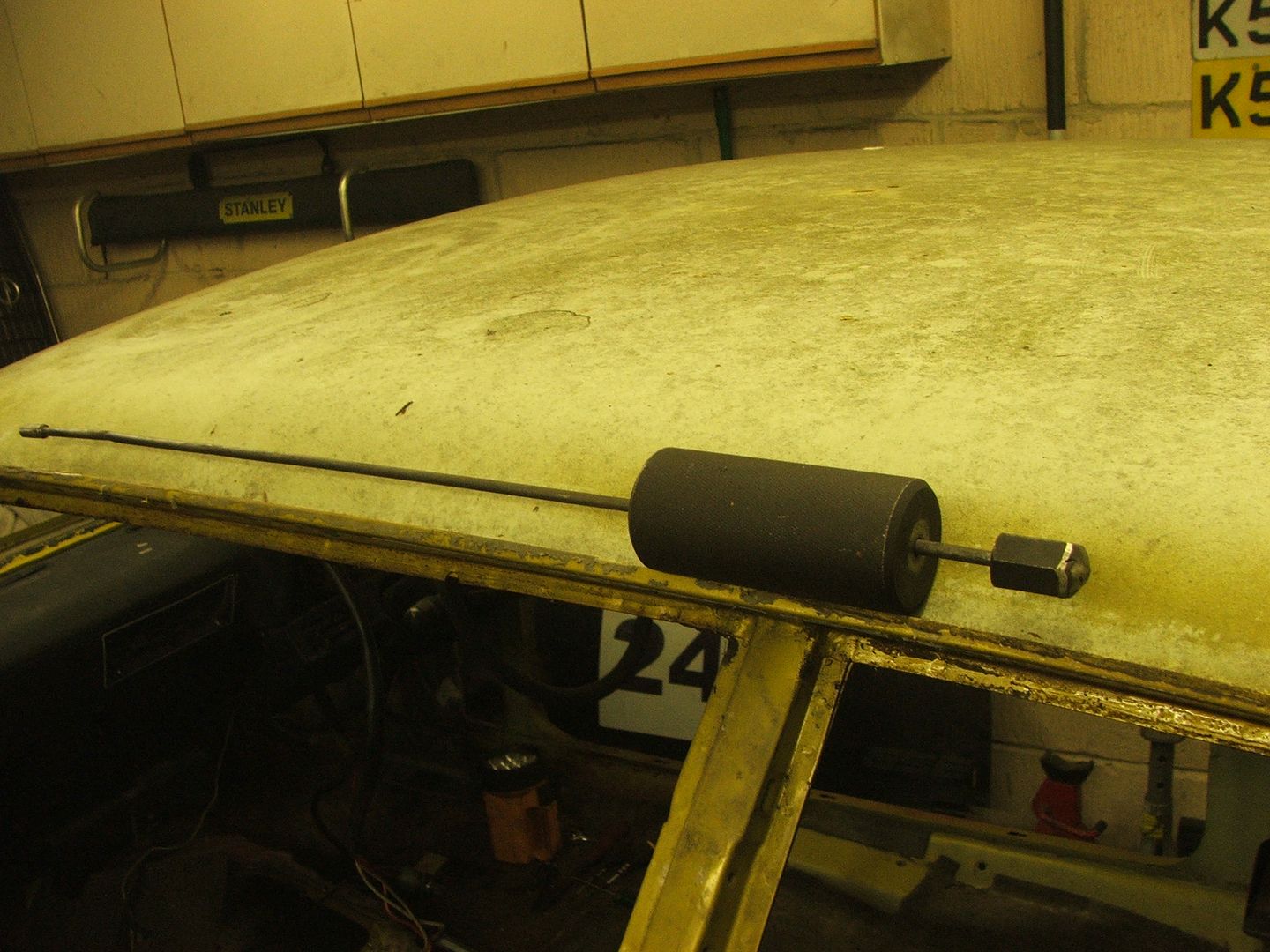
Now when I borrowed it I was warned that the thread was getting iffy and the ferule was a ground down nut as the original had been lost - it got one pin out and cried enough (15 years of door pin removal - it seemed fair service)
Now we all share borrow tools and the accepted rule is if you break or damage something you repair or replace. So I had to get it re-threaded at a "local" engineering shop and a decent sized ferule made up to reduce the load on the thread.
I asked if they would make me one - the engineer reckoned for a one off it would be quite expensive but for a few of them it would probably bring the labour element of the cost right down (material cost will always be the same)
So fixed and some drawings made and the rest of the pins came out just fine
Anyway I asked on the club forums if people were interested and I got a fairly good response.
I got a partial delivery today
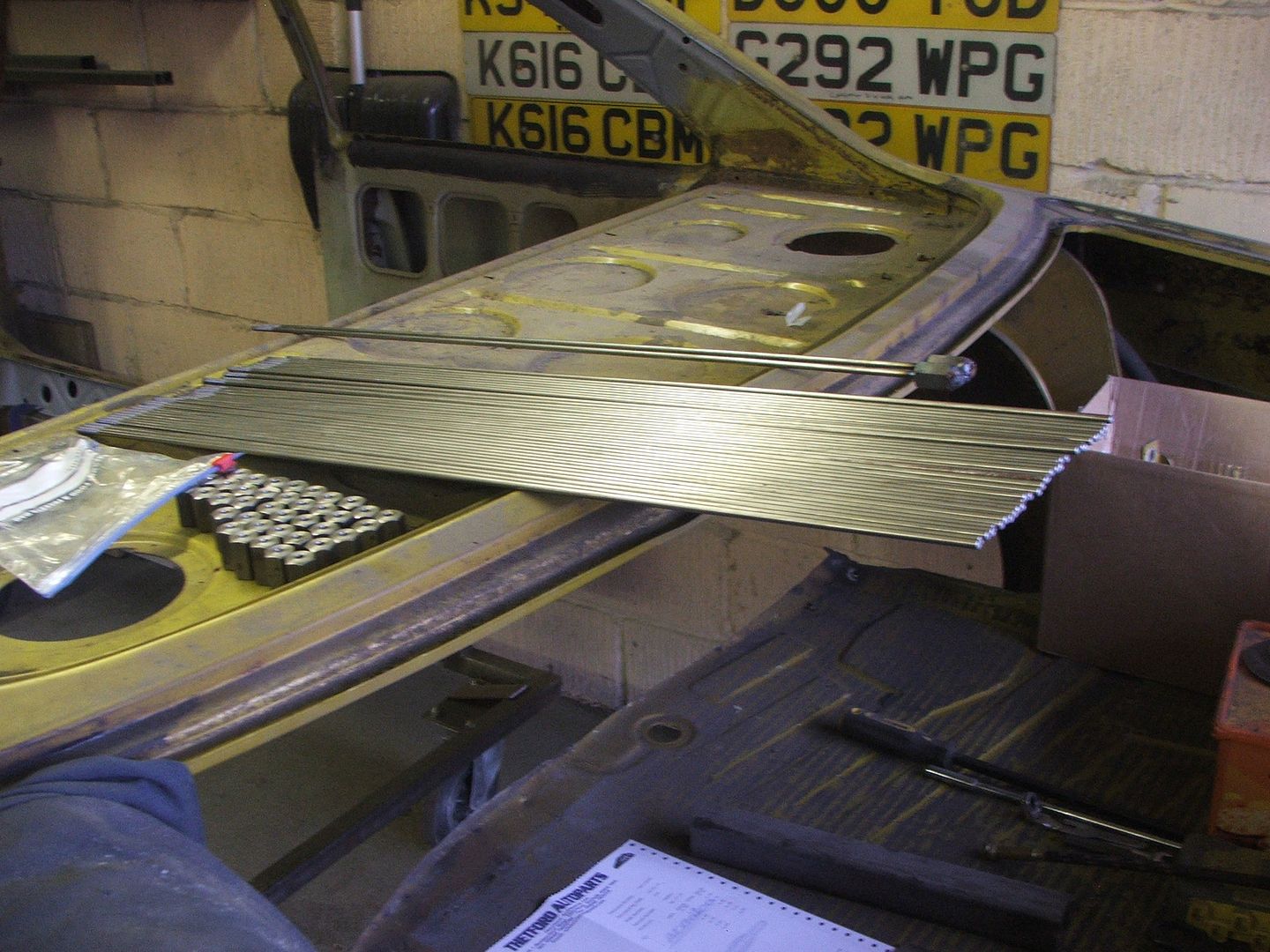
And
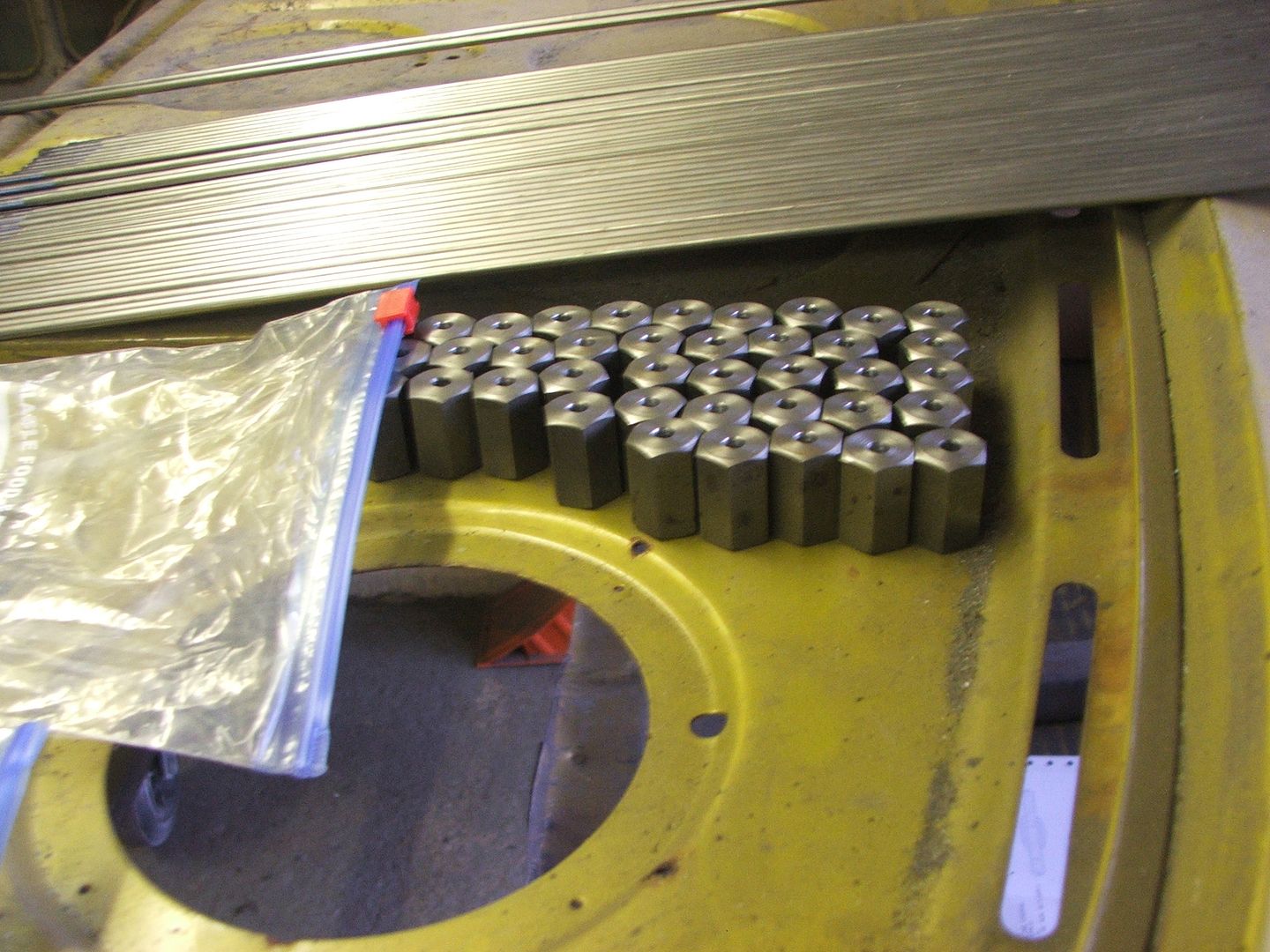
I got the ferules in EN24T with a nice flat either side at the end to make holding/doing up easy when it's thro the door pin
So as I think I mentioned earlier - the engineer can machine but not weld so that bit is down to me so I set up a little jig
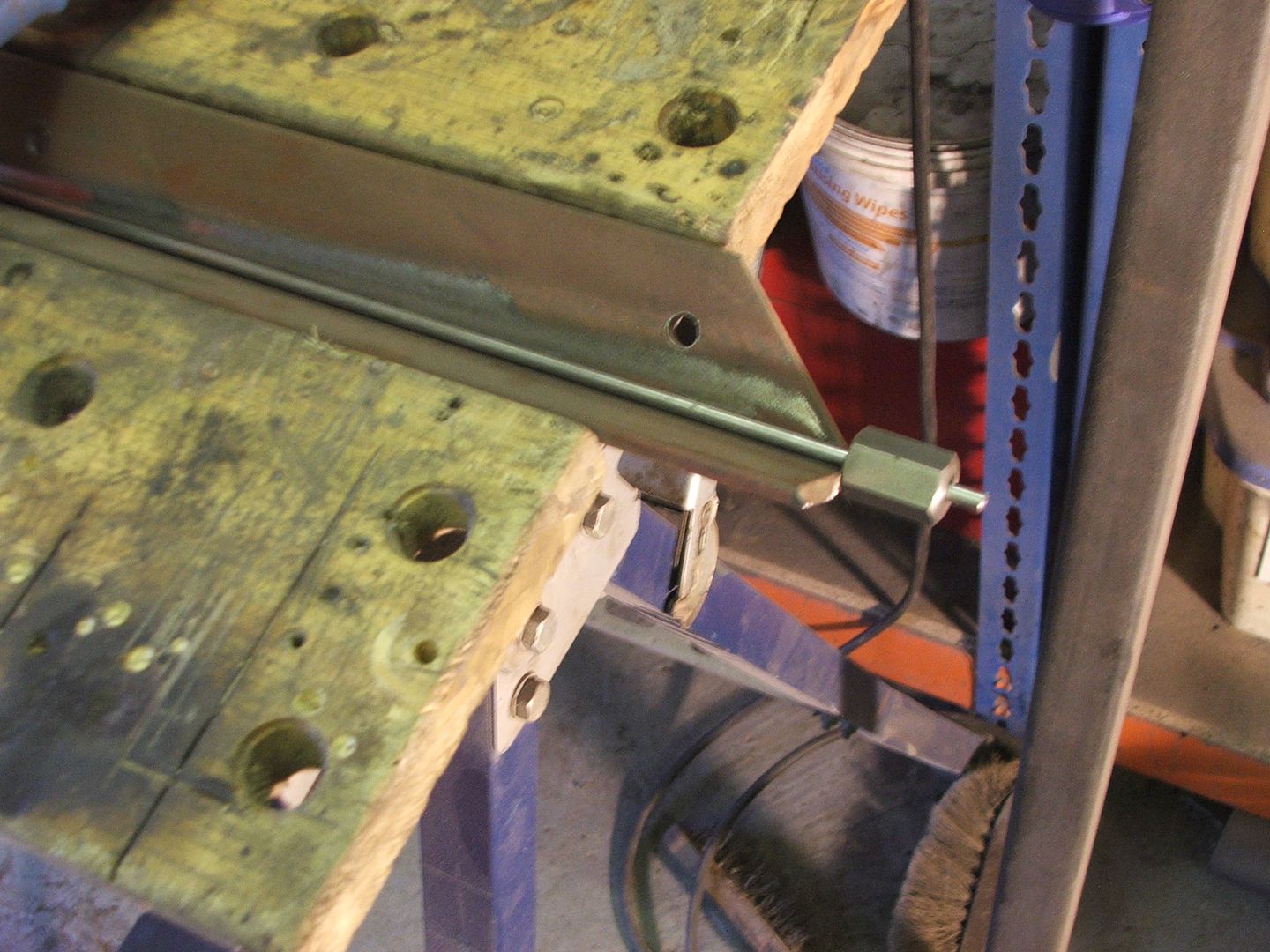
Weldy weldy and two got done
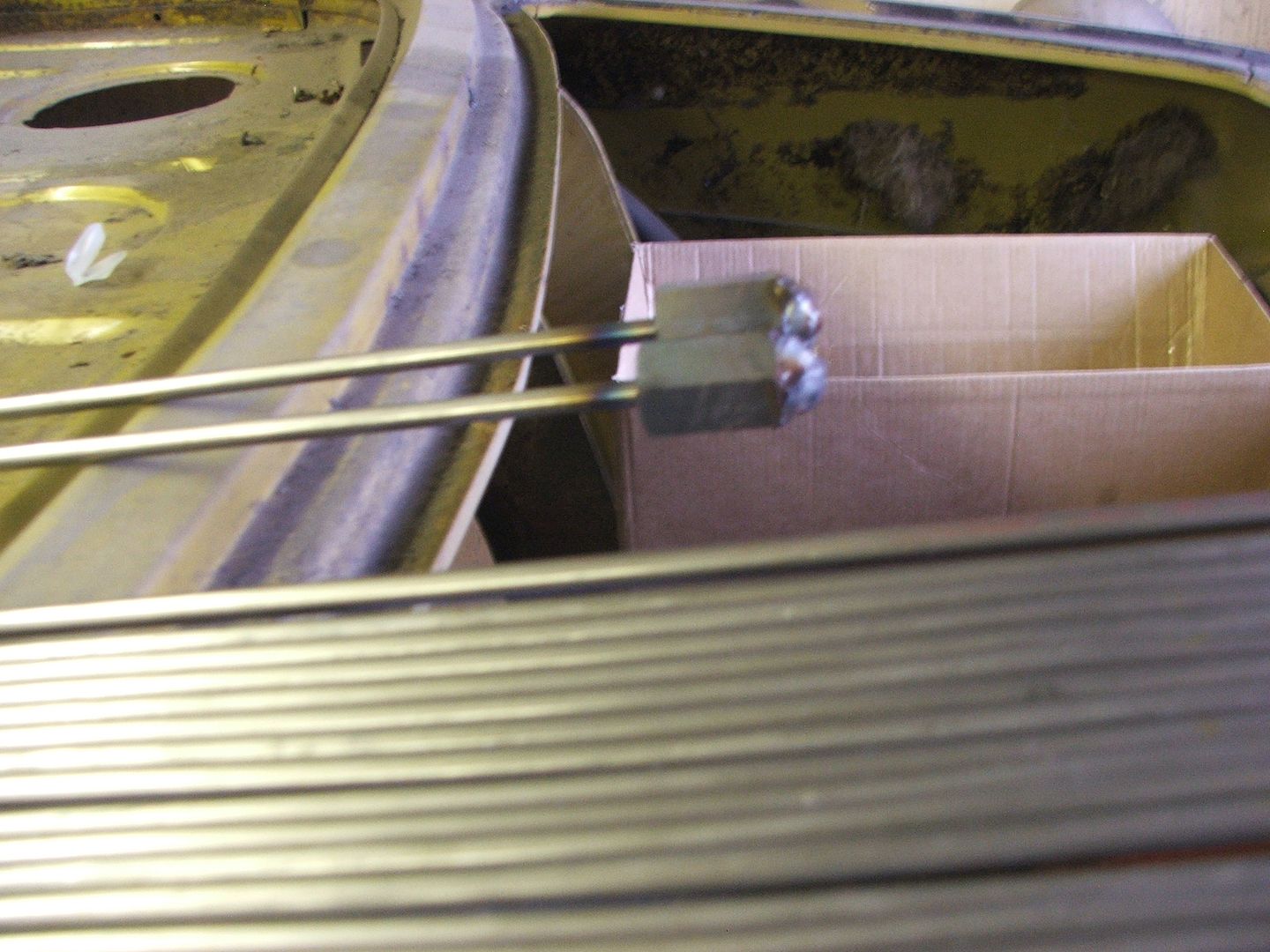
Lots more weldy weldy and I had 40 welded up
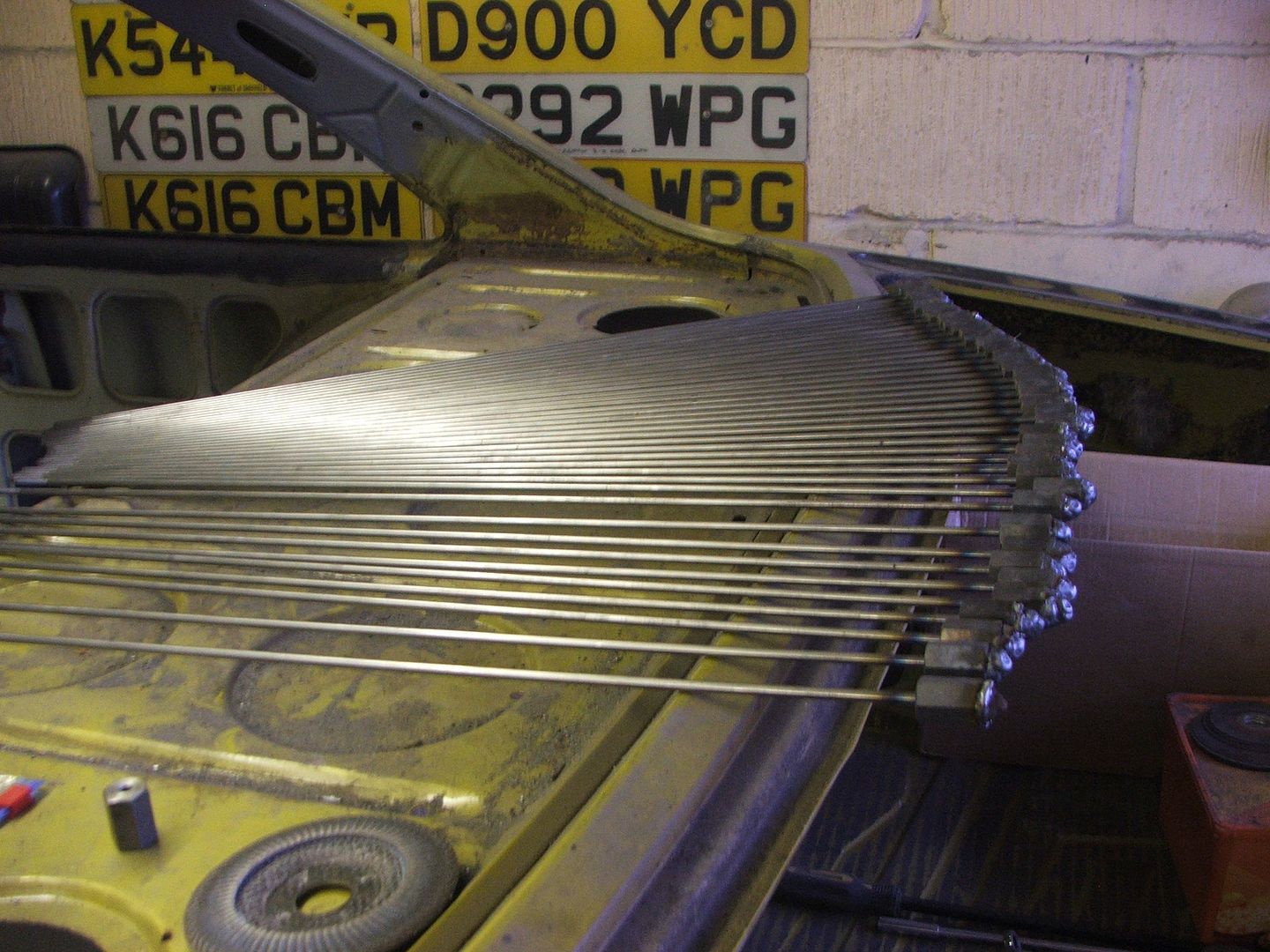
Just need to clean up the welds and stick a bit of paint on the end
And while I'm doing this the engineer is machining up the slide hammers hopefully I'll finish cleaning up my welding before he's done - unlikely!!!
So I borrowed an ancient Opel/Vauxhall tool to extract the door pins so I could remove the doors on my current track car project - 43 years they'd been in and they'd defeated the usual cranked arm machine mart tool (never found them to survive more than a couple of doors before they break) so I borrowed a better tool from a mate.
It's effectively a slide hammer on a thin steel rod with a removable end cap that is slightly under the size of a door pin hole and a few cracks on the slide hammer extracts the door pin easily
Three components
1 - steel shaft approx 60 cm long 10 mm Diameter tapering to 4-5 mm Diameter threaded at the end
2 - Slide hammer weight (approx 1 kg)
3 - Pin extraction tip (10 cm long diameter just under 8 mm threaded internally)
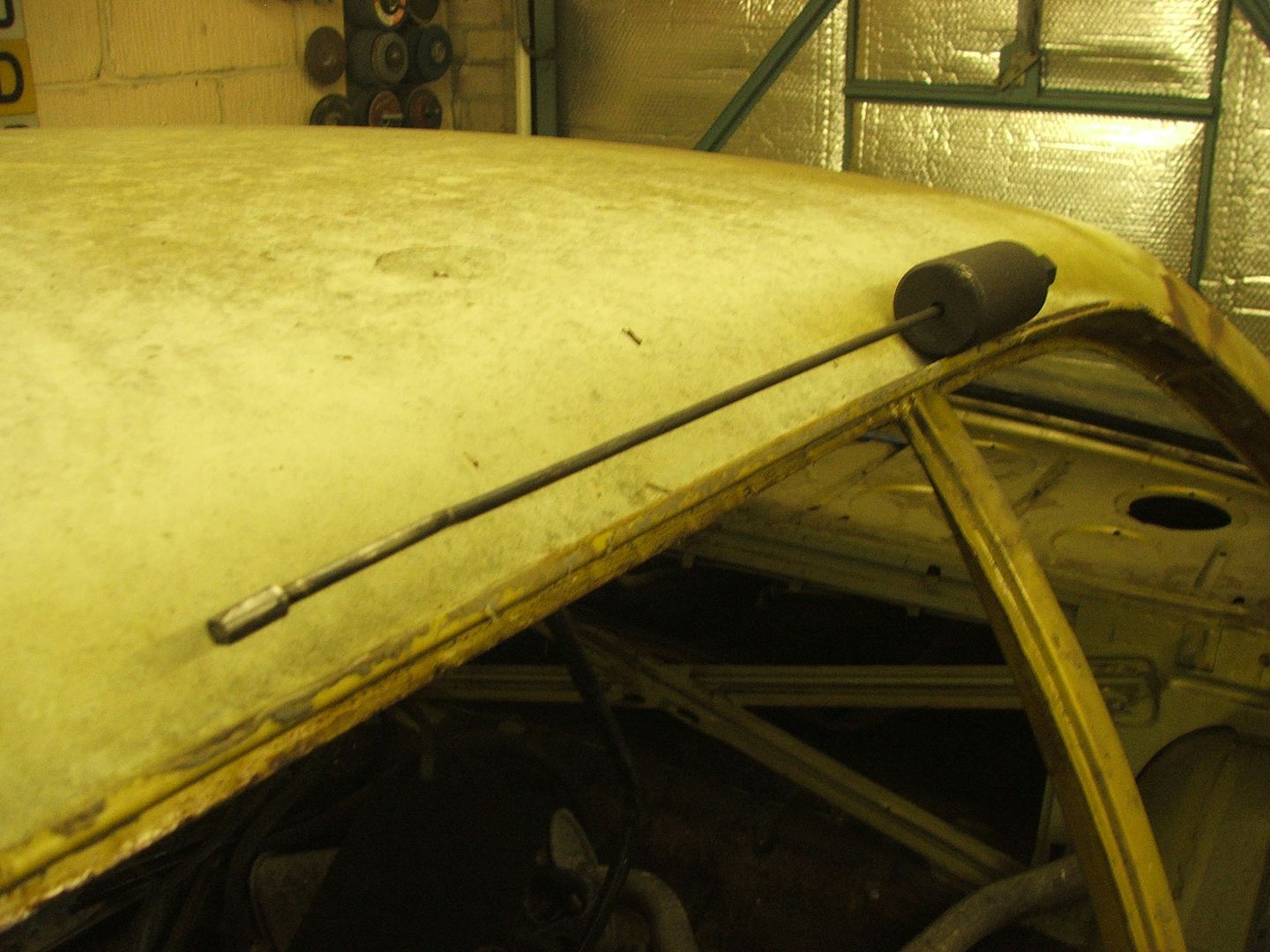
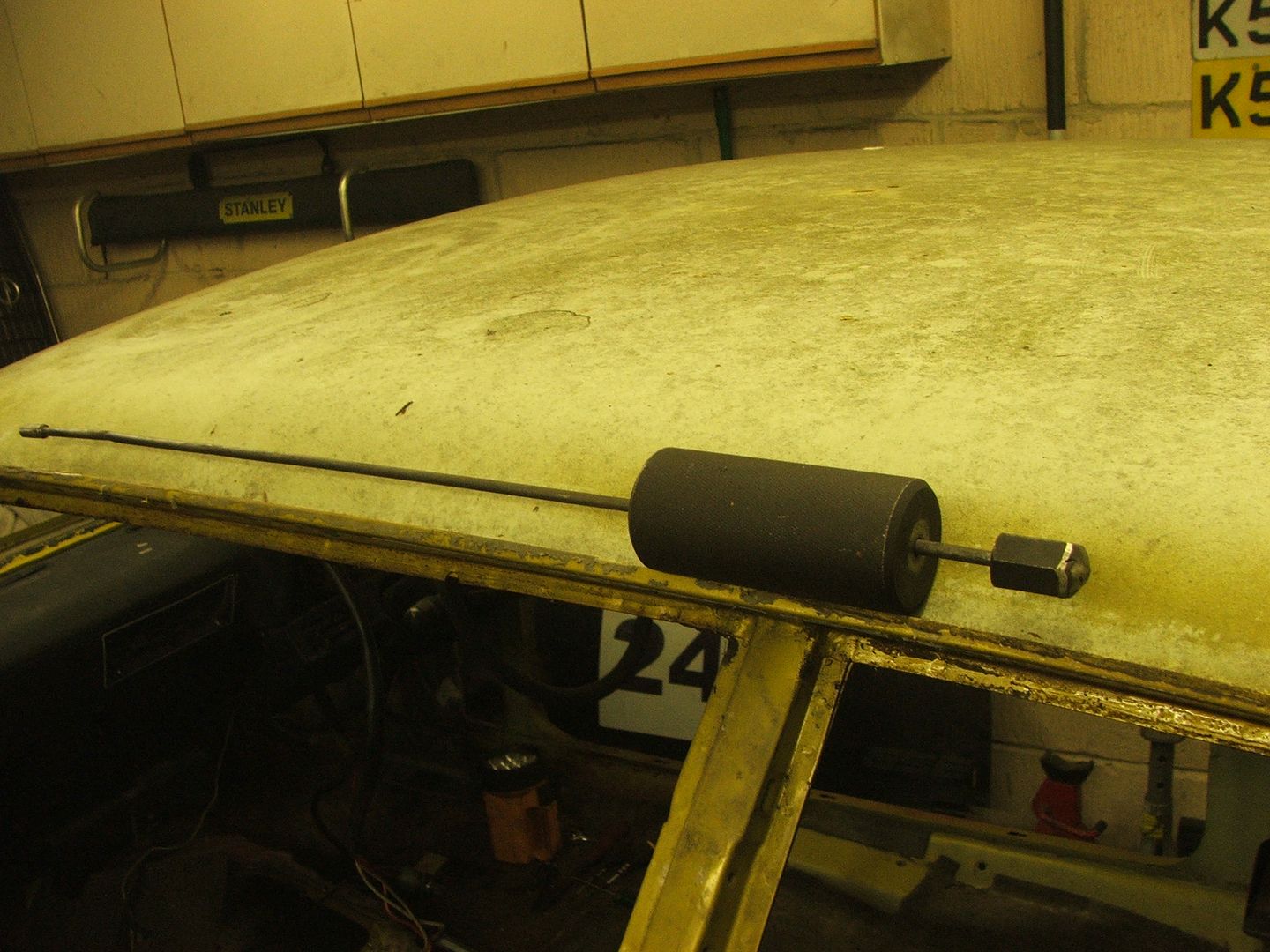
Now when I borrowed it I was warned that the thread was getting iffy and the ferule was a ground down nut as the original had been lost - it got one pin out and cried enough (15 years of door pin removal - it seemed fair service)
Now we all share borrow tools and the accepted rule is if you break or damage something you repair or replace. So I had to get it re-threaded at a "local" engineering shop and a decent sized ferule made up to reduce the load on the thread.
I asked if they would make me one - the engineer reckoned for a one off it would be quite expensive but for a few of them it would probably bring the labour element of the cost right down (material cost will always be the same)
So fixed and some drawings made and the rest of the pins came out just fine
Anyway I asked on the club forums if people were interested and I got a fairly good response.
I got a partial delivery today
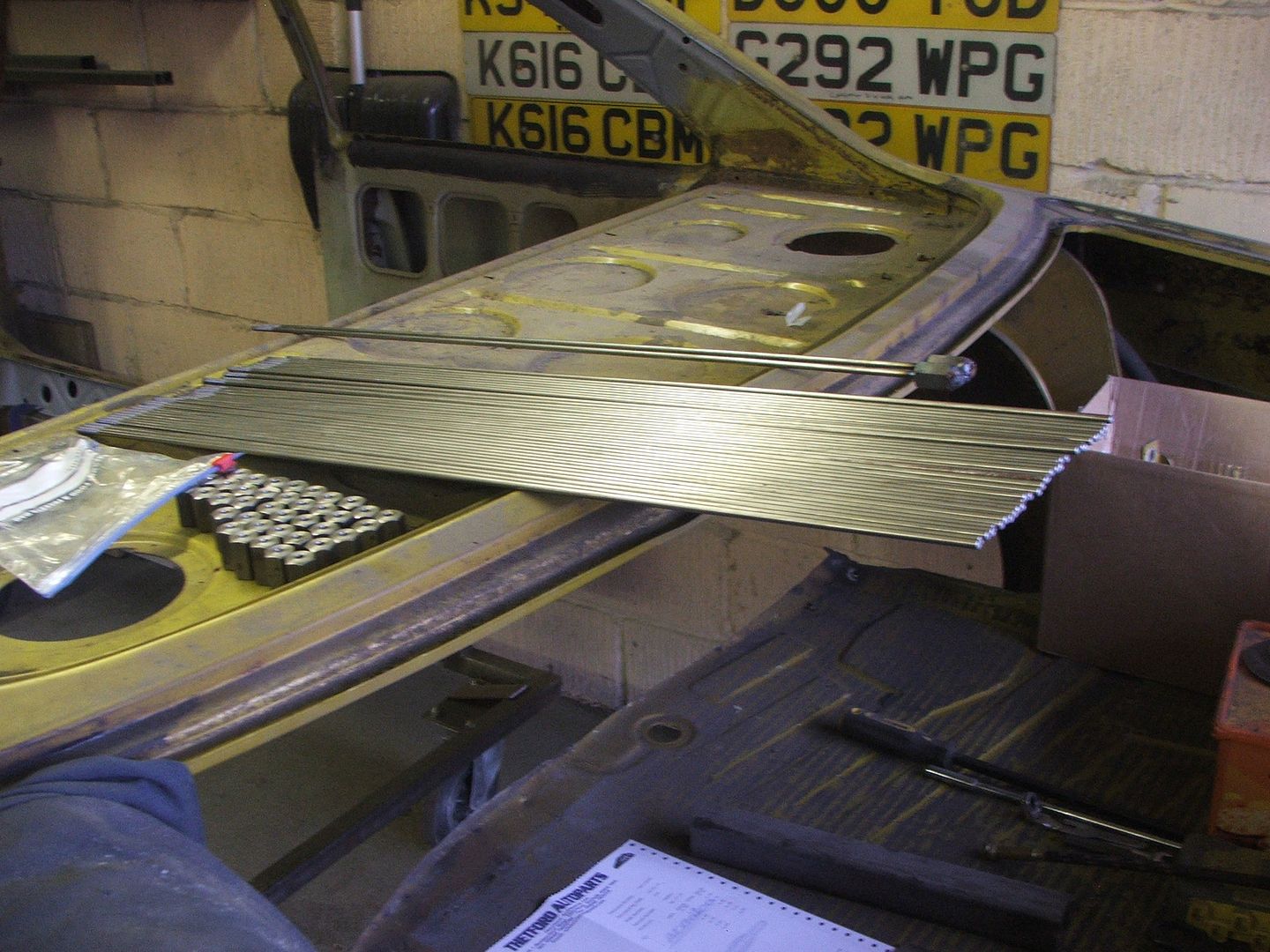
And
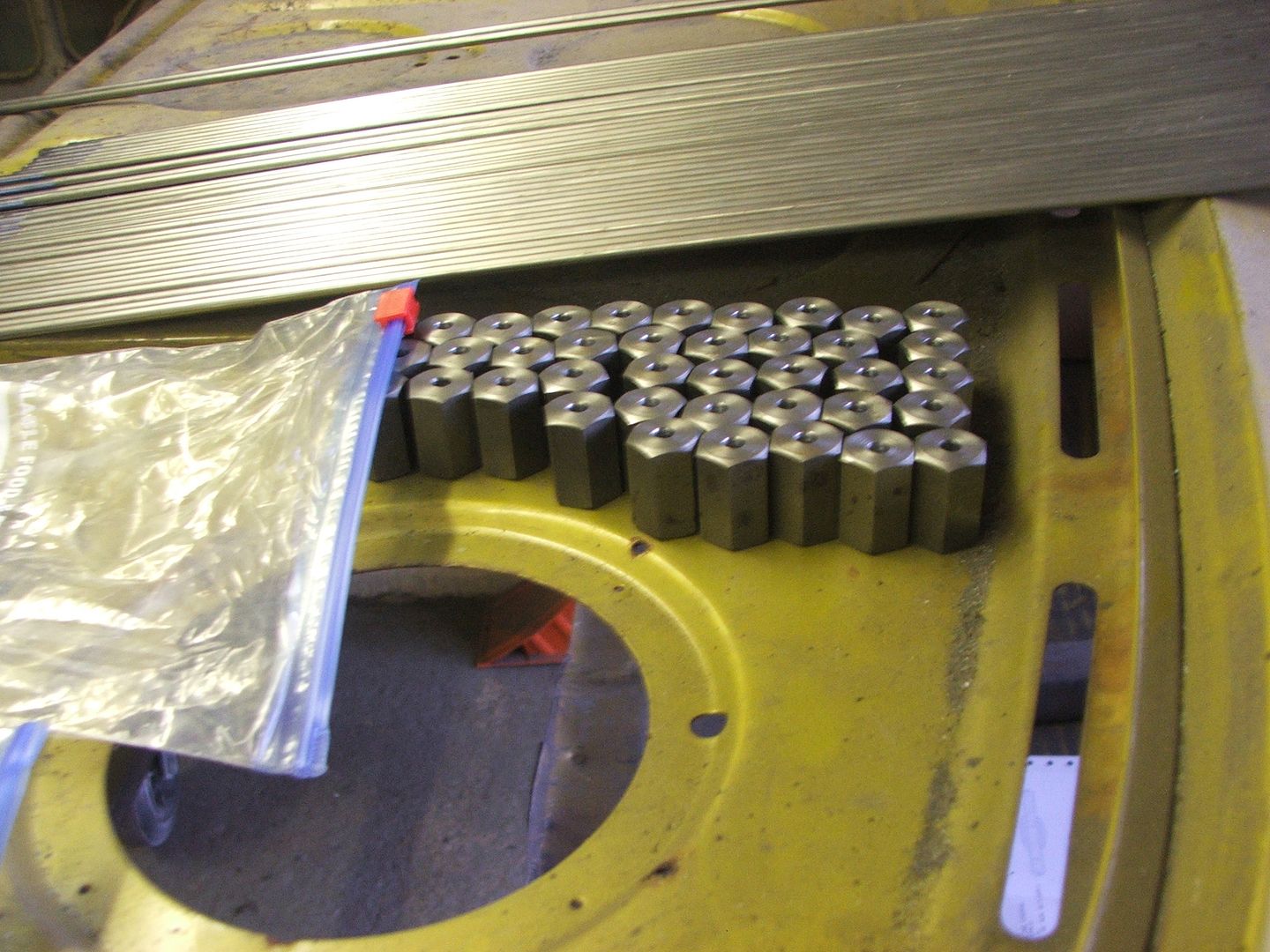
I got the ferules in EN24T with a nice flat either side at the end to make holding/doing up easy when it's thro the door pin
So as I think I mentioned earlier - the engineer can machine but not weld so that bit is down to me so I set up a little jig
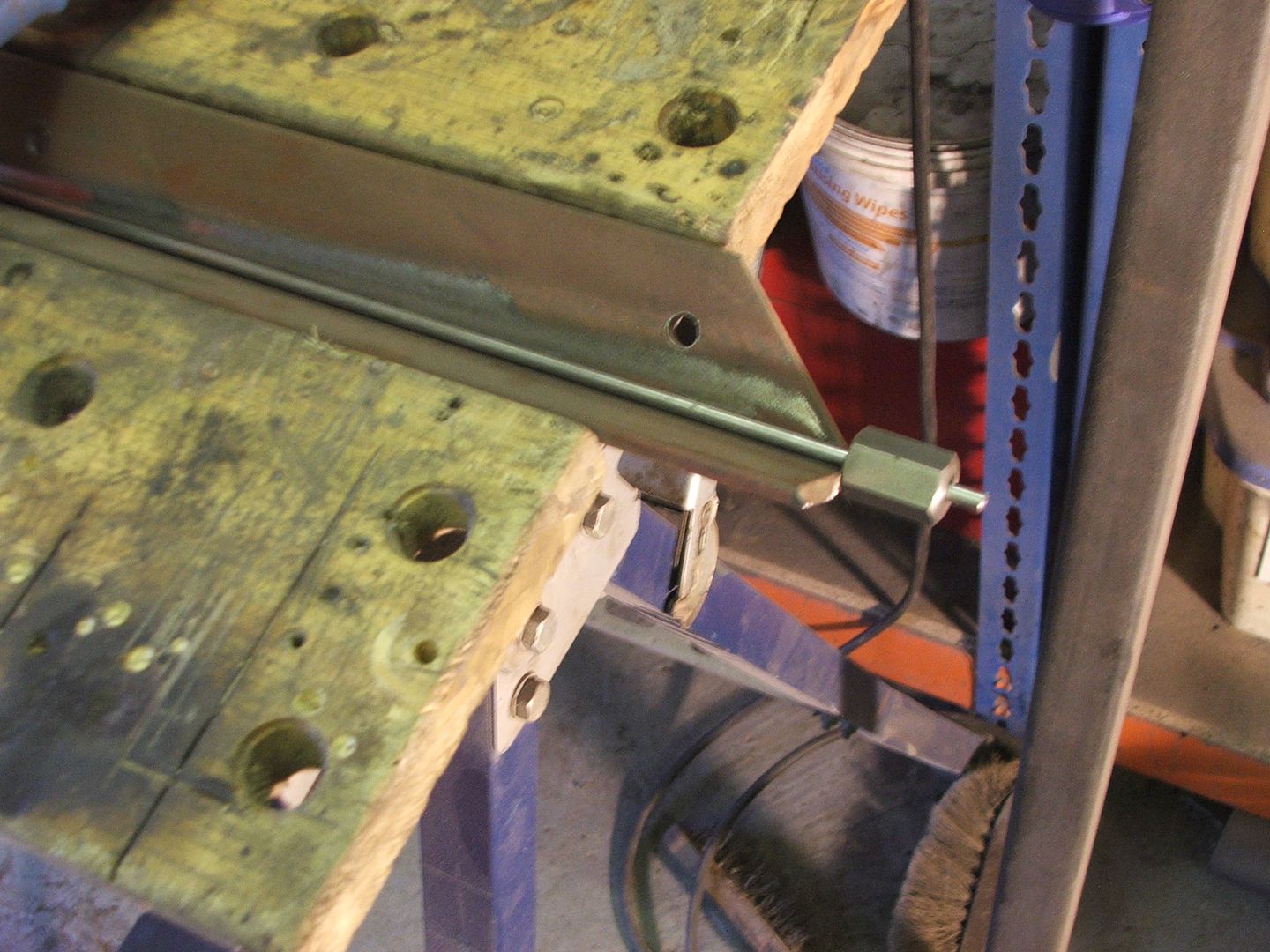
Weldy weldy and two got done
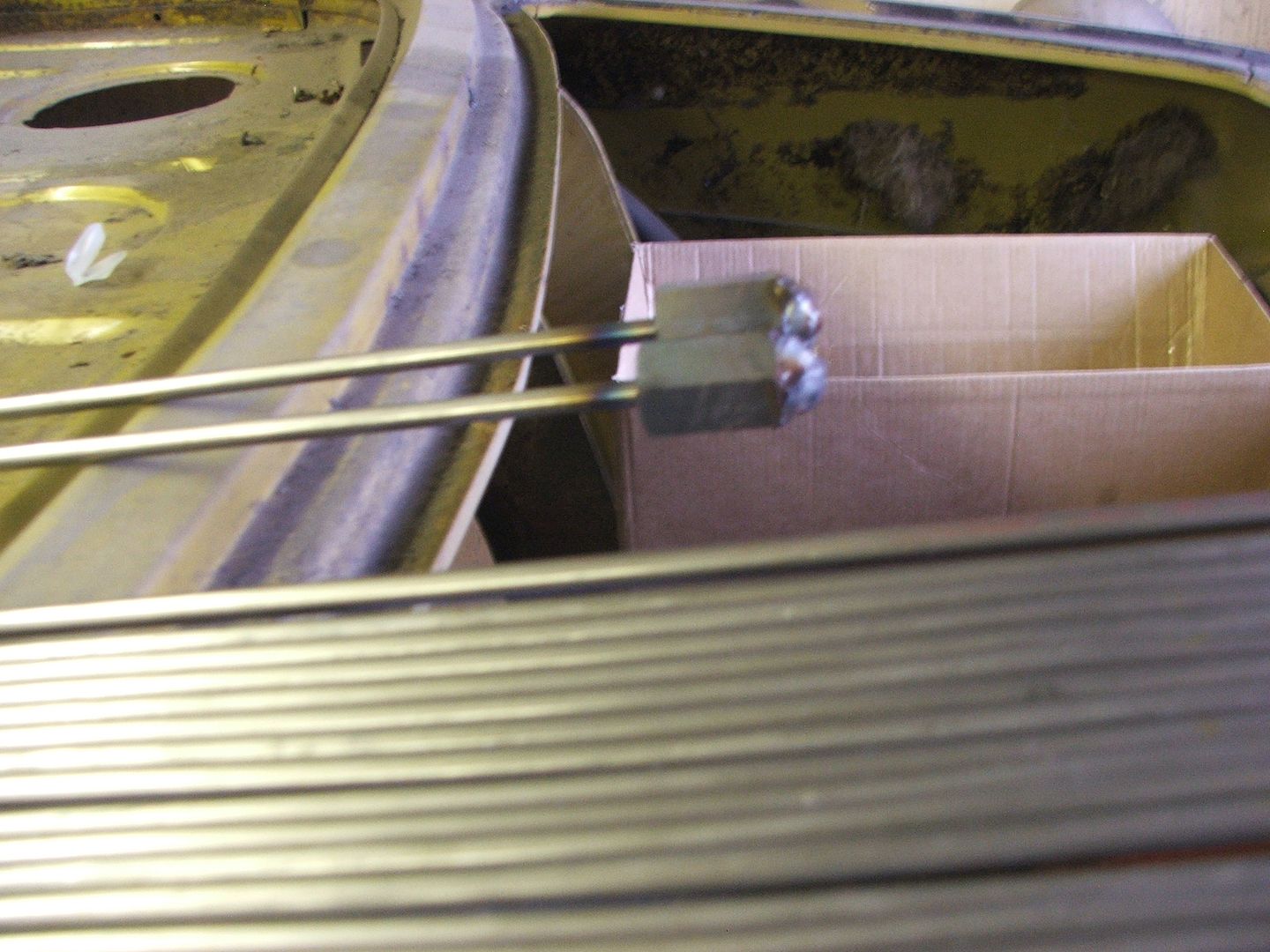
Lots more weldy weldy and I had 40 welded up
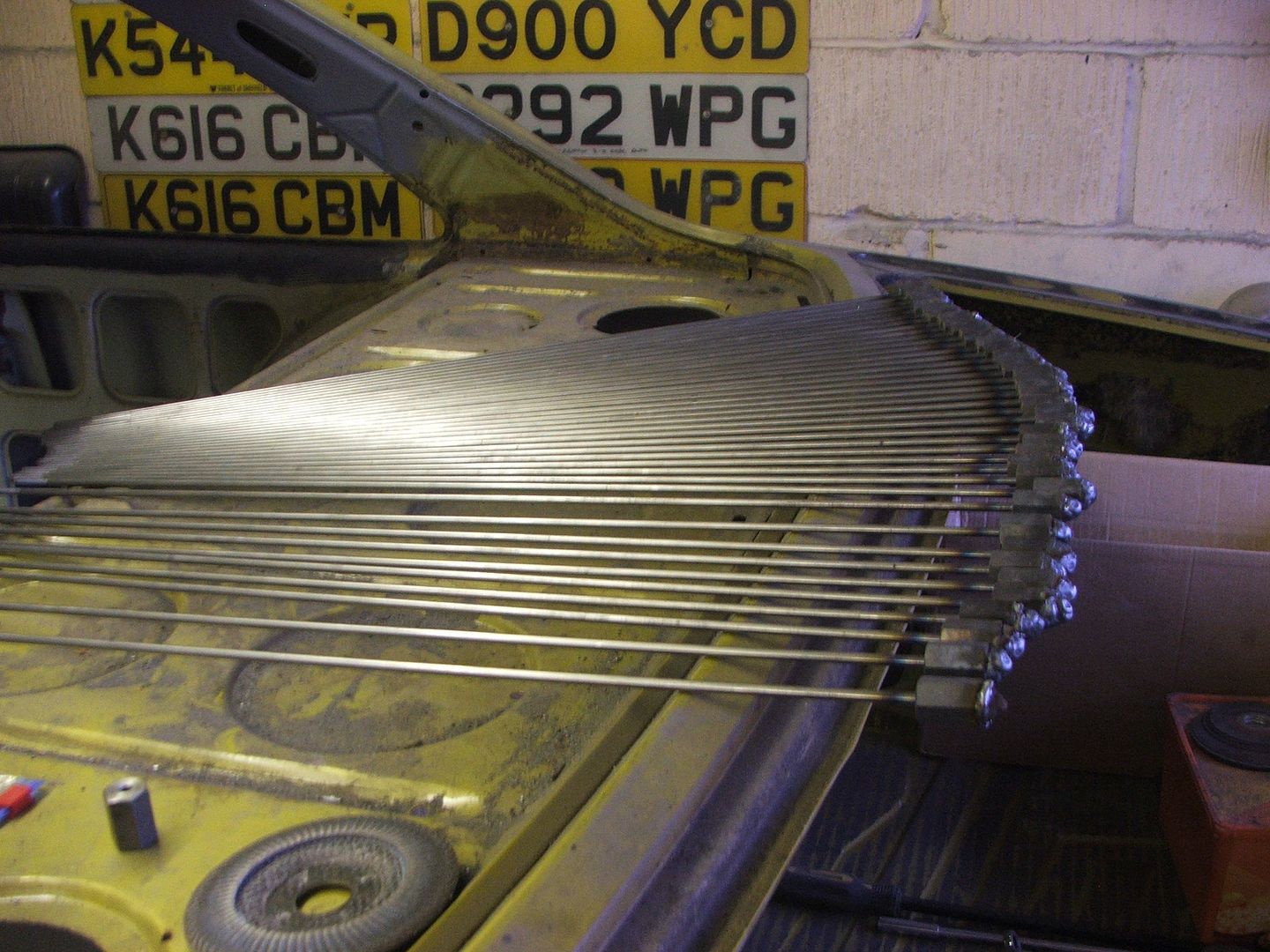
Just need to clean up the welds and stick a bit of paint on the end
And while I'm doing this the engineer is machining up the slide hammers hopefully I'll finish cleaning up my welding before he's done - unlikely!!!