Richard.
Member
- Messages
- 18,344
- Location
- Cambridgeshire
I bought a large lump of cast iron surface plate cheap off Pete late last year and it’s been great for setting up my small to medium fabrication jobs on but I’ve decided to try and make it that little bit more useful and add some fixtures to it.
So to start off it needed 15 holes spaced 150mm apart which gave me 150-170mm of maximum reach from any hole to be able to clamp in any position on the table. Then all of them were tapped out m12.

First job I think is some simple clamps. 10 in total is enough of a variety of possible clamping heights.
The m12 threaded bar is perfect for making things fully adjustable. You can’t go mad on tightening them or they’re gonna bend but even finger tight on the nuts I can’t physically move the item being clamped to the bench so more than good enough for firmly holding jobs flat to the top. Here is a typical clamp kit
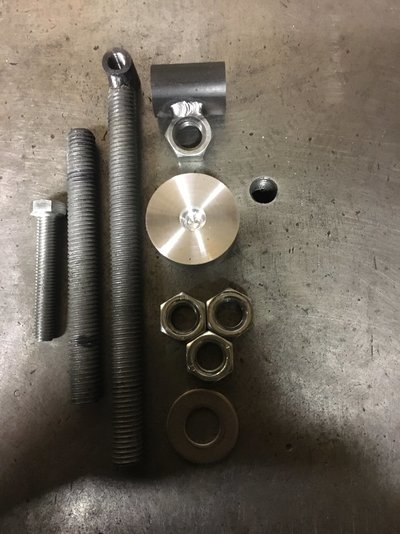
And assembled in action holding a flat firmly to a box.
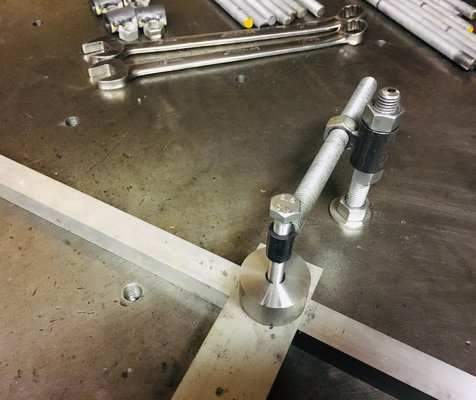
So to start off it needed 15 holes spaced 150mm apart which gave me 150-170mm of maximum reach from any hole to be able to clamp in any position on the table. Then all of them were tapped out m12.

First job I think is some simple clamps. 10 in total is enough of a variety of possible clamping heights.
The m12 threaded bar is perfect for making things fully adjustable. You can’t go mad on tightening them or they’re gonna bend but even finger tight on the nuts I can’t physically move the item being clamped to the bench so more than good enough for firmly holding jobs flat to the top. Here is a typical clamp kit
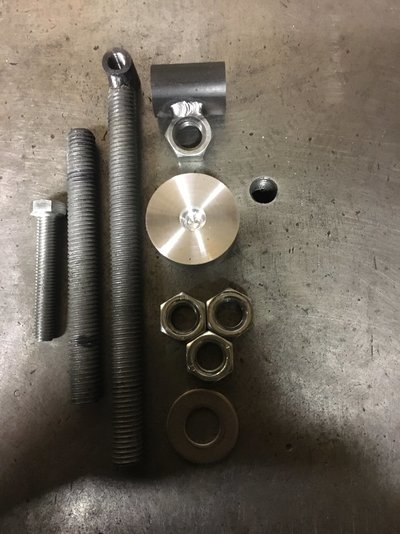
And assembled in action holding a flat firmly to a box.
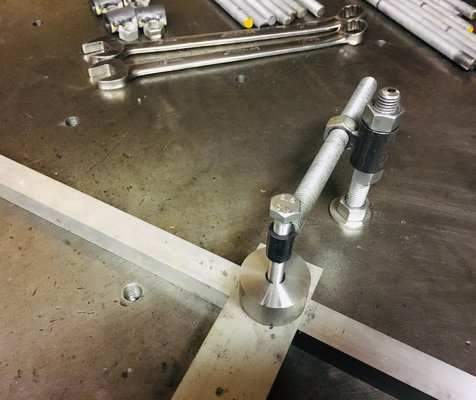