Hello All 
I joined the forum last July after my project car, a 68 Mustang, failed it's MOT and I've been reading since. I bought myself a Clarke 160TE and i think it's paid for itself already with the welding I've done. I've taught myself with the aid of the tutorials on this site, the search function and some help from friends! I've come to the conclusion its all about practise and trial and error!
Anyway, on to the reason for my first post. I am about to make myself an turbo exhaust manifold for my project. I have some mild steel butt weld fittings and a piece of flat mild steel (for the flange). The pipes are about 3.5mm wall thickness and the flat is 12mm thick.
I've not done anything like this before so I'm not sure what will happen!
Do you think I will suffer any problems with the flange warping during welding if it is unsupported?
I have a piece of 10mm stainless steel I could bolt to it to hopefully reduce warpage, but would this be sufficient?
The other option is my new aluminium cylinder head that I could bolt it too during welding, but i'd rather not risk damaging this with stray weld. (or am i being over cautious about the head?)
Any help/advice is apprieciated!
Cheers
Nathan
PS Here is my project car (photo is a little old now, there have been a few changes)

I joined the forum last July after my project car, a 68 Mustang, failed it's MOT and I've been reading since. I bought myself a Clarke 160TE and i think it's paid for itself already with the welding I've done. I've taught myself with the aid of the tutorials on this site, the search function and some help from friends! I've come to the conclusion its all about practise and trial and error!

Anyway, on to the reason for my first post. I am about to make myself an turbo exhaust manifold for my project. I have some mild steel butt weld fittings and a piece of flat mild steel (for the flange). The pipes are about 3.5mm wall thickness and the flat is 12mm thick.
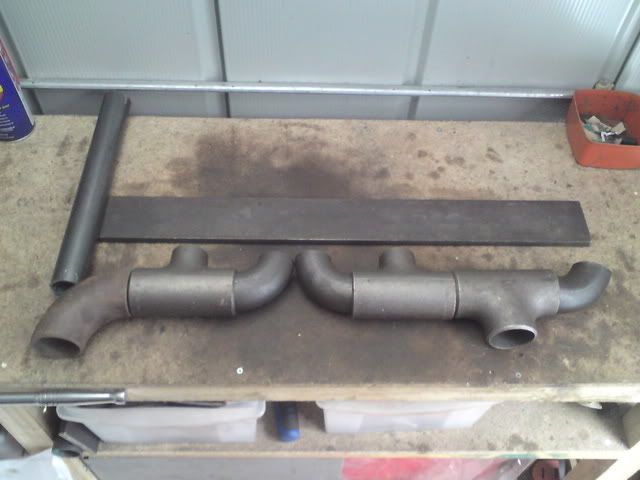
I've not done anything like this before so I'm not sure what will happen!
Do you think I will suffer any problems with the flange warping during welding if it is unsupported?
I have a piece of 10mm stainless steel I could bolt to it to hopefully reduce warpage, but would this be sufficient?
The other option is my new aluminium cylinder head that I could bolt it too during welding, but i'd rather not risk damaging this with stray weld. (or am i being over cautious about the head?)
Any help/advice is apprieciated!
Cheers
Nathan
PS Here is my project car (photo is a little old now, there have been a few changes)
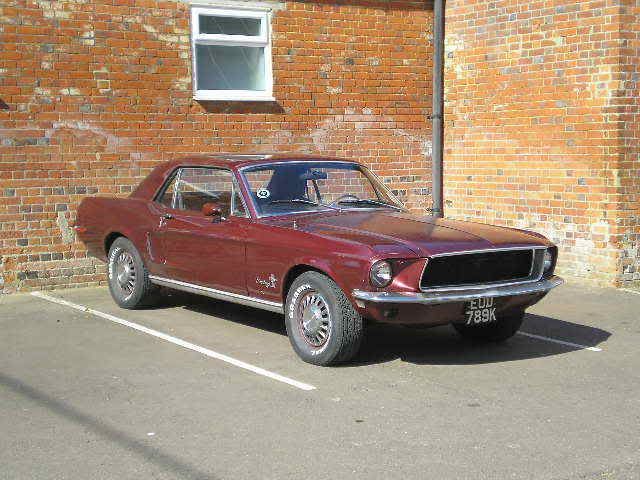