I always struggle with fillet welds, I can do them pretty well on the DC inverter but I think this is because the better machine is covering for my poor technique.
Whenever I do them on AC they always go off and miss the joint, or have a load of slag in them.
Oxford oil cooled at 80amps, 2.5mm Bohler AWS 6013 rod.
Is it rod angle that's the issue? I ask this because I altered the angle to a bit more towards 90 along the travel line and it helped (still 45 degree into the joint favouring the upper piece) and things improved. The problem with putting the angle more vertical is that I sometimes get the pool (molten slag maybe) on the wrong side of the rod which suggests it's too vertical along the travel line.
Or is it amps, running too cold and needs more current? I feel like I'm having to rush the joint though which suggests it's too hot.
The weld sounds good or at least it does to me, crackling frying pan.
Totally missed the joint
Adjusted angle which gave a better result
but still not perfect at that angle
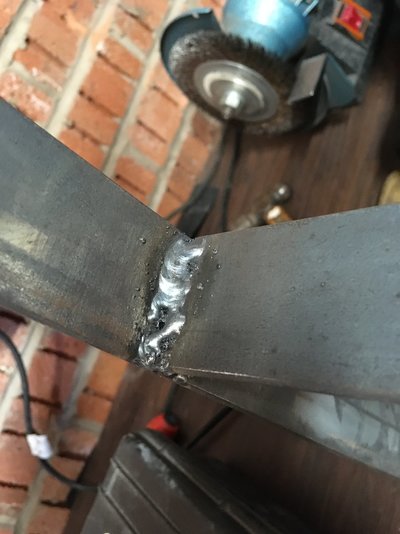
Whenever I do them on AC they always go off and miss the joint, or have a load of slag in them.
Oxford oil cooled at 80amps, 2.5mm Bohler AWS 6013 rod.
Is it rod angle that's the issue? I ask this because I altered the angle to a bit more towards 90 along the travel line and it helped (still 45 degree into the joint favouring the upper piece) and things improved. The problem with putting the angle more vertical is that I sometimes get the pool (molten slag maybe) on the wrong side of the rod which suggests it's too vertical along the travel line.
Or is it amps, running too cold and needs more current? I feel like I'm having to rush the joint though which suggests it's too hot.
The weld sounds good or at least it does to me, crackling frying pan.
Totally missed the joint
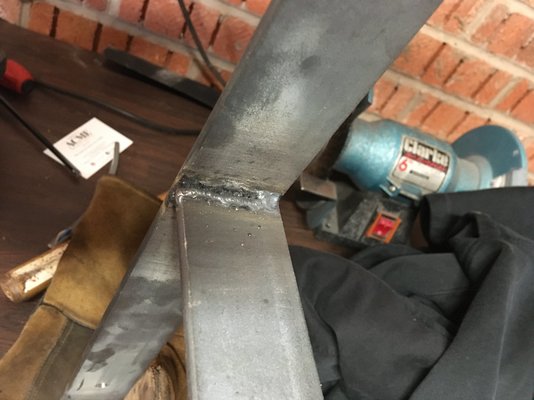
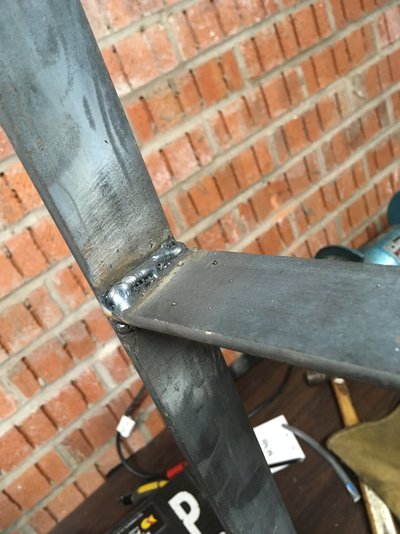
Adjusted angle which gave a better result
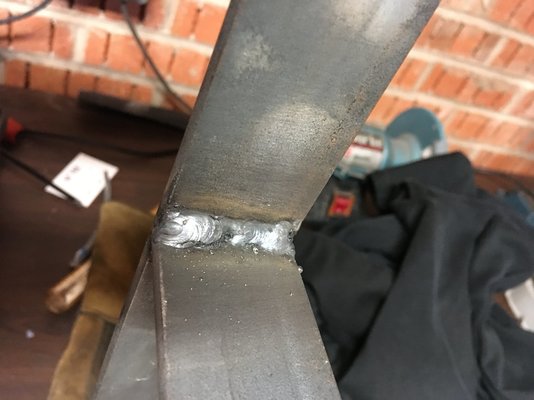
but still not perfect at that angle
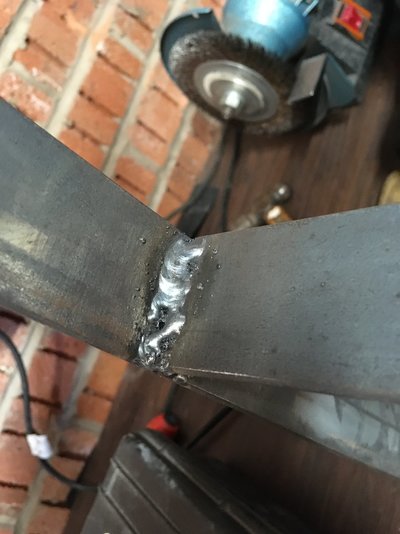