I've been making some punch and dies - and have had some success with multile holes on smaller tins.
I've now come to do the same thing on larger tin lids (With larger punch rods) and have run into a few problems.
I suspect the problem is two fold - but would welcome any guidance.
Problem # 1 - I'm not cutting the silver steel which (Used as the punch pins) cleanly enough. These are 4mm and 5mm.
To get the pins from the 'main rod', I've tried:
Grinding them with a cutting disc (Leaves a burr)
Bolt cutters (Leaves a rough end here the silver steel 'snaps'
Hacksaw (No - just no...)
Lathe (Too much deflection when trying to part off)
All of these all lead to some sort of malformation or burr, which I've been taking off with a grinder, or with sandpaper - and I think is leading to a tapered (i.e. pointed) pin going into the die - causing the tin lid to stretch more than shear - so leaving sharp edges.
Problem #2 - perhaps the die holes are too large, so allowing the 'stretch not shear'. I've been making the holes with short drill bit (Trying to minimise hole drift). Would I be better making a smaller drill hole, and finishing with a reamer? I've never used a reamer - don't even know if they come in different types - so what size drill/size and type reamer do I need for 4 and 5 mm holes?
I'm doing the holes in punch and die with my pillar drill - as I don't have a vertical mill which I guess may be slightly stiffer?
I know you all love a picture - so here are some demonstrating the problem tops - in tin and aluminium. The upper side showing various nicks and deformities from pushing/pulling through the material. The underside showing the 'stretch' rather than shear of the pins - and I must say those thin slivers of stretched tin are viciously sharp!
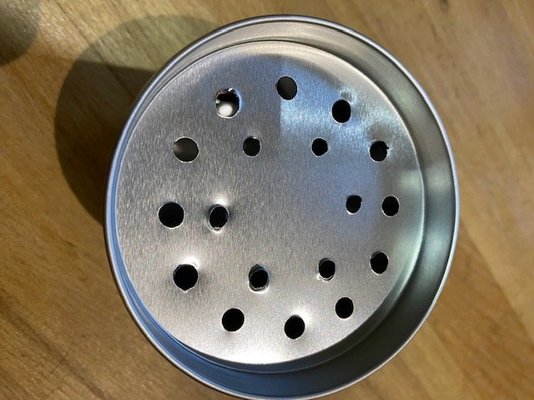
I've now come to do the same thing on larger tin lids (With larger punch rods) and have run into a few problems.
I suspect the problem is two fold - but would welcome any guidance.
Problem # 1 - I'm not cutting the silver steel which (Used as the punch pins) cleanly enough. These are 4mm and 5mm.
To get the pins from the 'main rod', I've tried:
Grinding them with a cutting disc (Leaves a burr)
Bolt cutters (Leaves a rough end here the silver steel 'snaps'
Hacksaw (No - just no...)
Lathe (Too much deflection when trying to part off)
All of these all lead to some sort of malformation or burr, which I've been taking off with a grinder, or with sandpaper - and I think is leading to a tapered (i.e. pointed) pin going into the die - causing the tin lid to stretch more than shear - so leaving sharp edges.
Problem #2 - perhaps the die holes are too large, so allowing the 'stretch not shear'. I've been making the holes with short drill bit (Trying to minimise hole drift). Would I be better making a smaller drill hole, and finishing with a reamer? I've never used a reamer - don't even know if they come in different types - so what size drill/size and type reamer do I need for 4 and 5 mm holes?
I'm doing the holes in punch and die with my pillar drill - as I don't have a vertical mill which I guess may be slightly stiffer?
I know you all love a picture - so here are some demonstrating the problem tops - in tin and aluminium. The upper side showing various nicks and deformities from pushing/pulling through the material. The underside showing the 'stretch' rather than shear of the pins - and I must say those thin slivers of stretched tin are viciously sharp!
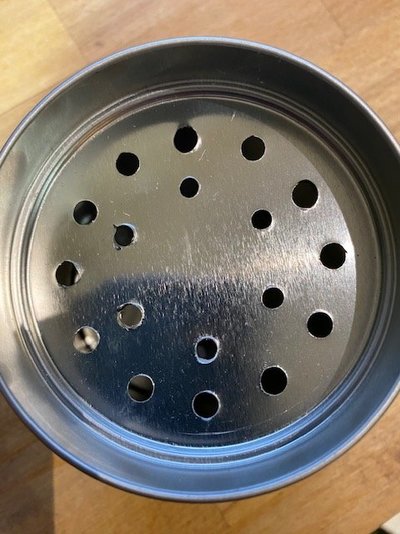
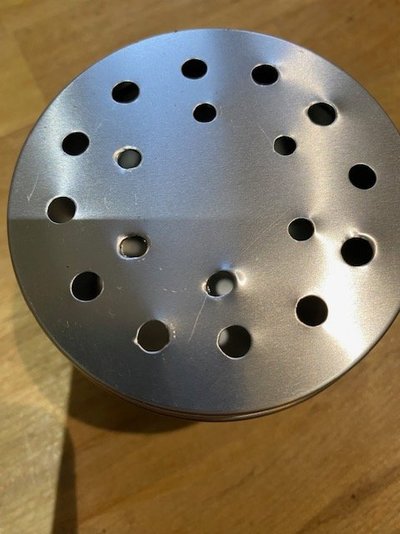
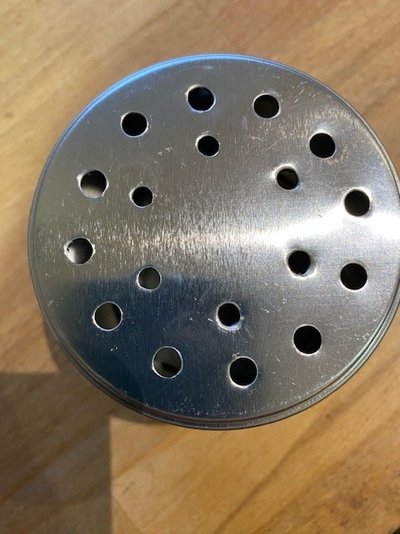
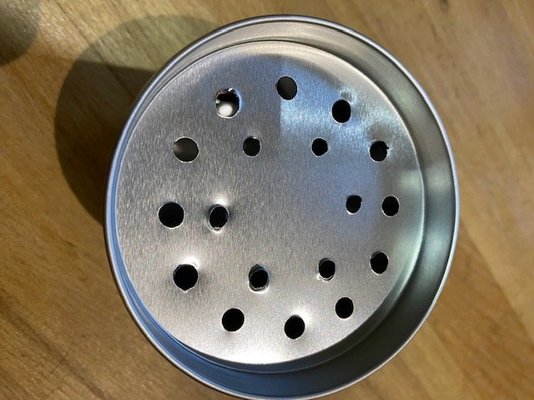