Misterg
Member
- Messages
- 1,062
- Location
- North Wales
Years ago, when the internet was still in primary school, one of the wonders that I found (in between pictures of naked ladies) was that a guy called Kurt Schreckling had written a book on how to build a working model jet engine inside an empty Camping Gaz cannister. I really wanted one, but at the time I was living in a first floor flat with absolutely no workshop facilities, then life got in the way.
Fast forward about 25 years and I now have a TIG welder and a lathe... and still a hankering to try and build a jet engine. So I bought a book:
www.sarikhobbies.com
This is still a dated design with modest performance, but importantly (to me) it's is one of the few which is claimed to work with a home made turbine wheel
So, for the last few months, I've been working on turning this:

Into something that looks more like this (but both halves!)

I thought some pictures might be of interest - it's not finished yet, and I've no idea if it'll work but if I don't start posting pictures now, I probably never will, so here goes:
***WARNING! CONTAINS IMAGES OF AMATEURISH WELDING WHICH SOME MAY FIND DISTRESSING ***
I made a start on the combustion chamber (the grey bit with the holes in). It's supposed to look like this (mostly 0.5mm 304 stainless):
It acts a bit like a blowlamp nozzle - air gets fed from the outside and fuel gets fed to the inside (through the cranked vapouriser tubes) and the fire goes out the back.
The front cover was spun over a plywood former on my mini lathe:

I formed most of the cover with a brass bar in the tool post of the lathe

then used a bearing to tightly crimp the edge. I needed to remove the piece and anneal it to get the edge to turn down properly.

After this, I clamped the part over the outer diameter so that the centre clamp could be removed and used the brass bar again to form the central hole.

No photos of the inner hole being formed, but it was much easier than the OD and very pleasing to do!
The rear cover was made using the same former and the holes drilled with a toolpost spindle while the part was still on the lathe.
The inner and outer walls of the combustion chamber have a pattern of holes drilled in them. I thought it would be difficult to weld the inner wall if I rolled it after drilling, even with a staggered seam, so I decided to roll and weld it first and drill after. I used the aluminium stock I had bought for the shaft tunnel as a mandrel to form the combustion chamber inner, shaving the diameter down gradually until I cold get the ends of the sheet to meet tightly.

Then tig welded the seam with it still on the mandrel;

(A bit messy as I burned through in a couple of places and had to use filler rod to plug the hole, but it looked OK after grinding the tops off the lumps.
At this point, I could still move the inner.
I parted the sleeve to length and decided I may as well drill the holes in the inner sleeve whilst it was still on the mandrel too.


It turned out that it was a bit of a battle to get it off the mandrel! I thought I would be OK if I stuck the whole thing in the freezer (but I was wrong!).

The design calls for some of the holes to be drilled undersize then swaged to the finished diameter, creating a sort of jet to direct the air into the combustion chamber. I swaged the holes in the inner wall using a punch mounted in a length of bar that fitted inside the tube and bridged the vice jaws. The die is made from a section of thick-wall pipe so that the surface matches the curvature of the combustor inner. It seemed like a good idea at the time, but not sure that it was worth the trouble compared to just turning the die with a flat face.


I was happy with this so far!

Continued...
Fast forward about 25 years and I now have a TIG welder and a lathe... and still a hankering to try and build a jet engine. So I bought a book:

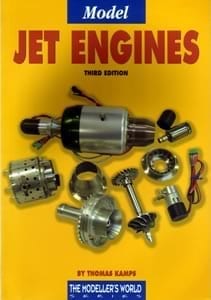
Model Jet Engines (3rd Edtn) Plane Modelling Book - by Thomas Kamps - Sarik Hobbies - for the Model Builder
Grab a little bit of history and take a trip down memory lane with Model Jet legend, Thomas Kamps, as he takes you on a journey through the history of model jet engine development.

This is still a dated design with modest performance, but importantly (to me) it's is one of the few which is claimed to work with a home made turbine wheel

So, for the last few months, I've been working on turning this:

Into something that looks more like this (but both halves!)

I thought some pictures might be of interest - it's not finished yet, and I've no idea if it'll work but if I don't start posting pictures now, I probably never will, so here goes:
***WARNING! CONTAINS IMAGES OF AMATEURISH WELDING WHICH SOME MAY FIND DISTRESSING ***
I made a start on the combustion chamber (the grey bit with the holes in). It's supposed to look like this (mostly 0.5mm 304 stainless):


It acts a bit like a blowlamp nozzle - air gets fed from the outside and fuel gets fed to the inside (through the cranked vapouriser tubes) and the fire goes out the back.
The front cover was spun over a plywood former on my mini lathe:

I formed most of the cover with a brass bar in the tool post of the lathe

then used a bearing to tightly crimp the edge. I needed to remove the piece and anneal it to get the edge to turn down properly.

After this, I clamped the part over the outer diameter so that the centre clamp could be removed and used the brass bar again to form the central hole.

No photos of the inner hole being formed, but it was much easier than the OD and very pleasing to do!
The rear cover was made using the same former and the holes drilled with a toolpost spindle while the part was still on the lathe.
The inner and outer walls of the combustion chamber have a pattern of holes drilled in them. I thought it would be difficult to weld the inner wall if I rolled it after drilling, even with a staggered seam, so I decided to roll and weld it first and drill after. I used the aluminium stock I had bought for the shaft tunnel as a mandrel to form the combustion chamber inner, shaving the diameter down gradually until I cold get the ends of the sheet to meet tightly.

Then tig welded the seam with it still on the mandrel;

(A bit messy as I burned through in a couple of places and had to use filler rod to plug the hole, but it looked OK after grinding the tops off the lumps.
At this point, I could still move the inner.
I parted the sleeve to length and decided I may as well drill the holes in the inner sleeve whilst it was still on the mandrel too.


It turned out that it was a bit of a battle to get it off the mandrel! I thought I would be OK if I stuck the whole thing in the freezer (but I was wrong!).

The design calls for some of the holes to be drilled undersize then swaged to the finished diameter, creating a sort of jet to direct the air into the combustion chamber. I swaged the holes in the inner wall using a punch mounted in a length of bar that fitted inside the tube and bridged the vice jaws. The die is made from a section of thick-wall pipe so that the surface matches the curvature of the combustor inner. It seemed like a good idea at the time, but not sure that it was worth the trouble compared to just turning the die with a flat face.


I was happy with this so far!

Continued...
Last edited: