The Hydrovane HV02 vane compressor produces 8 CFM @ 100 psi from a 2 HP 3000 rpm electric motor. The compressor unit is mounted directly onto the motor so the pair are in line, and coupled by a Lovejoy three prong coupling with a rubber 'spider' between the pair - shafts being 24 mm.
On the compressor the coupling is a cast iron one made by Fener (L090) but on the motor the same three prongs are moulded into and are integral with the filled nylon motor fan.
My motor was running but the compressor was not turning - the coupling had failed - rubber spider in loads of bits and the three moulded prongs on the fan were broken. New fan and spider needed. No used parts available and the fan and spider were just over £150 from Hydrovane - a ridiculous price - so what to do?
A few careful measurements and I concluded that if I got hold of a standard 090 Lovejoy coupler I'd have the rubber spider and a cast iron 'prongy thing' that with any luck I could machine down and having also machined the fan could fit as a composite unit. 090 coupler bought for under £20 !!!!
All traces of the original fan prongs machined off and fan hub shortened as far as I dared go - limited by the brass threaded clamping insert. Then I chucked up one of the Lovejoy halves - greatly reduced it's length so that it (when fixed to the fan) ended up the same length as the original fan hub. Then bored it to 24 mm and planed an 8 mm keyway.
Drilling and tapping three M5 holes for grub screws where there was enough meat to do so (by the prongs) on the Lovjoy I ended up with a loose fan that would slide back on the motor shaft, be located by the key, and be retained by it's original grubscrew, and a much reduced prongy thing that sits on the same shaft and keyway and is retained by the three M5 grub screws.
Setting the position of the two elements so that their engagement was correct was a bit of fun but once done I re-located the cut down prongy thing with Loctite as it's area of shaft contact was somewhat less than previously.
The Loctite having cured I've run it up a few times, and so far - fingers crossed - it's OK but time will be the true judge.
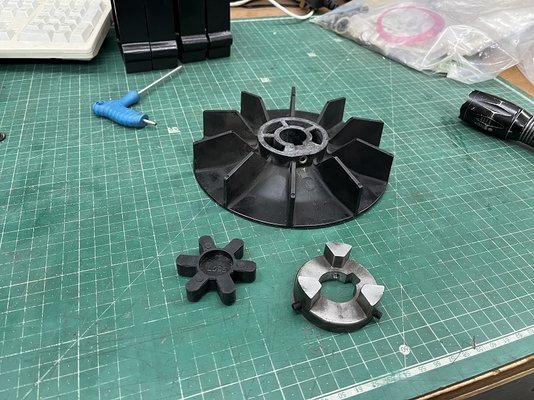
On the compressor the coupling is a cast iron one made by Fener (L090) but on the motor the same three prongs are moulded into and are integral with the filled nylon motor fan.
My motor was running but the compressor was not turning - the coupling had failed - rubber spider in loads of bits and the three moulded prongs on the fan were broken. New fan and spider needed. No used parts available and the fan and spider were just over £150 from Hydrovane - a ridiculous price - so what to do?
A few careful measurements and I concluded that if I got hold of a standard 090 Lovejoy coupler I'd have the rubber spider and a cast iron 'prongy thing' that with any luck I could machine down and having also machined the fan could fit as a composite unit. 090 coupler bought for under £20 !!!!
All traces of the original fan prongs machined off and fan hub shortened as far as I dared go - limited by the brass threaded clamping insert. Then I chucked up one of the Lovejoy halves - greatly reduced it's length so that it (when fixed to the fan) ended up the same length as the original fan hub. Then bored it to 24 mm and planed an 8 mm keyway.
Drilling and tapping three M5 holes for grub screws where there was enough meat to do so (by the prongs) on the Lovjoy I ended up with a loose fan that would slide back on the motor shaft, be located by the key, and be retained by it's original grubscrew, and a much reduced prongy thing that sits on the same shaft and keyway and is retained by the three M5 grub screws.
Setting the position of the two elements so that their engagement was correct was a bit of fun but once done I re-located the cut down prongy thing with Loctite as it's area of shaft contact was somewhat less than previously.
The Loctite having cured I've run it up a few times, and so far - fingers crossed - it's OK but time will be the true judge.
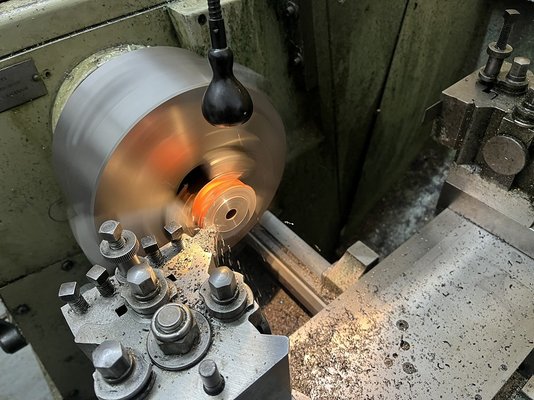
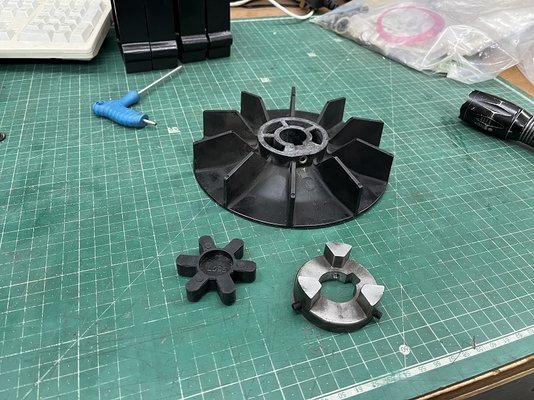