chunkolini
celebrity artiste
- Messages
- 9,514
- Location
- Swansea
For ages I have been meaning to modify the thingy on my bench shears to set the thickness being cut.
They are made by Keetona and needed a spanner and three hands to set up properly.
Every now and again I will 'waste' half a day of workshop time on these little jobs.
I found an old push bike quick release in a box of stuff, that I used years ago for something else, possibly securing a machine vice on a pillar drill.
Anyway I removed the offending bolt and bits and bobs and fitted the quick release.
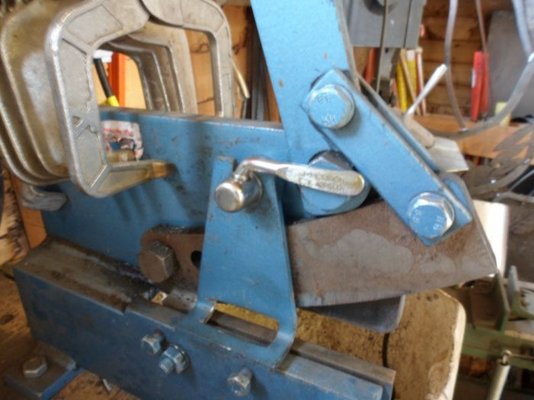
Job done, typically a ten minute job took an hour but worth the effort. Next thing is to make a small support to go a few inches to the left of the shears to help get the height right. I also cut a slot in the thingy so i can see what I am doing when making small cuts.
How did that picture get in twice?
Then I had a go at my belt linisher.
it narked me that I had to fanny about taking two bolts off to access the front roller for working on curved surfaces.
Out with the angle grinder, and slot the holes that the worktable thingy sits on.
Now loosen the bolts, pull it forwards and it drops off nicely.
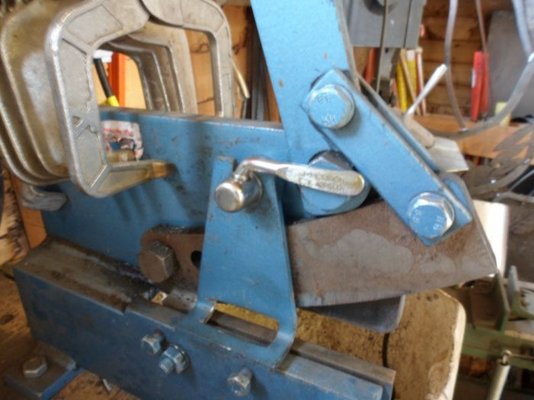
This one did take ten minutes.
I also made a cranked arm for my Power bender but forgot to take a picture.
I always think what the hell am I doing but know that I will be using these 'mods every day at work. Does anybody else take the odd day out to do these kind of things.
They are made by Keetona and needed a spanner and three hands to set up properly.
Every now and again I will 'waste' half a day of workshop time on these little jobs.
I found an old push bike quick release in a box of stuff, that I used years ago for something else, possibly securing a machine vice on a pillar drill.
Anyway I removed the offending bolt and bits and bobs and fitted the quick release.
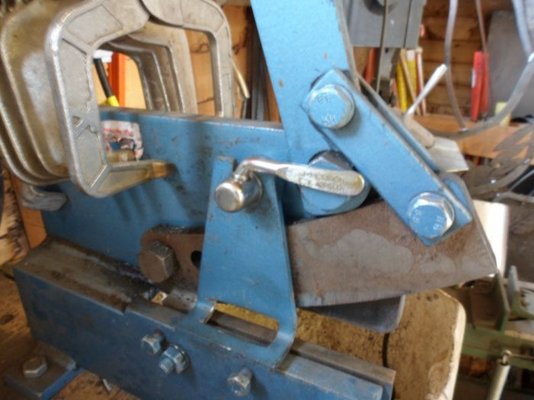
Job done, typically a ten minute job took an hour but worth the effort. Next thing is to make a small support to go a few inches to the left of the shears to help get the height right. I also cut a slot in the thingy so i can see what I am doing when making small cuts.
How did that picture get in twice?
Then I had a go at my belt linisher.
it narked me that I had to fanny about taking two bolts off to access the front roller for working on curved surfaces.
Out with the angle grinder, and slot the holes that the worktable thingy sits on.
Now loosen the bolts, pull it forwards and it drops off nicely.
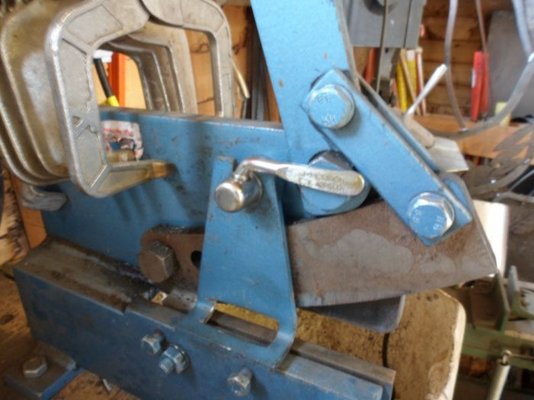
This one did take ten minutes.
I also made a cranked arm for my Power bender but forgot to take a picture.
I always think what the hell am I doing but know that I will be using these 'mods every day at work. Does anybody else take the odd day out to do these kind of things.