shenion
Tool Pack Rat
- Messages
- 7,586
- Location
- Stone Mountain, GA USA
I have an upcoming project to build an overflow tank for my Jeep (parts come in next week.) The tank will be made from 0.090 aluminum and a CNC-machined billet pressure cap.
So, I'll need a sheet metal bender. Checked my fav tool superstore and they have cheap ones that do up to 16ga or huge expensive ones. So, I decided I'll make my own:
Basically it is two pieces of angle iron welded to some door hinges. There is 36" between the hinges. The hinges are installed upside-down. That makes the surfaces of the angle irons almost meet exactly with the center of the hinge pin. It also limits it to bends just over 90 degrees:
To fit the hinges, the angle iron needed to be cut to make room for the pin:
Since the slot for the hinge splits the angle iron, I welded a bridge weld across the corner connecting the two halves and the hinge.
The angle iron is 1.5" x 1/8" steel from discarded bed frames. It is real hard, will take the teeth right off a hack saw, so cuts were made using my LP/O2 torch and a 4" cutoff wheel. The torch cuts were real rough as I don't have the proper tip and still learning how to use it.
There are two pieces of angle iron welded on the ends to allow clamping it to the bench, two pieces of steel pipe (old bycycle frames) were welded as handles.
Tried it on some scrap thin steel. I think it was stainless as it was real hard. The L-steel bowed in the middle. So, I took some 1.25" angle iron (cross supports from bed frame) and boxed it in. Now works better.
The slotted holes in the steel were there from how the bed framed linked together. They turned out handy as I can use them for the C clamps to hold down the brace.
Here is a small piece of 1/16" aluminum, 2 bends on the left were done. Top left used more angle iron to bend against, it shows the radius of the brace. The bottom left used a piece of 1/4" x 3/4" aluminum bar as a brace with square corners (shown in bender on 1st picture). The bend is tighter.
It seems to work OK. It took some fiddling to get the spacing right. Basically clamp both ends to hinges and get it to lay flat and also align up vertically. Welds were sloppy as my wire feeder had problems.
Total costs: $0, all from scrap
If I did it again I'd get 2" L-stock 3/16 thick or better. I'd also use some larger hinges.
So, I'll need a sheet metal bender. Checked my fav tool superstore and they have cheap ones that do up to 16ga or huge expensive ones. So, I decided I'll make my own:
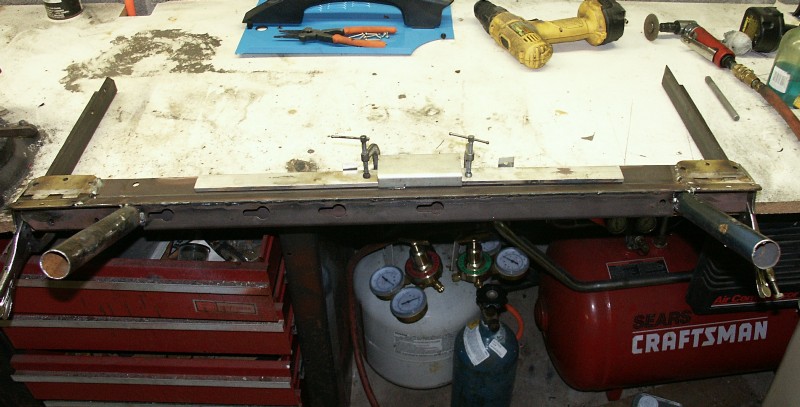
Basically it is two pieces of angle iron welded to some door hinges. There is 36" between the hinges. The hinges are installed upside-down. That makes the surfaces of the angle irons almost meet exactly with the center of the hinge pin. It also limits it to bends just over 90 degrees:

To fit the hinges, the angle iron needed to be cut to make room for the pin:
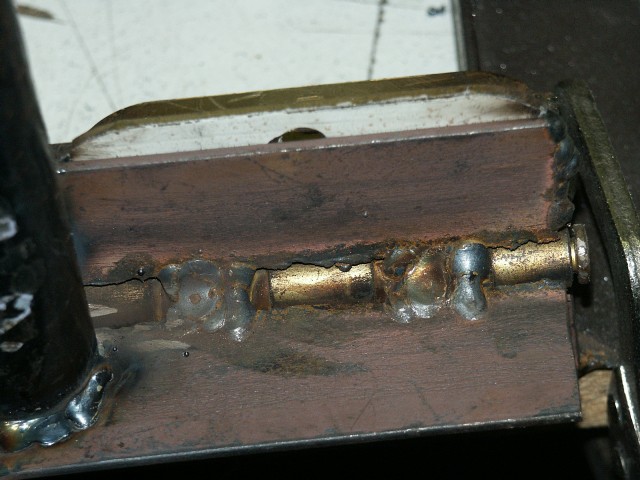
Since the slot for the hinge splits the angle iron, I welded a bridge weld across the corner connecting the two halves and the hinge.
The angle iron is 1.5" x 1/8" steel from discarded bed frames. It is real hard, will take the teeth right off a hack saw, so cuts were made using my LP/O2 torch and a 4" cutoff wheel. The torch cuts were real rough as I don't have the proper tip and still learning how to use it.
There are two pieces of angle iron welded on the ends to allow clamping it to the bench, two pieces of steel pipe (old bycycle frames) were welded as handles.
Tried it on some scrap thin steel. I think it was stainless as it was real hard. The L-steel bowed in the middle. So, I took some 1.25" angle iron (cross supports from bed frame) and boxed it in. Now works better.
The slotted holes in the steel were there from how the bed framed linked together. They turned out handy as I can use them for the C clamps to hold down the brace.
Here is a small piece of 1/16" aluminum, 2 bends on the left were done. Top left used more angle iron to bend against, it shows the radius of the brace. The bottom left used a piece of 1/4" x 3/4" aluminum bar as a brace with square corners (shown in bender on 1st picture). The bend is tighter.
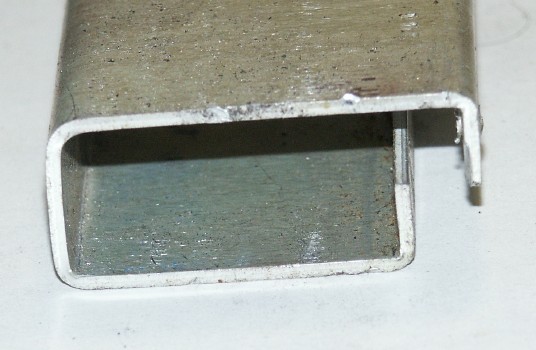
It seems to work OK. It took some fiddling to get the spacing right. Basically clamp both ends to hinges and get it to lay flat and also align up vertically. Welds were sloppy as my wire feeder had problems.
Total costs: $0, all from scrap

If I did it again I'd get 2" L-stock 3/16 thick or better. I'd also use some larger hinges.