burrows1980
Member
- Messages
- 132
- Location
- Buckley, North Wales
Hi,
Over the last few weeks ive been busy building a silent or nearly silent running compressor. I had a Wolfe 2hp Direct drive comp, that as you know was very loud! not very neighbour friendly.
I aquired 7 air conditioning motors ranging from 720W to 1.2kW, ended up using two of the 1.2kW and two 1.1kW motors. I calculated that most of the time I would only need two of the motors running only need four if I was using a lot of air. So I decided to use two pressure switches and two Non return valves, plus the wattage used by for is far more than a 13A fuse can take, not even going into the size flex I would need.
Next was the issue of the oil consumption of the motors and how much they throw out when compressing. I didnt want the oil to enter my receiver if I could help it. It just so happened that my local ALDI had all there recent air tool promotional items at a knock down price, managed to get two Power Craft air filter regulator and oil Lubricator, I admit there not the nest quality, but certainly seem to do the job.
I also wanted to make sure the motors didnt get too hot, so mounted a powerful fan, also from a air con unit, on the back controlled by individual thermostats mounted to each motor, set at 45C, not to sure if this is to low and could cope at 60C will see though.
When I got the motors out of the air con units, they had a cylinder attached to the motor, which seperated the oil from the refrigerant gas, oil collected in the bottom of the cylinder and was fed back into the motor via a drip feed system (1mm hole in the copper pipe):
The pipe that comes out of the motor into the cylinder stops 3/4 way up small filter fitted then about a inch gap before the suction pipe, this acted as a muffler, once I cut it off the motor became really noisey, no difference to a direct drive compressor!! I measured around 60db before I cut the cylinder off then 96db after
So I came up with a elaborate intake system that would make the system quiet again but not restrict the intake in any way. So I made a box out of copper that each motor would be piped into seperately then two 22mm pipes out of the box with a filter on the end ( at the moment a car washing sponge
) :
Without the sponge on the end it makes a proper weird noise, sounds like a deep throaty turbo charged exhuast note, cool
So a few figures now, my old direct drive comp used to fill the receiver to 120psi in 1min 40secs, im not sure if its 25 ltr or 50ltr to be honest, I always thought it was 50ltr but got nothing to compare against at the moment.
So on the original mock up I did to see it the idea would work, 1 motor would reach 60 psi in 1min 24sec two motors acheived it in 54sec, a whole 30 seconds quicker.
With all four running and a slight air leak well a large air leak on a pneumatic push fit connection it reaches 120psi in 53 seconds, when using my spray gun it maintains a steady 90psi when ive set the regulator to 70psi for my gun thats only running with two motors.. I managed to spray my calor 47kg cyclinder today non stop with 4 coats of primer and it didnt break sweat. Still needs refining but its a good set of figures to work with.
Im going to use the cylinder as a Aux receiver, filled that to 120psi as well as the mounted receiver in under 5 minutes, more than happy with that, so a possible 150ltr of air.. Im going to try and work out the cfm of it, its defo enough for what I want to do and best of all its really quiet, only problem that annoys me is when the blow off valve vents from the pressure set in the pressure switch, thats the only loud bit, but the air in the comps needs to be realeased, blows the fuse if they try and start under excessive load. The pipe work is as short as I can possible make it, might work out a way of quietening the sound from the pressure swt when releasing...
So heres a few ok a lot of photos of the build ( dont laugh at the welds!! im a first time welder just learning how at the mo!!):
Underneath Chassis
Motor Mounts
Air Box
Intake Pipes Installed & shopping trolley front wheels......
Motor Capacitors & Wiring Conduit
Wining going in, 1.5mm singles
Wiring through for motors & Temp sensors
Spacer installed to stop vibrations
First two motors installed and connected
Temp sensor attached
All four motors mounted
All four wired in...
Pipe seen coming out of motor is the one that was inside the cylinder I cut off, these differ in size not normal metric british copper pipe size, had to braize 15mm to it
Oil fill pipes installed with a iso valve, with out this the air box doesnt do its job, becomes a noisey system
GTi-R in the back ground, pride and joy.....
Receiver fitted...
Oil seperators mounted...
Ended up changing these pneumatic pipes to copper, space was to tight to use nylon pipe wouldnt bend tight enough put far to much pressure on the pushfit fittings, oh and a view of my dodgy welding :-)
Wiring nearly finished....
Time for a safety inspection from the cat!! it passed, phew....
Air pressure switches fitted...
Large non return valve fitted, machine mart sent wrong one oh well made it fit, makes a cool sound when it opens, like a super charger whine!!
Auxiliary gate valve installed to connect a extra receiver to..
Finished, woohoo....
Car wash sponge wedged in....
Push fits im chaging to braized pipe, they leak to much, the 8mm copper out of the comp is dented slightly, so cant make a proper seal...
All primed up ready for top coat..
I will get a video of it running soon,
Hopefully this has been useful and maybe a little informative
Thanks
Gaz
Over the last few weeks ive been busy building a silent or nearly silent running compressor. I had a Wolfe 2hp Direct drive comp, that as you know was very loud! not very neighbour friendly.
I aquired 7 air conditioning motors ranging from 720W to 1.2kW, ended up using two of the 1.2kW and two 1.1kW motors. I calculated that most of the time I would only need two of the motors running only need four if I was using a lot of air. So I decided to use two pressure switches and two Non return valves, plus the wattage used by for is far more than a 13A fuse can take, not even going into the size flex I would need.
Next was the issue of the oil consumption of the motors and how much they throw out when compressing. I didnt want the oil to enter my receiver if I could help it. It just so happened that my local ALDI had all there recent air tool promotional items at a knock down price, managed to get two Power Craft air filter regulator and oil Lubricator, I admit there not the nest quality, but certainly seem to do the job.
I also wanted to make sure the motors didnt get too hot, so mounted a powerful fan, also from a air con unit, on the back controlled by individual thermostats mounted to each motor, set at 45C, not to sure if this is to low and could cope at 60C will see though.
When I got the motors out of the air con units, they had a cylinder attached to the motor, which seperated the oil from the refrigerant gas, oil collected in the bottom of the cylinder and was fed back into the motor via a drip feed system (1mm hole in the copper pipe):
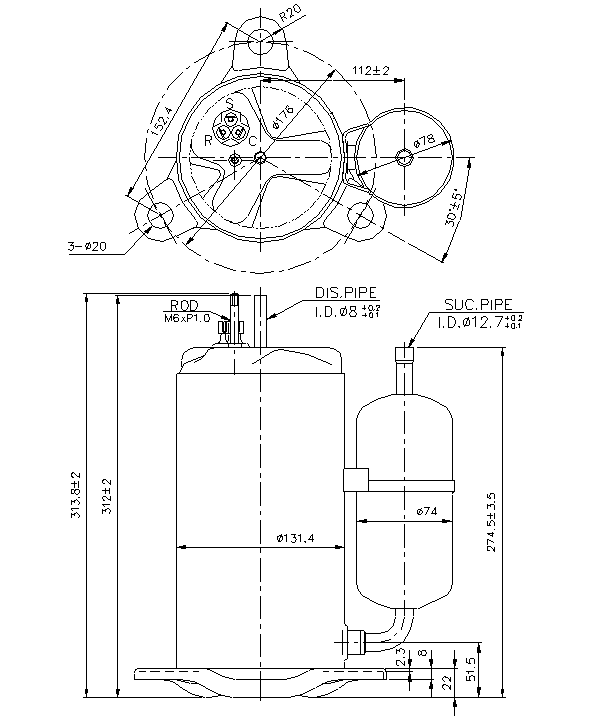
The pipe that comes out of the motor into the cylinder stops 3/4 way up small filter fitted then about a inch gap before the suction pipe, this acted as a muffler, once I cut it off the motor became really noisey, no difference to a direct drive compressor!! I measured around 60db before I cut the cylinder off then 96db after

So I came up with a elaborate intake system that would make the system quiet again but not restrict the intake in any way. So I made a box out of copper that each motor would be piped into seperately then two 22mm pipes out of the box with a filter on the end ( at the moment a car washing sponge

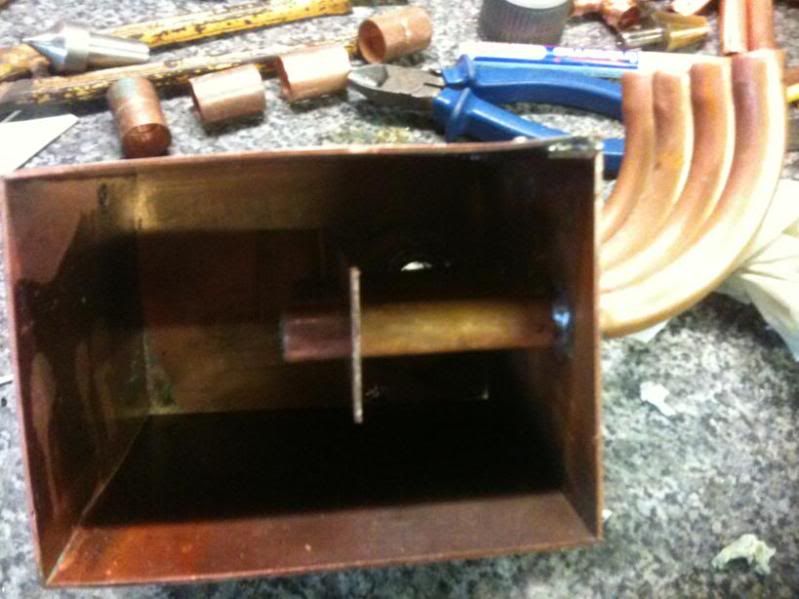
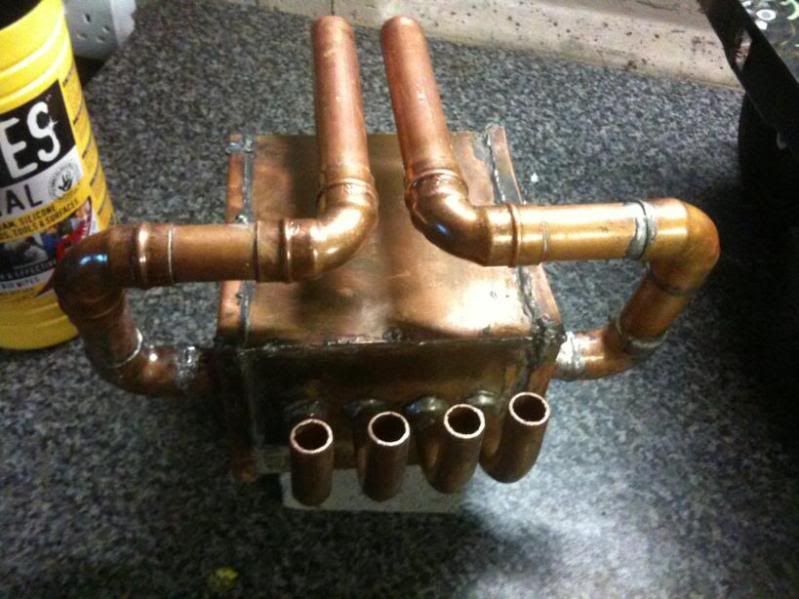
Without the sponge on the end it makes a proper weird noise, sounds like a deep throaty turbo charged exhuast note, cool

So a few figures now, my old direct drive comp used to fill the receiver to 120psi in 1min 40secs, im not sure if its 25 ltr or 50ltr to be honest, I always thought it was 50ltr but got nothing to compare against at the moment.
So on the original mock up I did to see it the idea would work, 1 motor would reach 60 psi in 1min 24sec two motors acheived it in 54sec, a whole 30 seconds quicker.
With all four running and a slight air leak well a large air leak on a pneumatic push fit connection it reaches 120psi in 53 seconds, when using my spray gun it maintains a steady 90psi when ive set the regulator to 70psi for my gun thats only running with two motors.. I managed to spray my calor 47kg cyclinder today non stop with 4 coats of primer and it didnt break sweat. Still needs refining but its a good set of figures to work with.
Im going to use the cylinder as a Aux receiver, filled that to 120psi as well as the mounted receiver in under 5 minutes, more than happy with that, so a possible 150ltr of air.. Im going to try and work out the cfm of it, its defo enough for what I want to do and best of all its really quiet, only problem that annoys me is when the blow off valve vents from the pressure set in the pressure switch, thats the only loud bit, but the air in the comps needs to be realeased, blows the fuse if they try and start under excessive load. The pipe work is as short as I can possible make it, might work out a way of quietening the sound from the pressure swt when releasing...
So heres a few ok a lot of photos of the build ( dont laugh at the welds!! im a first time welder just learning how at the mo!!):
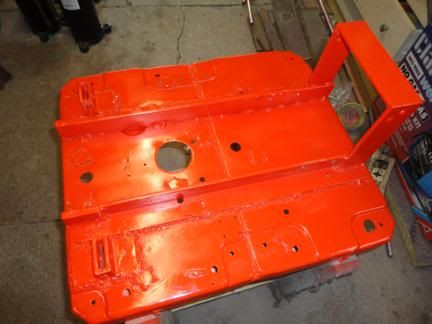
Underneath Chassis
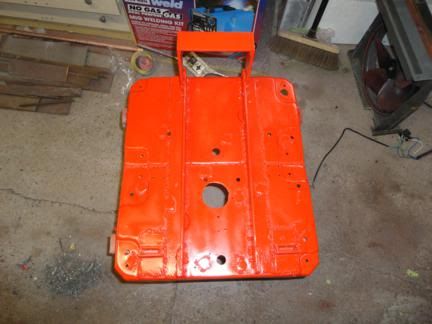
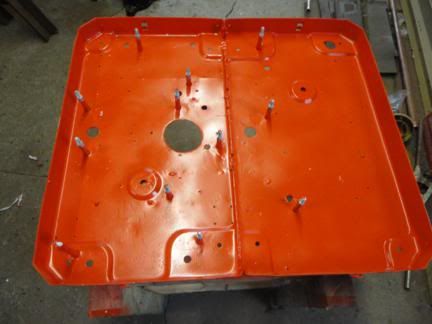
Motor Mounts
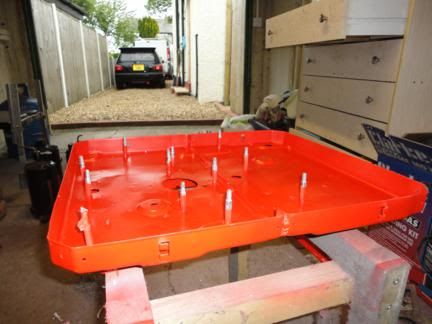
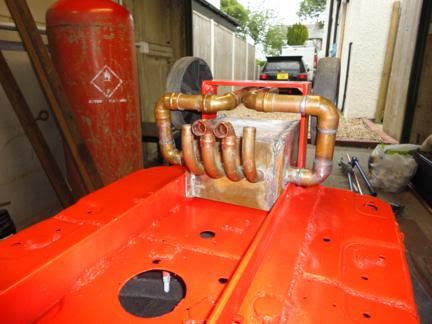
Air Box
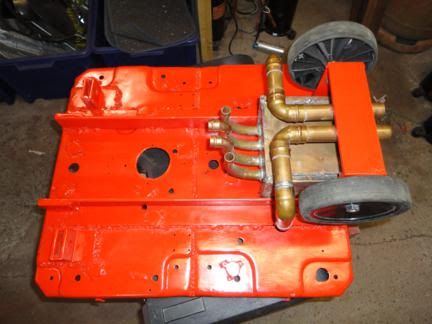
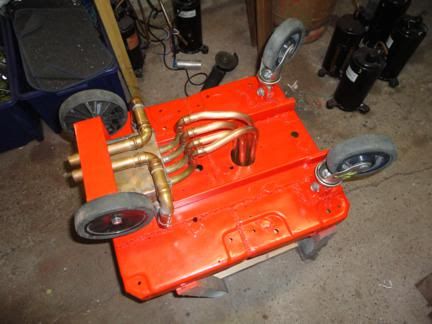
Intake Pipes Installed & shopping trolley front wheels......
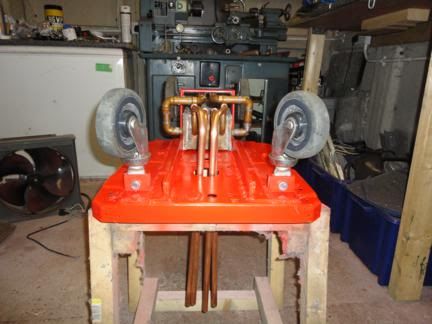
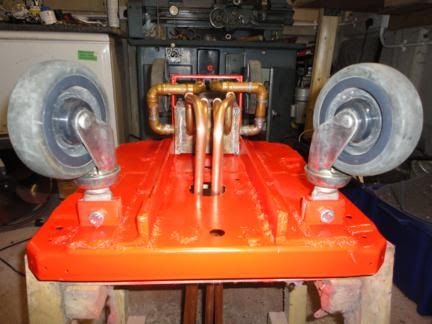
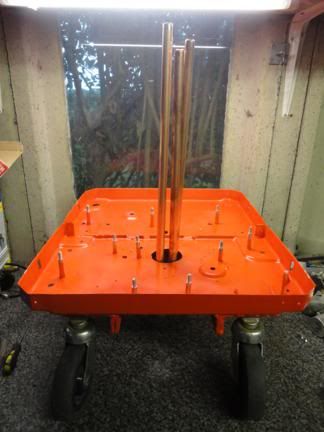
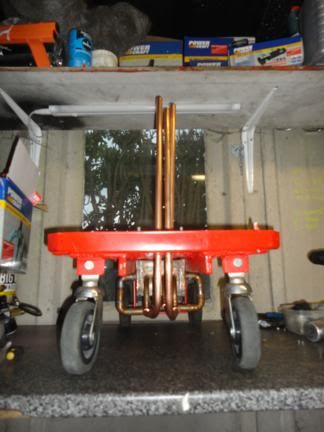
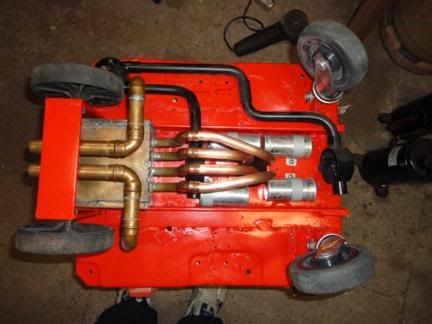
Motor Capacitors & Wiring Conduit
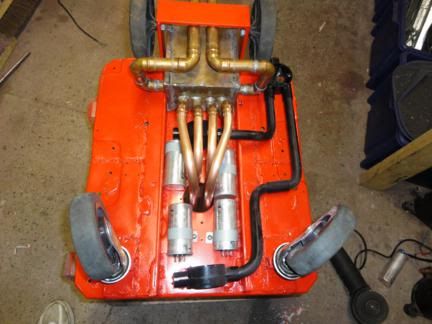
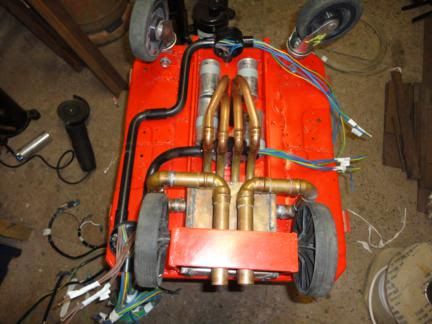
Wining going in, 1.5mm singles
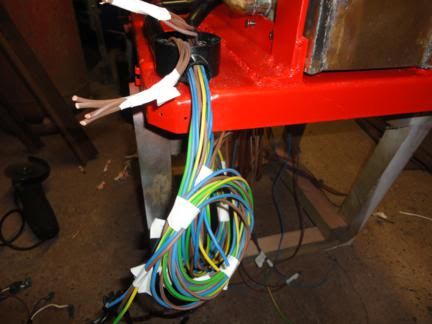
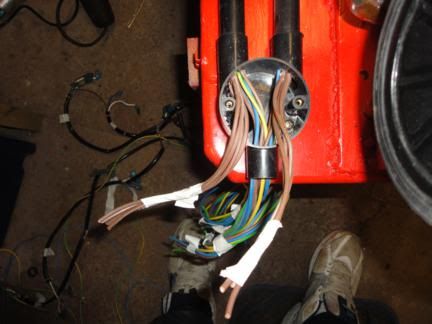
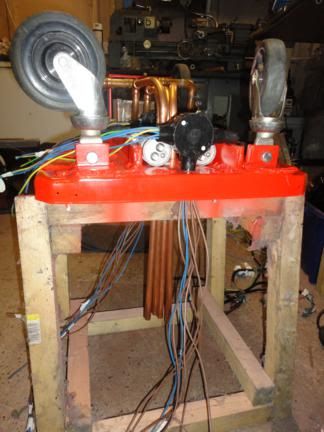
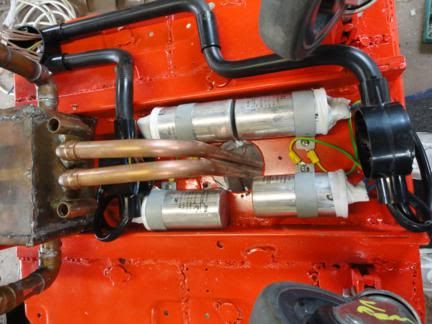
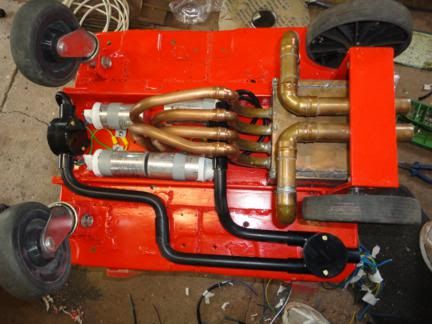
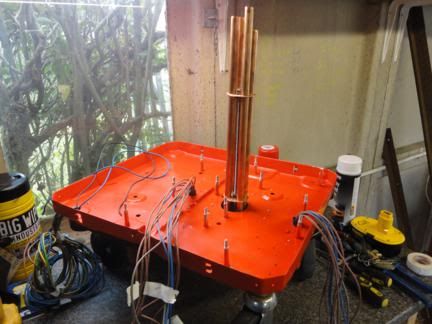
Wiring through for motors & Temp sensors
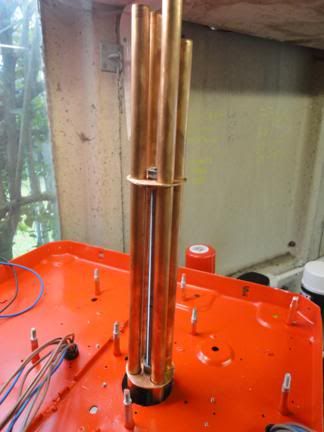
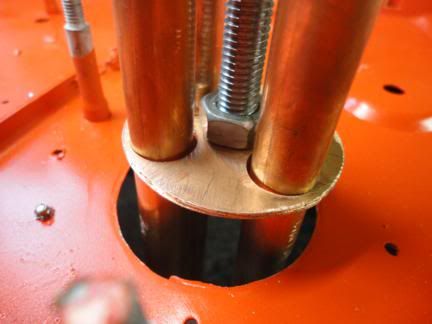
Spacer installed to stop vibrations
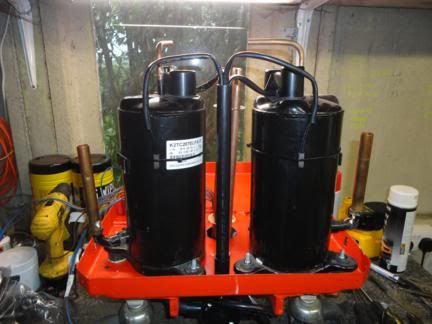
First two motors installed and connected
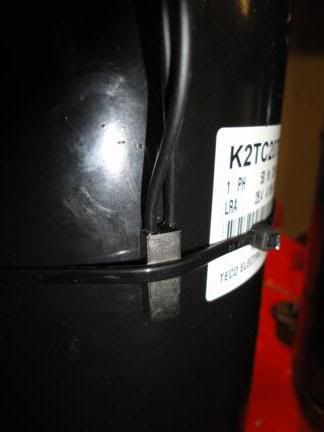
Temp sensor attached
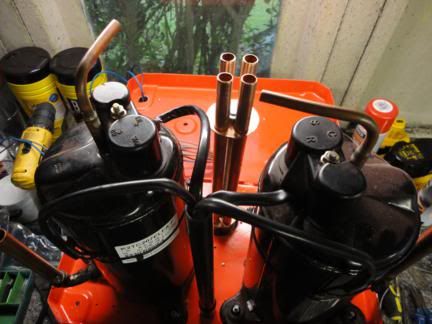
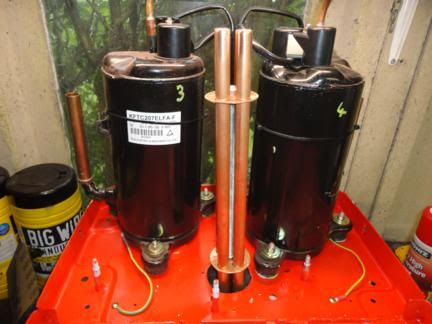
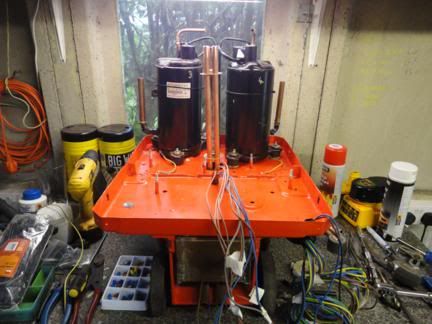
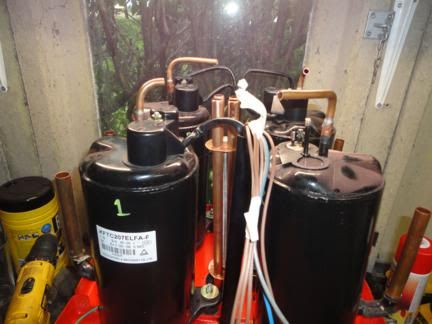
All four motors mounted
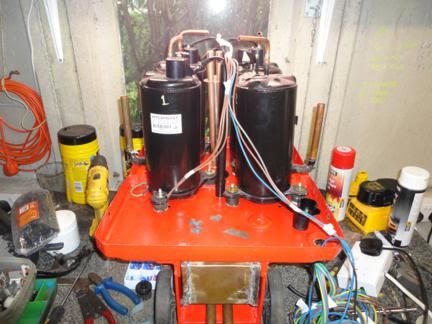
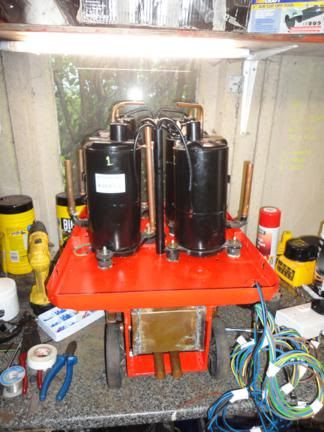
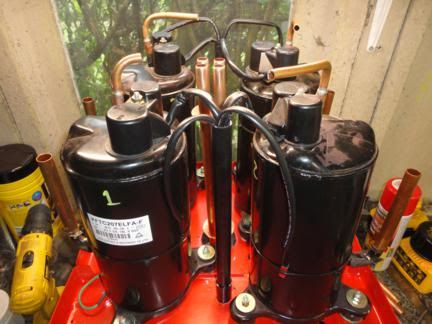
All four wired in...
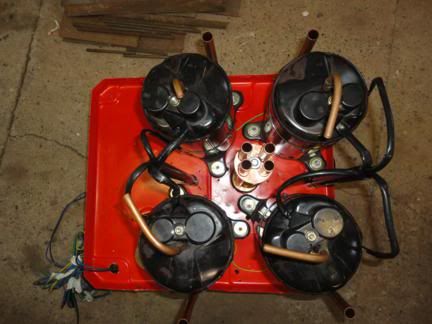
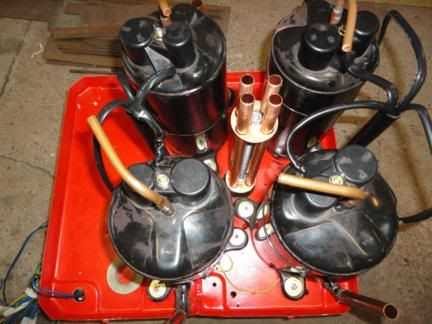
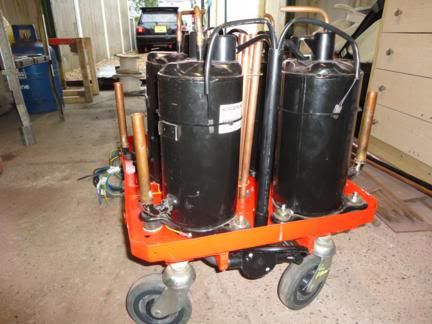
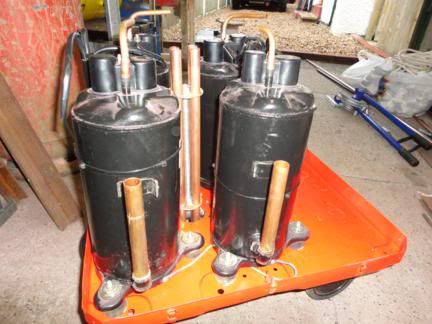
Pipe seen coming out of motor is the one that was inside the cylinder I cut off, these differ in size not normal metric british copper pipe size, had to braize 15mm to it
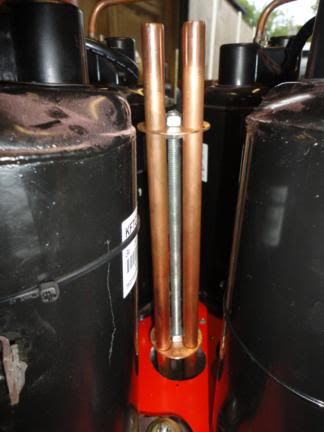
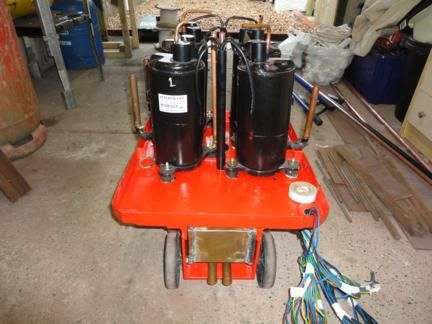
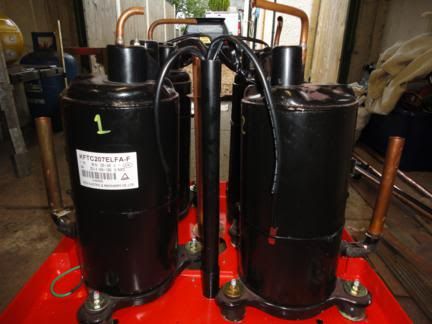
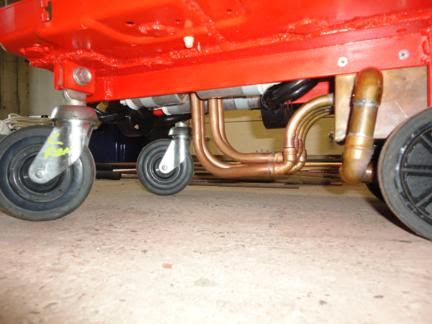
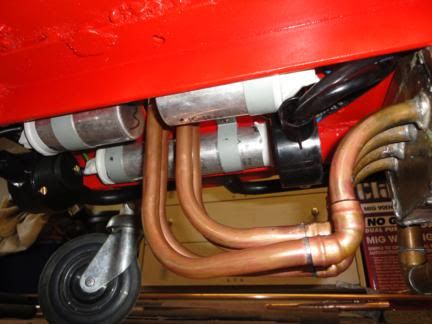
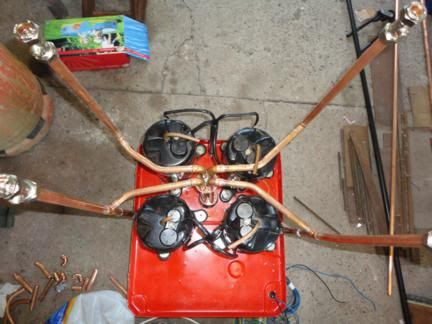
Oil fill pipes installed with a iso valve, with out this the air box doesnt do its job, becomes a noisey system
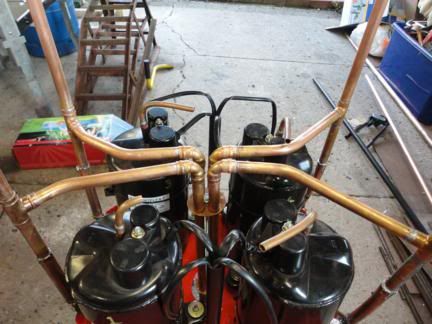
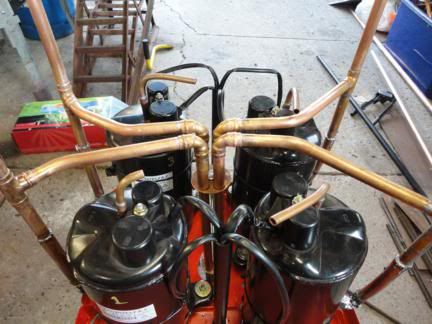
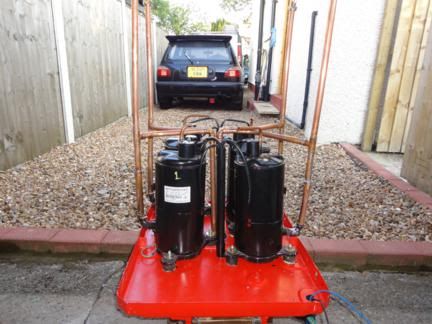
GTi-R in the back ground, pride and joy.....
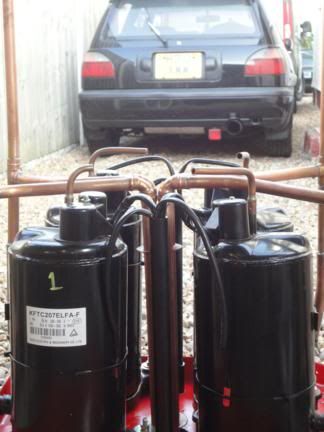
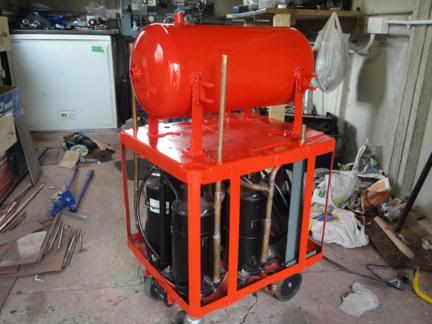
Receiver fitted...
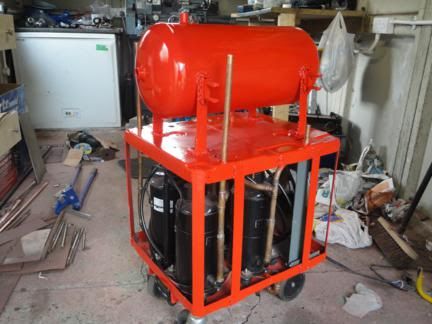
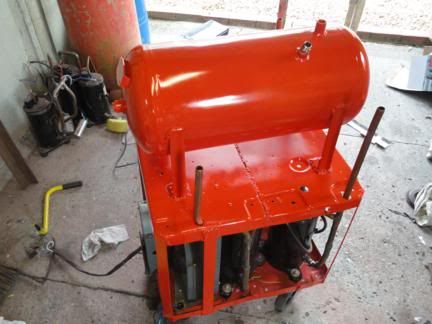
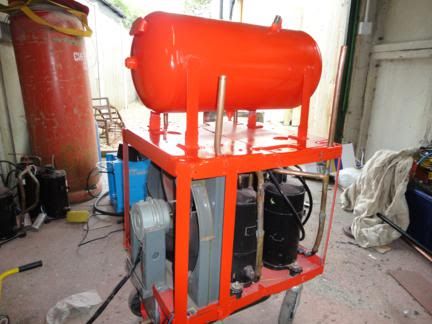
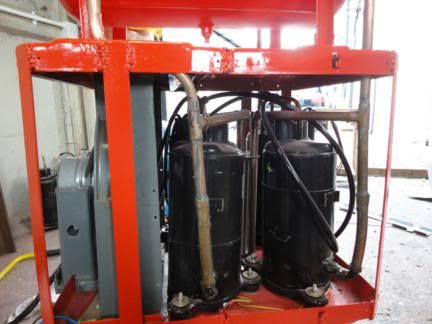
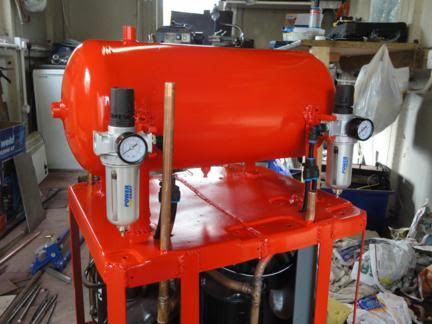
Oil seperators mounted...
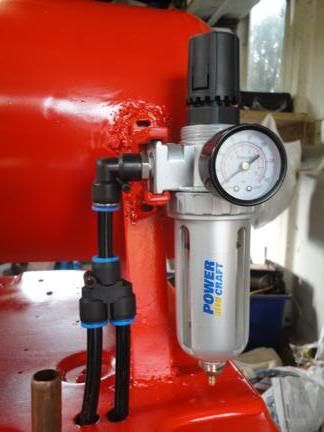
Ended up changing these pneumatic pipes to copper, space was to tight to use nylon pipe wouldnt bend tight enough put far to much pressure on the pushfit fittings, oh and a view of my dodgy welding :-)
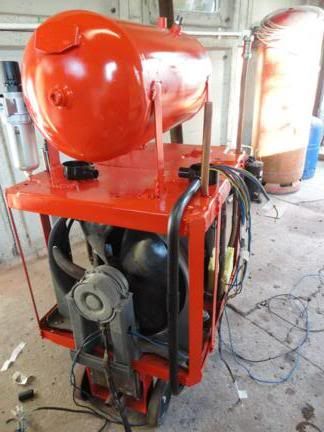
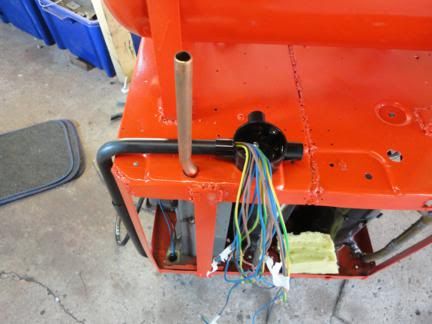
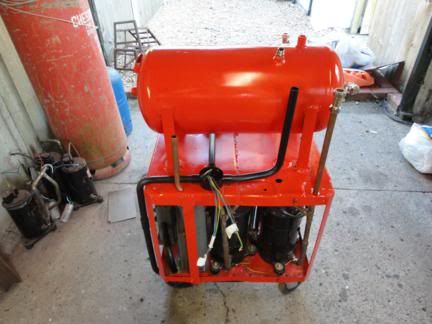
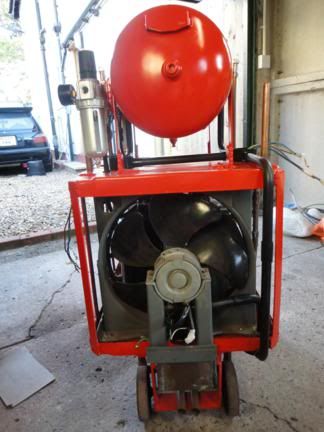
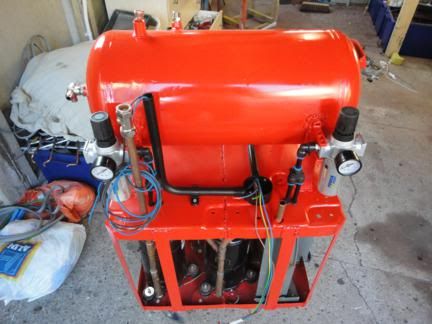
Wiring nearly finished....
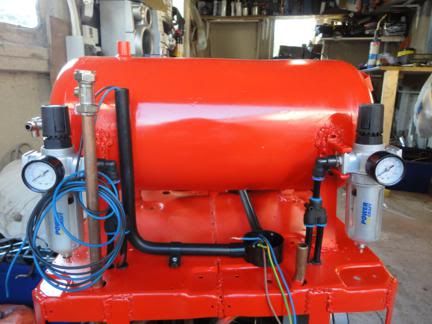
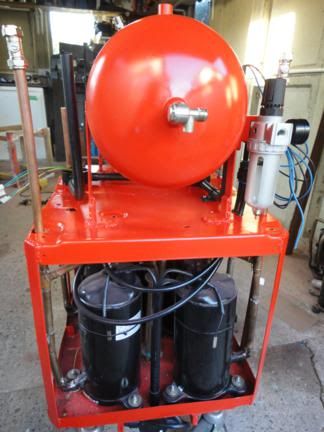
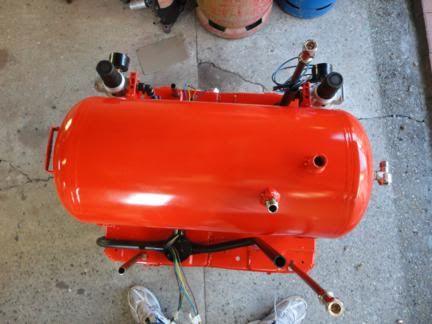
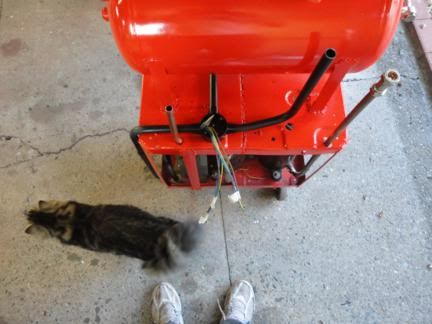
Time for a safety inspection from the cat!! it passed, phew....
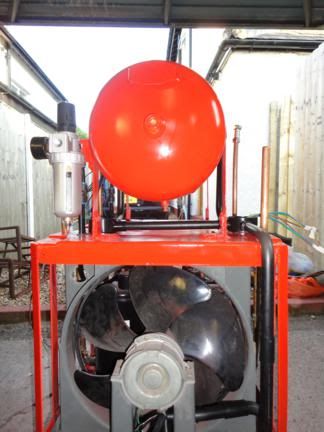
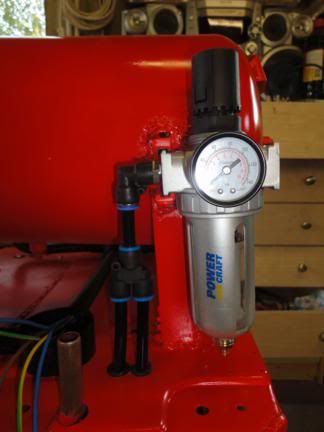
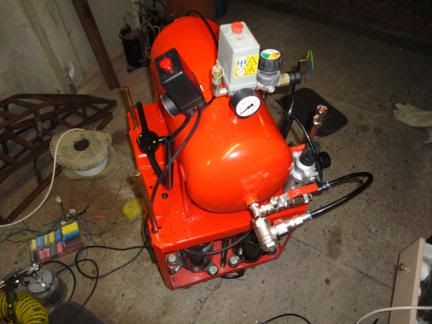
Air pressure switches fitted...
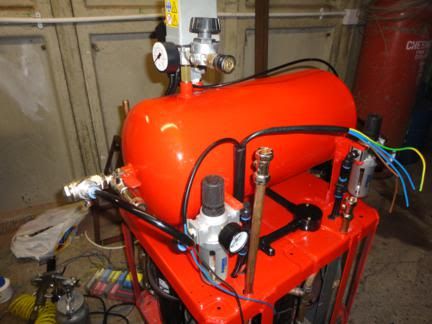
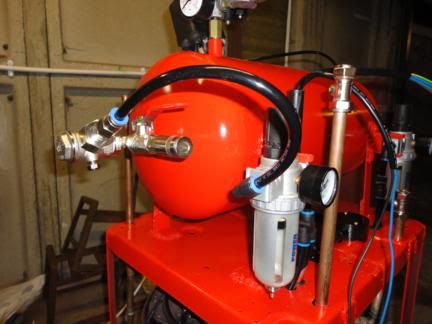
Large non return valve fitted, machine mart sent wrong one oh well made it fit, makes a cool sound when it opens, like a super charger whine!!
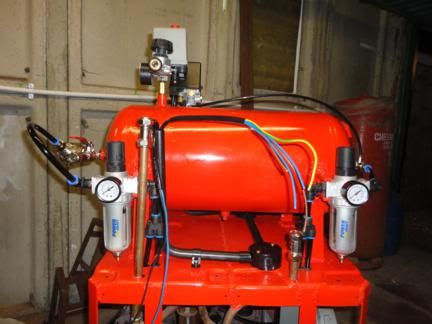
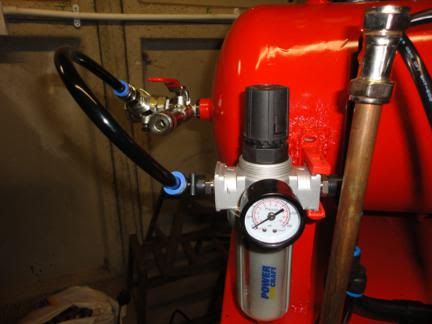
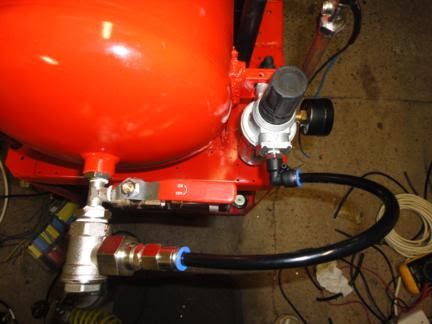
Auxiliary gate valve installed to connect a extra receiver to..
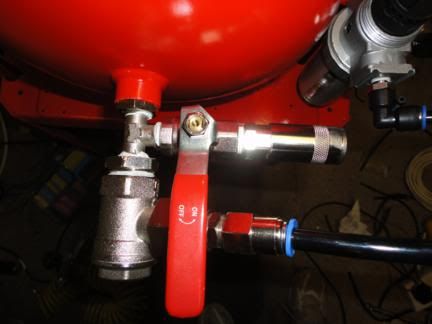
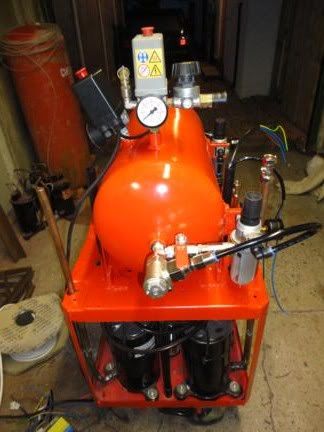
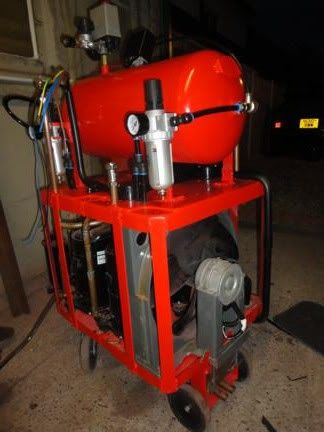
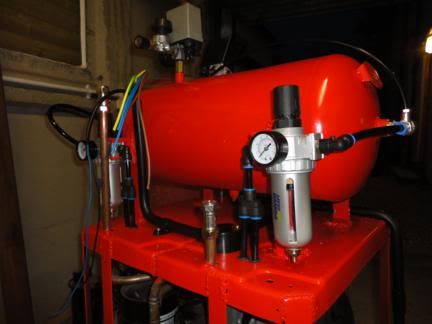
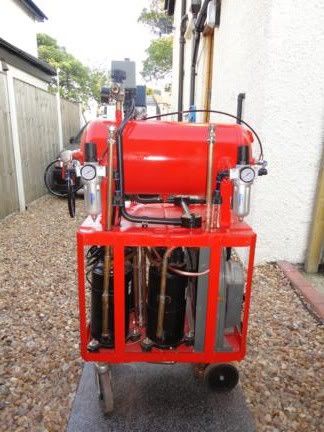
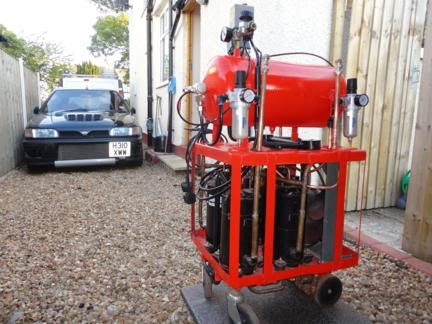
Finished, woohoo....
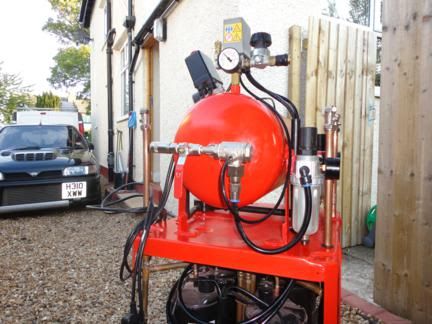
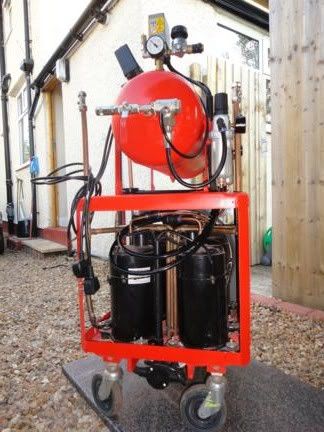
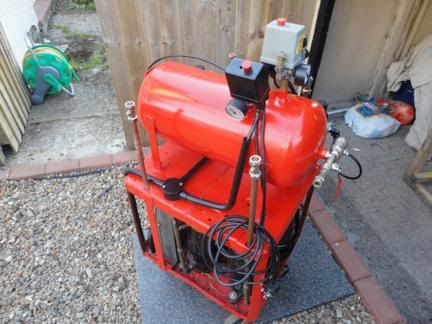
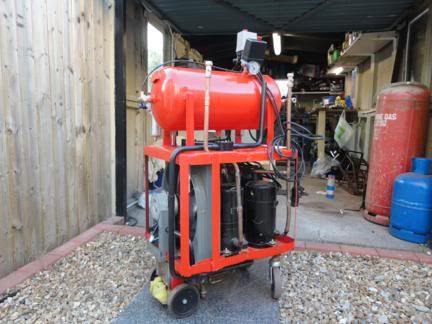
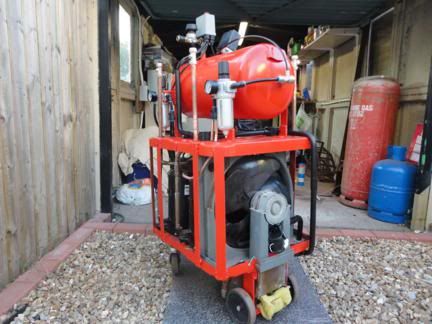
Car wash sponge wedged in....
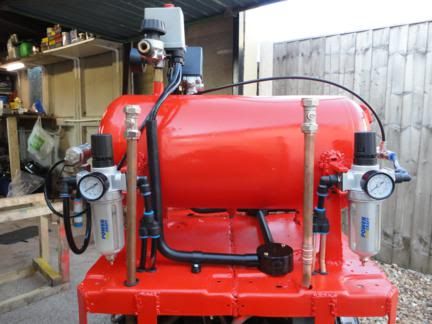
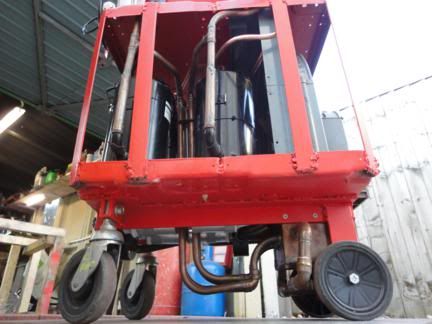
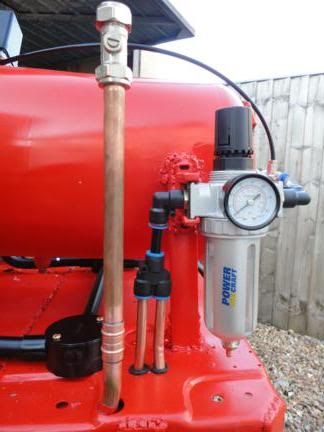
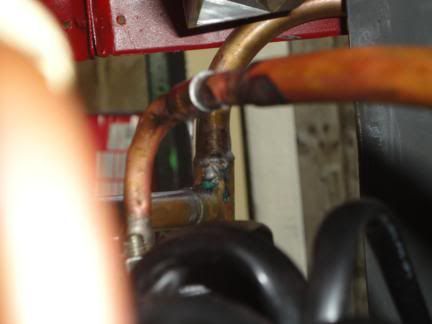
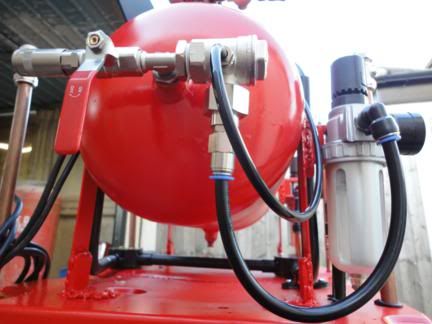
Push fits im chaging to braized pipe, they leak to much, the 8mm copper out of the comp is dented slightly, so cant make a proper seal...
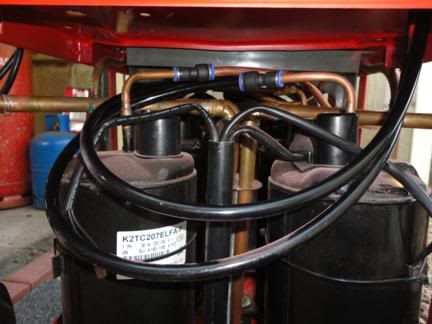
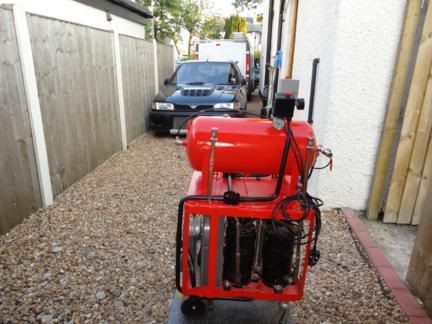
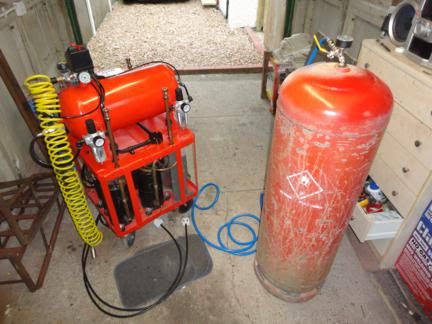
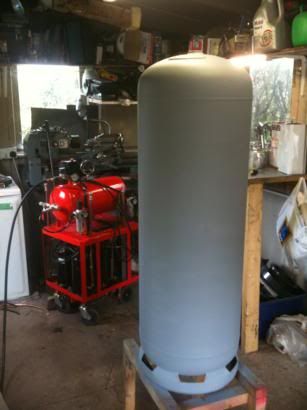
All primed up ready for top coat..
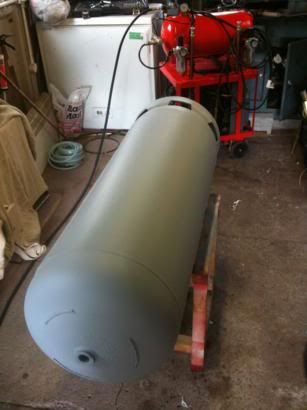
I will get a video of it running soon,
Hopefully this has been useful and maybe a little informative

Thanks
Gaz