zzr1200
Working at 650 ft on open steel work.
- Messages
- 6,295
- Location
- Glapwell, Chesterfield, Derbyshire, UK
I've owned my plasma cutter for several years now, but never really been happy with the quality of the cuts in material above 13mm (steel), and never achieved the 18mm clean cut/24mm severance, plus the tips always seemed to burn out quickly.
I needed to stock up on consumables again but couldn't find any sensibly price tips and I'd never found any drag tips for the LT70 torch, supplied with the HF50 machine, so the hunt was on, I ended up ordering a LT80 plasma torch which has a higher amp age capacity and much cheaper cutting tips.
A few weeks later the torch arrived, then a wait for the new cutting tips (1.1 and 1.3mm), I used the cables/pipes/protective sheaf from the original torch assembly the only difference is the way the main supply pipe is connected to the torch head this is easy to over come by either, removing the barrel olive/pipe nut from the original torch or buying a new 6mm barrel olive/nut. the new LT80 torch has a soldered on connector nut that has to be removed or cut off.
I cut off the soldered on connector on the new torch, cut back the plastic sleeve and pulled off the barrel olive off of the original torch to use it again on the new one, because I couldn't find my box of olives they are in the workshop SOMEWHERE.....
.
Both the LT70 and LT80 use a 6mm pipe for the plasma head/pipe connection just different connectors.
I found that when trying the new torch out the Plasma Stream/Flame spat and cut out intermittently, this is caused by high air pressure (75psi) recommended by R Tech, I reduced the pressure and the plasma stream stabilized, the pressure required seems to change with tip size and design.
This weekend was the first real test for the new torch head, I had to make several cuts in 15mm plate, the cut quality compared to the old torch is immense, the plasma was at full power (50amp), using a 1.3mm hole tip and 40psi air pressure, I use an Aldi V2 direct drive compressor, while cutting the compressor started up built up pressure a cut out again, so air fed from a small tanked 13 cfm compressor is not a problem.
One of the photos shows the soldered on connector (ringed in orange and the plastic cover that needs to be cut back in blue) that has to be removed to fit/use the original power cable/air pipe, when the torch is dismantled the yellow safety trigger guard pivot (green ring) pops out of its pivot hole (purple ring) which makes reassembly fun until you figure out what's happened......
.
There are 4 tip hole sizes for the LT80 torch 1.1mm, 1.3mm, 1.5mm and 1.7mm so be aware if you change torches, I have 1.1mm, 1.3mm and 1.5mm (supplied with the torch).
So below are the pictures of the LT80 torch fitted to the original cables/pipe, the material cuts are all in15mm plate and hand held with the standard outer shield, as yet I haven't had time to play with a drag nozzle but I will soon.
Your opinions on cut quality and any inputs to improve them would help...

I needed to stock up on consumables again but couldn't find any sensibly price tips and I'd never found any drag tips for the LT70 torch, supplied with the HF50 machine, so the hunt was on, I ended up ordering a LT80 plasma torch which has a higher amp age capacity and much cheaper cutting tips.
A few weeks later the torch arrived, then a wait for the new cutting tips (1.1 and 1.3mm), I used the cables/pipes/protective sheaf from the original torch assembly the only difference is the way the main supply pipe is connected to the torch head this is easy to over come by either, removing the barrel olive/pipe nut from the original torch or buying a new 6mm barrel olive/nut. the new LT80 torch has a soldered on connector nut that has to be removed or cut off.
I cut off the soldered on connector on the new torch, cut back the plastic sleeve and pulled off the barrel olive off of the original torch to use it again on the new one, because I couldn't find my box of olives they are in the workshop SOMEWHERE.....

Both the LT70 and LT80 use a 6mm pipe for the plasma head/pipe connection just different connectors.
I found that when trying the new torch out the Plasma Stream/Flame spat and cut out intermittently, this is caused by high air pressure (75psi) recommended by R Tech, I reduced the pressure and the plasma stream stabilized, the pressure required seems to change with tip size and design.
This weekend was the first real test for the new torch head, I had to make several cuts in 15mm plate, the cut quality compared to the old torch is immense, the plasma was at full power (50amp), using a 1.3mm hole tip and 40psi air pressure, I use an Aldi V2 direct drive compressor, while cutting the compressor started up built up pressure a cut out again, so air fed from a small tanked 13 cfm compressor is not a problem.
One of the photos shows the soldered on connector (ringed in orange and the plastic cover that needs to be cut back in blue) that has to be removed to fit/use the original power cable/air pipe, when the torch is dismantled the yellow safety trigger guard pivot (green ring) pops out of its pivot hole (purple ring) which makes reassembly fun until you figure out what's happened......

There are 4 tip hole sizes for the LT80 torch 1.1mm, 1.3mm, 1.5mm and 1.7mm so be aware if you change torches, I have 1.1mm, 1.3mm and 1.5mm (supplied with the torch).
So below are the pictures of the LT80 torch fitted to the original cables/pipe, the material cuts are all in15mm plate and hand held with the standard outer shield, as yet I haven't had time to play with a drag nozzle but I will soon.
Your opinions on cut quality and any inputs to improve them would help...
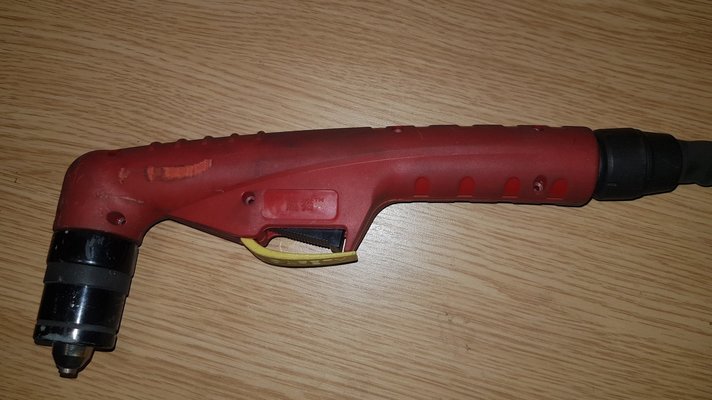
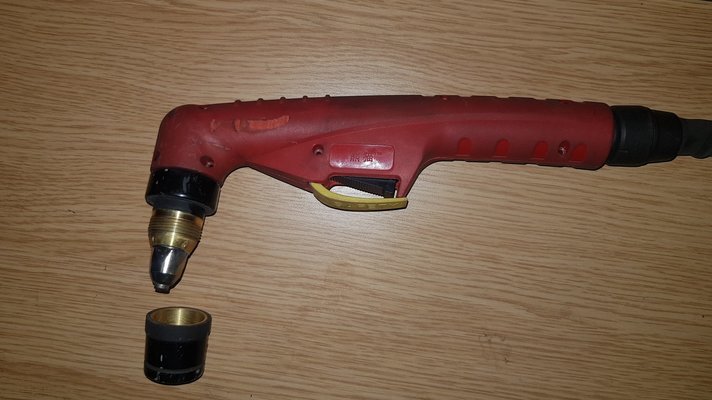
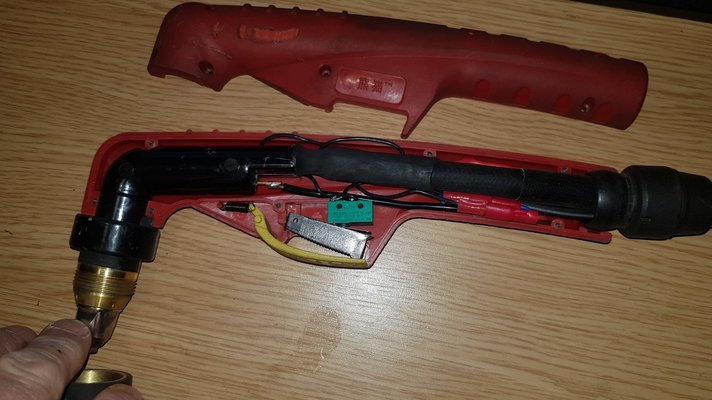
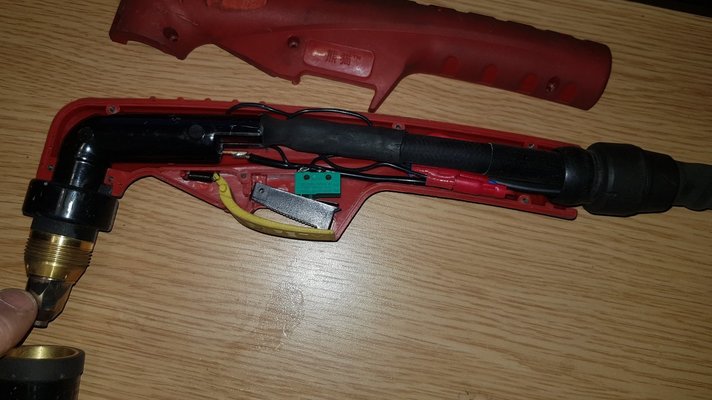
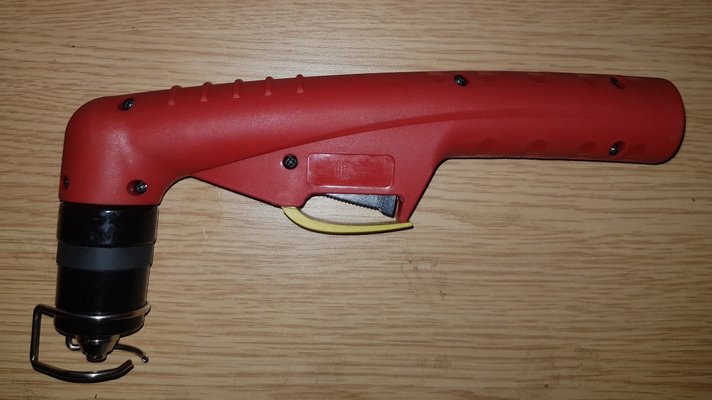
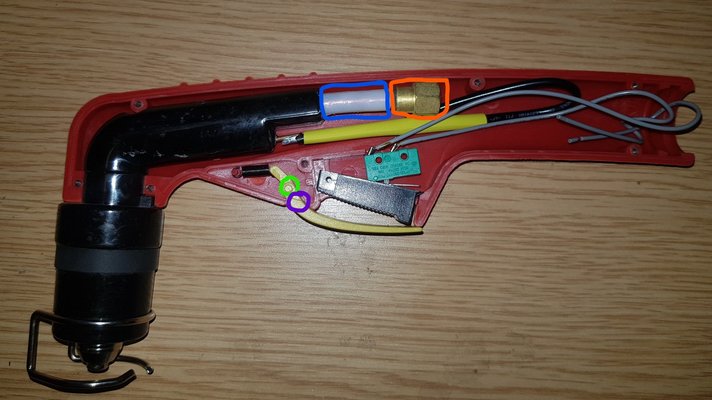
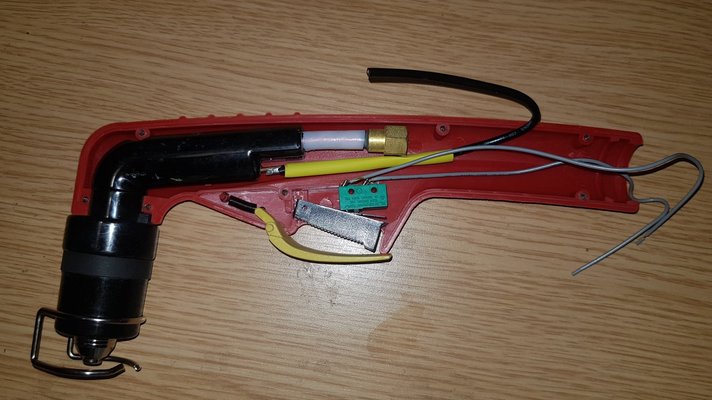

Last edited: