You're off to a good start there mccarthy, it is going to take a fair bit of practice. I know i keep banging on about it but arc length is paramount for this sort of thing, especially stainless and especially autogenous stainless- as arc length increases so does weld size. Looks to me like your arc length is too long (no more than the tungsten diameter ideally), movements are a bit inconsistant (losing the torch angle as you progress around the tube?) and that the purge didn't work properly.
Virtually everyone would struggle to reach the consistancy of the examples you posted unless they're doing this sort of work nearly every day. First looks man made to me, second looks like a high frequency pulsed weld i reckon mechanised
With practice you can get welds with filler virtually as neat as pulsed autogenous, smaller diameter filler will help here. Welded up some intercooler pipework (1.6mm 316L) and some exhaust bits today, owner fabricated it and didn't pay attention when i told him to 'split' the angle when cutting the tube so that it fits...
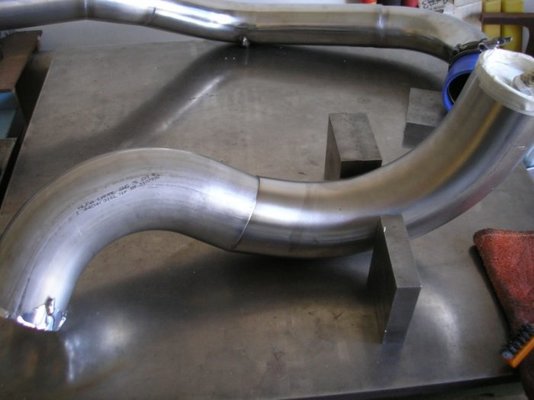
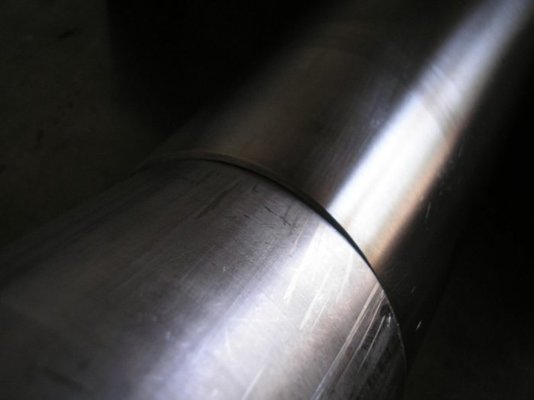
Not really a gap as such but enough of a missmatch to prevent neat results/cause burn through unless filler is used
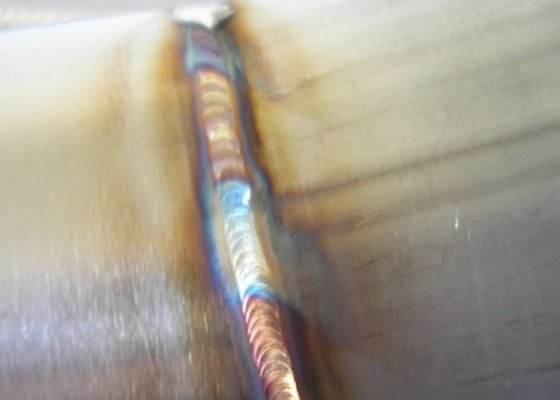
Half of this section of weld was done with filler (1.2mm) the other half is pulsed autogenous
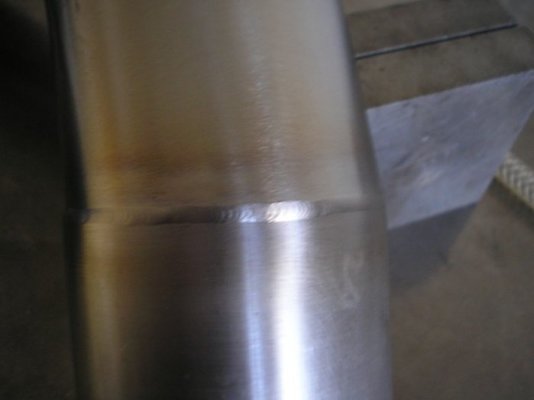
Nowhere close to as consistant as the examples posted in the OP but as long as you don't get too close...
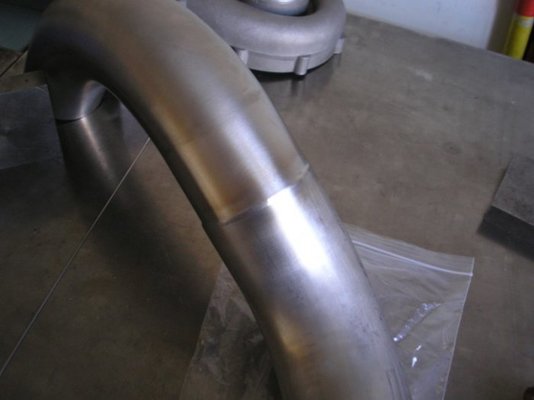
As Rodofgod said, the purge plays a key role. Obviously O2 needs to be excluded but pressure can play a role too. You only need enough to keep the air out, too much can cause problems when closing the joint (blow puddle out) but a little pressure can help weld profile by supporting the puddle. I don't know of any rules of thumb but FWIW i typically use a smaller exit hole for autogenous work, poked a single hole with the 1.2mm filler in this case and left the purge running at 3L/min instead of turning it down to a trickle. Obviously the volume to purged effects things
Virtually everyone would struggle to reach the consistancy of the examples you posted unless they're doing this sort of work nearly every day. First looks man made to me, second looks like a high frequency pulsed weld i reckon mechanised
With practice you can get welds with filler virtually as neat as pulsed autogenous, smaller diameter filler will help here. Welded up some intercooler pipework (1.6mm 316L) and some exhaust bits today, owner fabricated it and didn't pay attention when i told him to 'split' the angle when cutting the tube so that it fits...
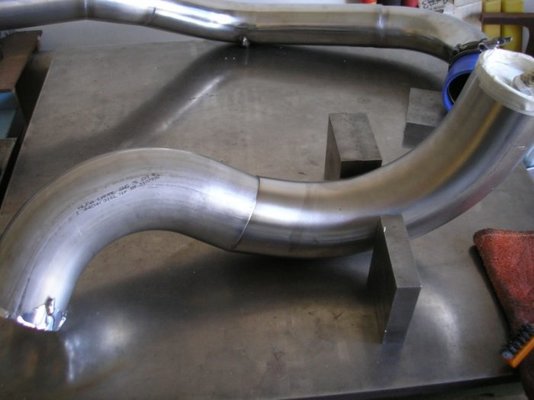
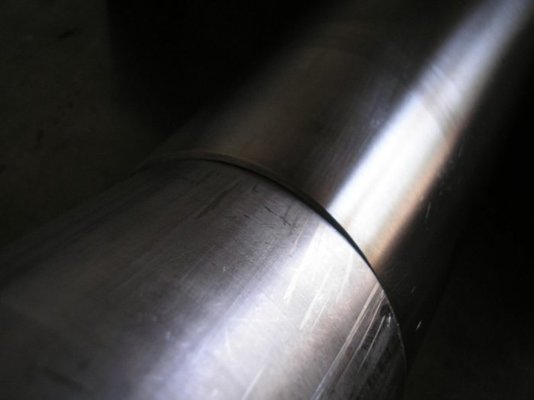
Not really a gap as such but enough of a missmatch to prevent neat results/cause burn through unless filler is used
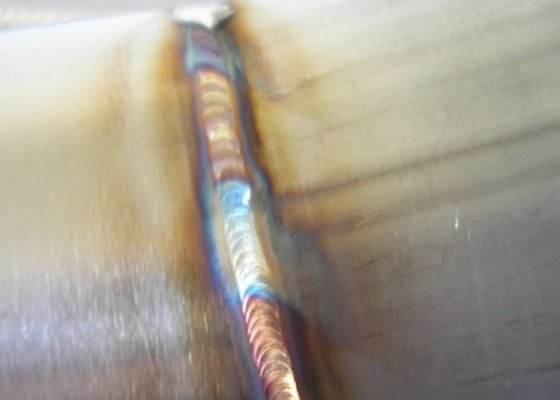
Half of this section of weld was done with filler (1.2mm) the other half is pulsed autogenous
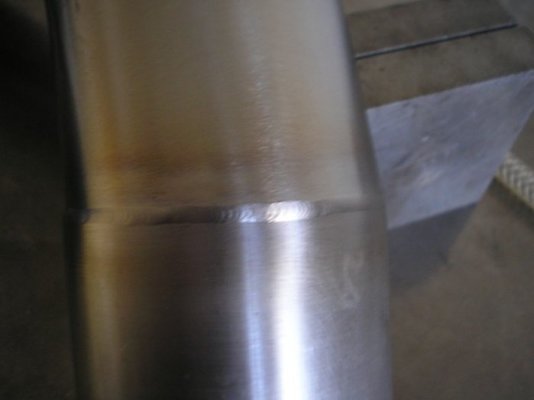
Nowhere close to as consistant as the examples posted in the OP but as long as you don't get too close...
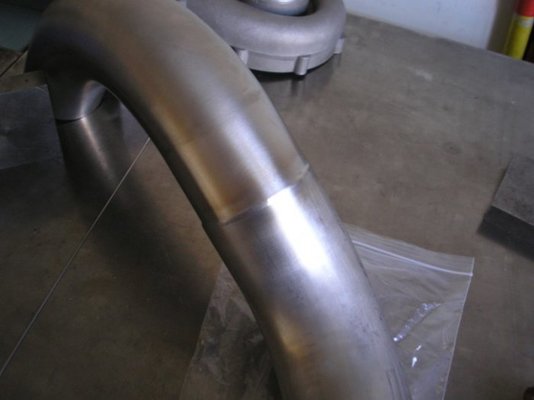
As Rodofgod said, the purge plays a key role. Obviously O2 needs to be excluded but pressure can play a role too. You only need enough to keep the air out, too much can cause problems when closing the joint (blow puddle out) but a little pressure can help weld profile by supporting the puddle. I don't know of any rules of thumb but FWIW i typically use a smaller exit hole for autogenous work, poked a single hole with the 1.2mm filler in this case and left the purge running at 3L/min instead of turning it down to a trickle. Obviously the volume to purged effects things