Buying an Arc Welder
Arc welding is only really suitable for metal over about 3mm. It can be used down to 2mm but becomes very fiddly and difficult to control. It's no good at all for welding cars! For metal below 3mm a MIG or TIG welder would be more suitable.
Arc welding is a strong and economic way to join thicker materials, especially when restricted to a domestic power supply. Where a MIG welder would require an increased power output for thicker materials, an smaller arc welder can often be used by increasing the number of passes instead of increasing the amps.
Which Welder to buy?
For the majority of people (those who don't have any special requirements) a DC inverter is the best type of arc welder to look for. They are the easiest type of arc welder to use, portable, and less demanding on power supplies than other types of arc welder.
Even the cheapest Chinese inverter welders perform reasonably well, but at the time of writing (2010) they aren't known for their reliability or support. There are many reports on the forum of cheap inverter welders failing within a few weeks of purchase. eBay tends to be the source and warranties can be tricky on there. Chinese made welders are best purchased from established UK based suppliers who can satisfy the warranty. It is in the interest of these suppliers to supply half decent ones to save on warranty claims.
Inverter welders do go wrong - they can be sensitive to knocks, power surges from the mains, dust and internal corrosion. Repairs will often cost more than the welder cost to buy in the first place. The difference between Chinese and European made inverters tends to be how sensitive they are to damage. And as a result how long they last.
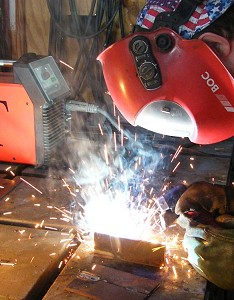
What about TIG?
The power source used in arc welders is very similar to the one used in TIG welders, and most (if not all) TIG welders can also be used for arc welding with the addition of a rod holder.
It doesn't work the other way around. TIG requires some extra features - a gas valve and HF start (an easy starting method that avoids tungsten contamination). If you also want to TIG weld it's best to start off looking at welders that are sold as TIG welders.
In more detail - what to look for?
- AC or DC?
DC is easier to start, and is safer than AC as the peak voltage is lower. Most rods can be run on DC. - Open circuit voltage (OCV)
Cheaper welders will tend to have 50V OCV which will make them more difficult to start, make the arc less stable, and prevent the use of special rods. Most decent transformer machines and inverters will run 70-80V and these are the ones to look for. - Start current, crater fill and fancy stuff
Many DC machines, and most inverters will increase the current when starting the arc. It's a useful feature to have as it makes it much easier to start the arc. Inverters often have crater fill which adds a little extra metal to fill the crater that is left is you pull the rod away to finish welding. - Maximum amps
An output of 140 amps is at the limit of a 13 amp 240V supply (for inverter machines). This will allow the use of 3.2mm rods. (100 amps output would be needed to run 2.5mm rods, and rods smaller than 2.5mm would require a lot more skill to use).
Higher outputs will allow the use of thicker rods which will reduce the number of passes required on thicker materials. - Duty cycle*
Some of the air cooled transformer arc welders have a very low duty cycle and can burn only one or two rods at full power before needing a long cooling period. Most other types should have an adequate duty cycle. - Display
For beginners it's very useful to have a digital amp readout to accurately set the amps. This helps rule out one of the variables in learning.
Aside from that the main choices are price, robustness, size, efficiency on a limited amp supply, and typical life time (which will depend on the quality and also on the type).
*More on Duty Cycles
The duty cycle of a welder normally reflects how long it can weld in a 10 minute period before it has to cool down. A 70% duty cycle would allow 7 minutes welding over a 10 minute period and the duty cycle will reduce as amps increase. It's not easy to compare duty cycles in manufacturers specs as the standards for measuring it vary between manufacturers.
Some expensive welders will test themselves at an ambient temperature of 40 degrees, some will test at room temperature, and others prefer it chilly. Also the time the duty cycle is measured over will vary between manufacturers. 10 minutes is the normal standard, but the cheaper welders often go for 5 minutes, instantly doubling their duty cycle. Very cheap welders with low duty cycles won't burn a rod before thermal cut out.