Alan, stop weaving and concentrate on practicing maintaining a SHORT arc length. Ideally no longer than the dia of the tungsten
Arc length is covered in the tutorials, also look at these threads http://www.mig-welding.co.uk/forum/threads/arc-length.7862/ & http://www.mig-welding.co.uk/forum/threads/tig-welding-stainless-manifold-help.23592/
With the correct arc length and no weaving you'd have one small weldpool at the point where the two parts meet instead of a large void bridged with filler metal (red arrow). Heat input would be lower for a given amperage too and the weldpool will much easier to control
FWIW this is 3" dia 1.5mm wall welded with 1 or 1.2mm filler wire after brushing the colour off (no point on exhaust stuff, this was for something else)
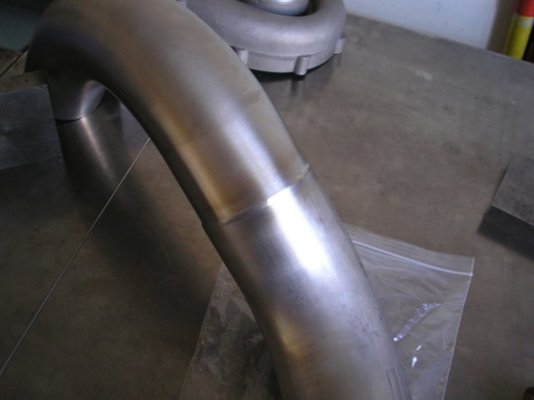
Arc length is covered in the tutorials, also look at these threads http://www.mig-welding.co.uk/forum/threads/arc-length.7862/ & http://www.mig-welding.co.uk/forum/threads/tig-welding-stainless-manifold-help.23592/
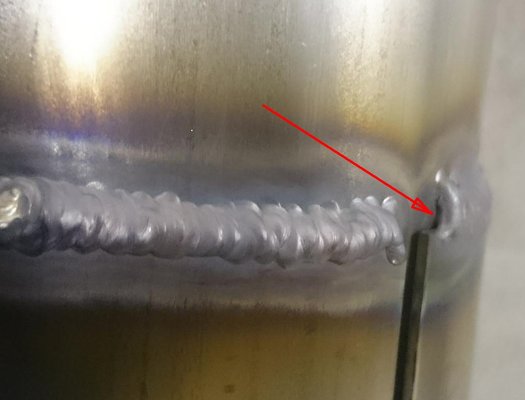
With the correct arc length and no weaving you'd have one small weldpool at the point where the two parts meet instead of a large void bridged with filler metal (red arrow). Heat input would be lower for a given amperage too and the weldpool will much easier to control
FWIW this is 3" dia 1.5mm wall welded with 1 or 1.2mm filler wire after brushing the colour off (no point on exhaust stuff, this was for something else)
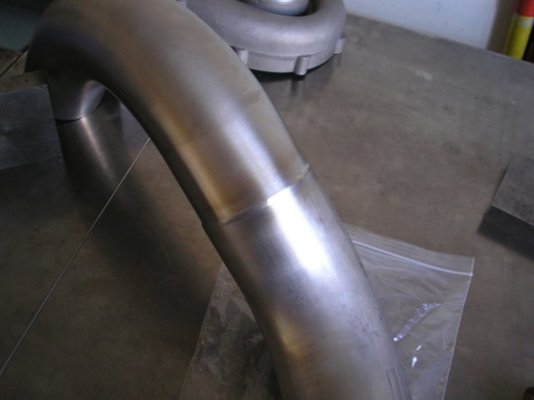