Dr.Al
Forum Supporter
- Messages
- 2,344
- Location
- Gloucestershire, UK
The bulk of this morning has been spent working on a shield to keep the sawdust out of the motor and inverter. I started with a big sheet of 0.8 mm thick steel, left-over from when I made some drawers (which you can see in lots of photos in this WIP). I marked out where I wanted the cuts to go, then did it again after getting it wrong first time (measure twice, and all that):
I then used my lovely little metal cutting circular saw to cut along the lines:
To remove the bit that goes over the spindle, I started by bending it back and forth to make the line a bit weaker and very clear:
I then considered a few different approaches, none of which seemed viable, before resorting to abusing one of my cheap and nasty chisels that I reserve for such abusive treatment:
One run along each side of the cut line and the thin steel was severed:
After roughly resharpening the poor chisel, I used a file to clean up the edge:
I then used my home-made sheet metal folder to form the sheet into shape:
For the last fold, I started with two clamps at each end of the bar:
Then moved one of them once I'd folded it up as far as I could (I didn't have any clamps with sufficient jaw depth to have a clamp from the front edge):
All done:
Before welding it, I did a quick test fit:
Then it was just a case of applying some tack welds:
Then using some more of the 3030 extrusion as an arm rest to try to get as comfortable as possible for welding:
The angle grinder then hides all the evidence:
When I made the shield, I hadn't really thought about how to mount it (although I had realised I needed to, I'd just put off the thinking!)
I rummaged around in my various metal stores and found a promising looking bit of aluminium angle. It already had a couple of holes in it; I added some more:
I then clamped it to the steel sheet with another bit of scrap aluminium at the back and then drilled through:
I did a similar process on the back end of the shield as well and with that, the shield is finished (give or take some rounding off of edges and some paint at some point):
It's held to the 3030 extrusion with two drop-in t-nuts at the front; the back just rests on the extrusion. I wanted it to be quick to remove as it'll have to be removed to adjust belt tension or to dismantle the lathe for storage. I thought I'd taken a photo of the finished shield in situ, but I can't find it. No doubt more photos will be taken in due course!
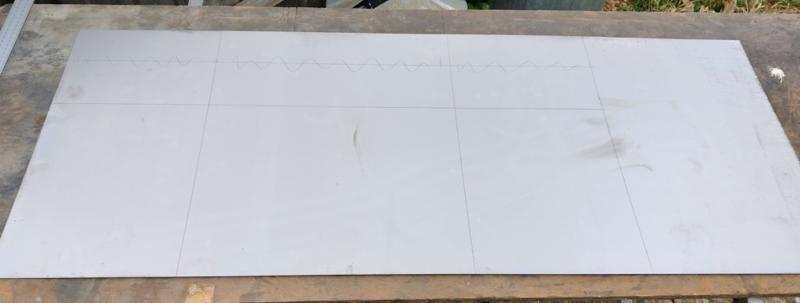
I then used my lovely little metal cutting circular saw to cut along the lines:
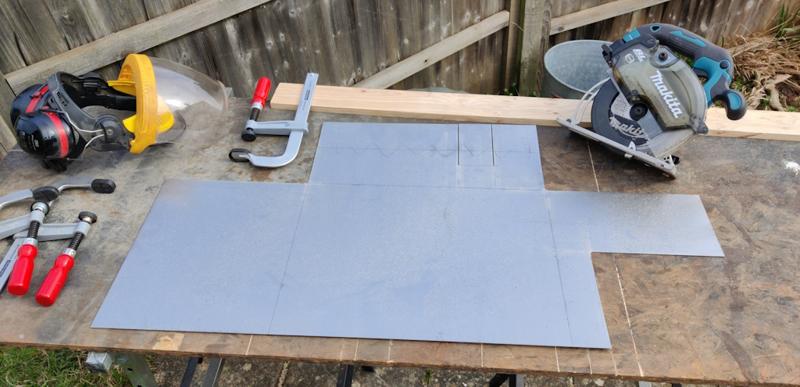
To remove the bit that goes over the spindle, I started by bending it back and forth to make the line a bit weaker and very clear:
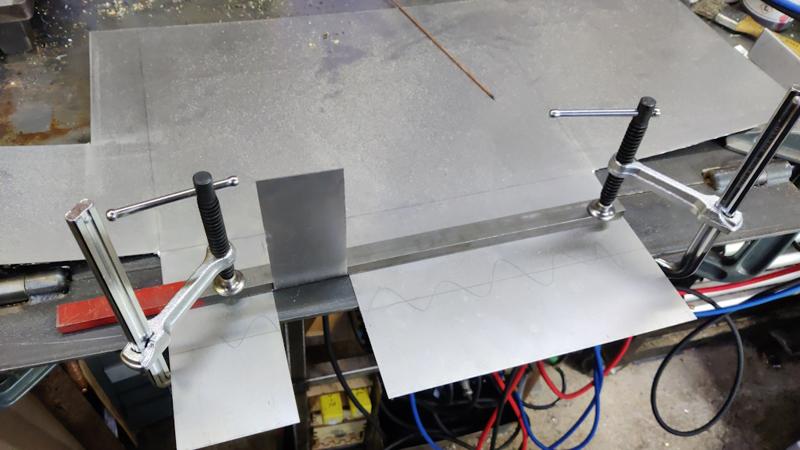
I then considered a few different approaches, none of which seemed viable, before resorting to abusing one of my cheap and nasty chisels that I reserve for such abusive treatment:
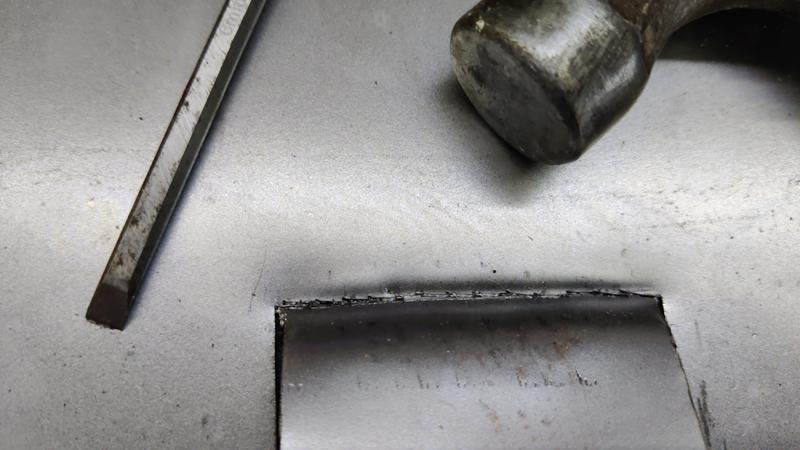
One run along each side of the cut line and the thin steel was severed:
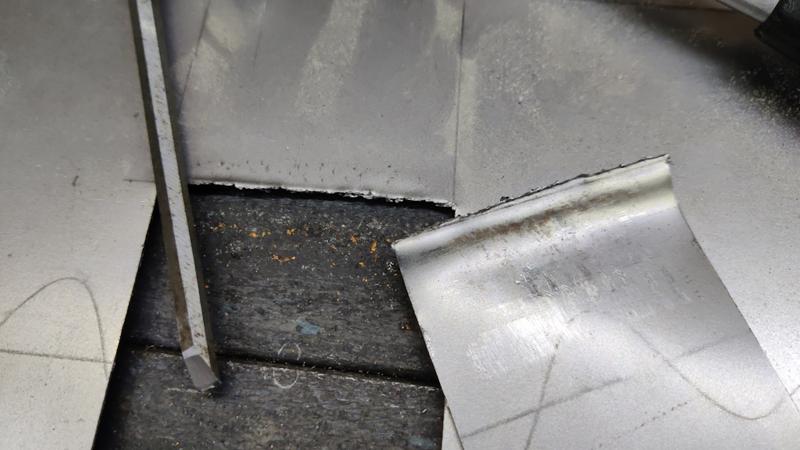
After roughly resharpening the poor chisel, I used a file to clean up the edge:
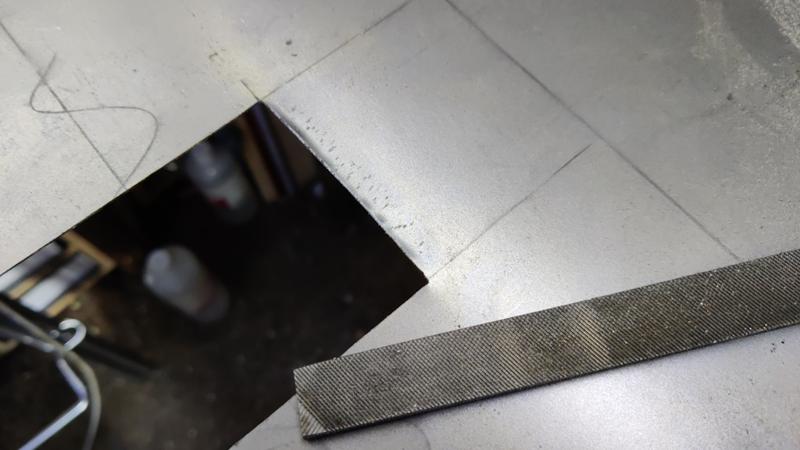
I then used my home-made sheet metal folder to form the sheet into shape:
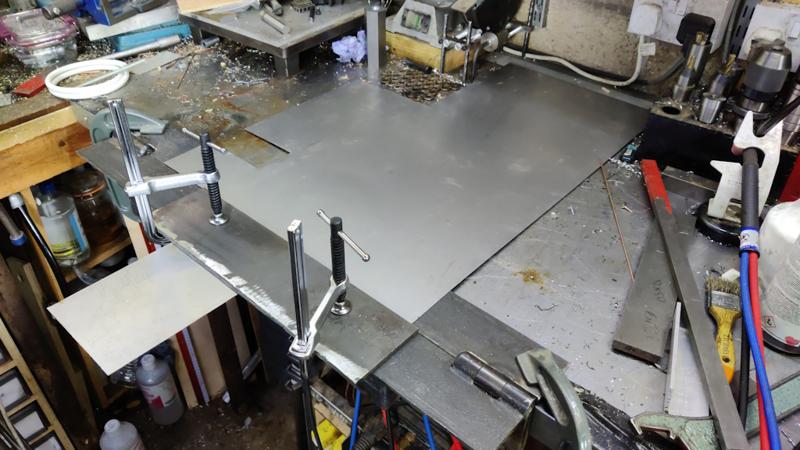
For the last fold, I started with two clamps at each end of the bar:
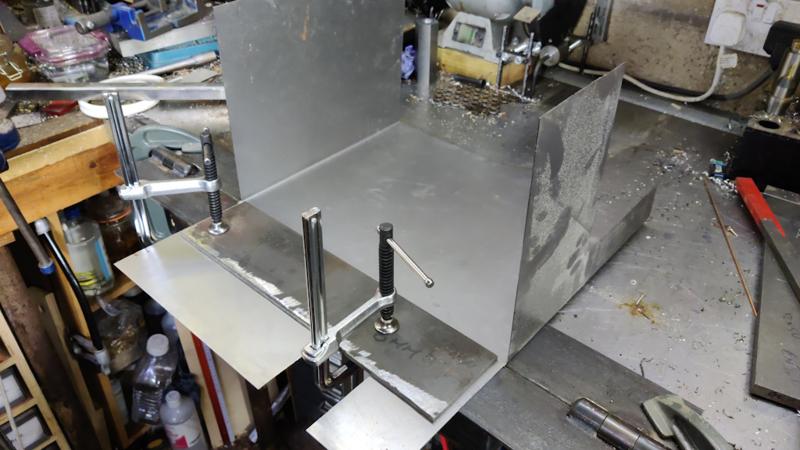
Then moved one of them once I'd folded it up as far as I could (I didn't have any clamps with sufficient jaw depth to have a clamp from the front edge):
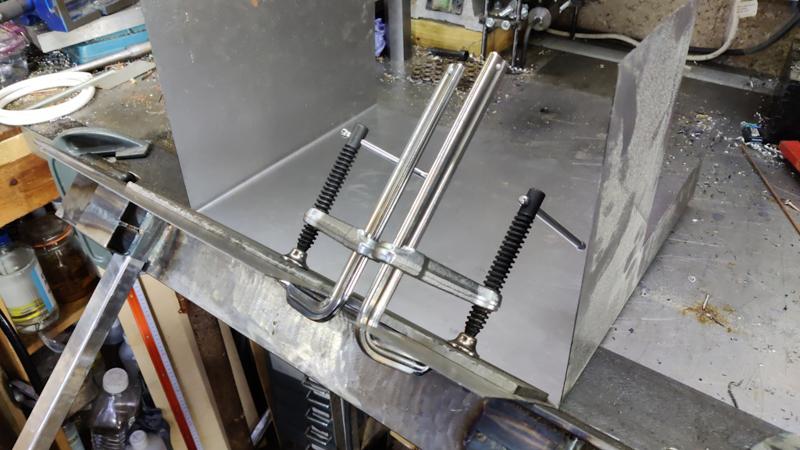
All done:
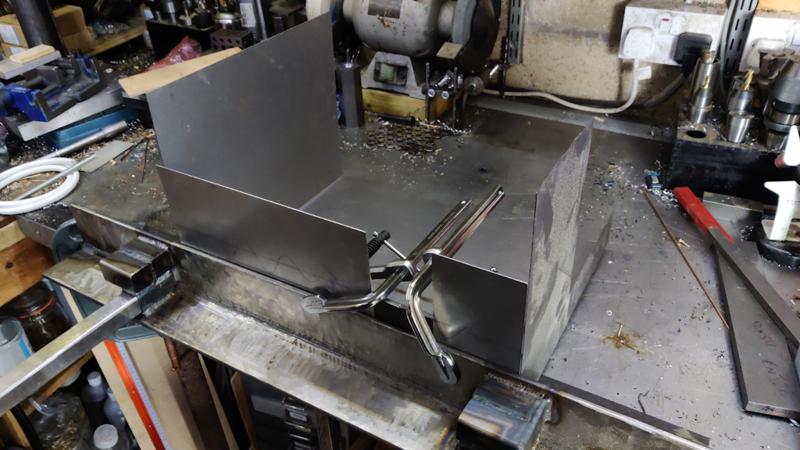
Before welding it, I did a quick test fit:
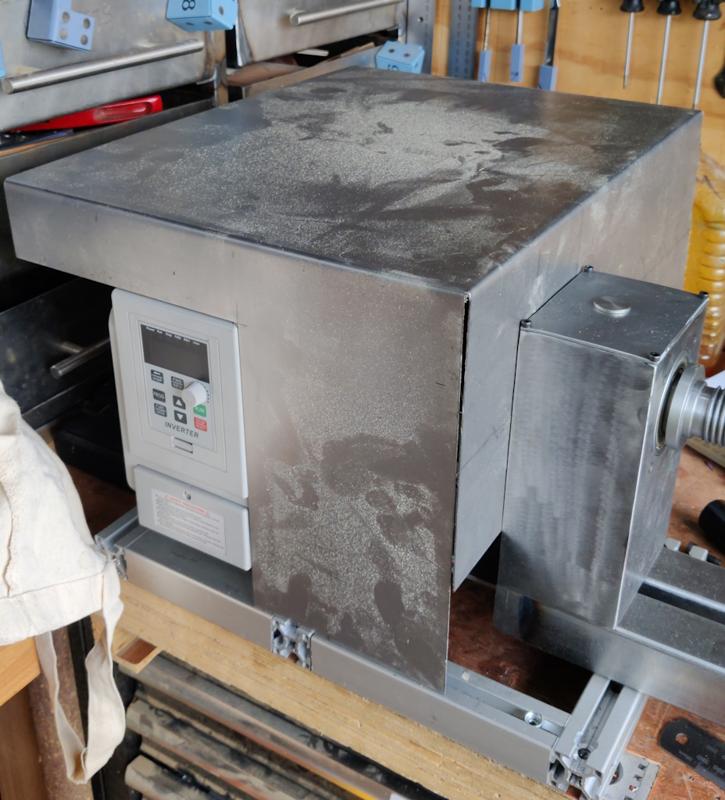
Then it was just a case of applying some tack welds:
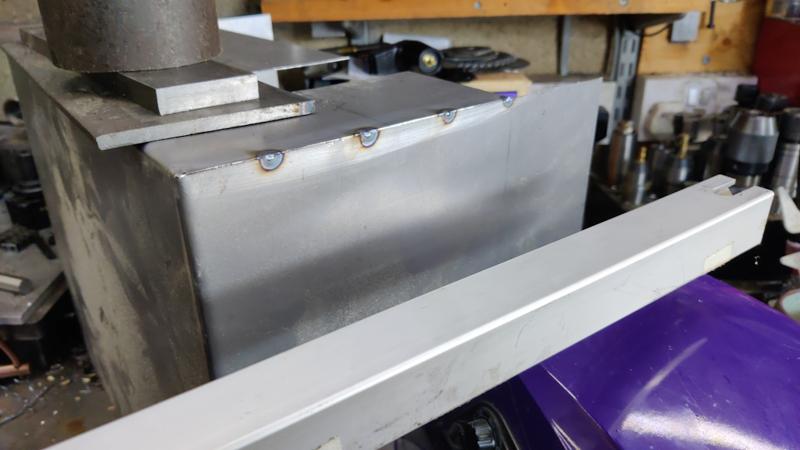
Then using some more of the 3030 extrusion as an arm rest to try to get as comfortable as possible for welding:
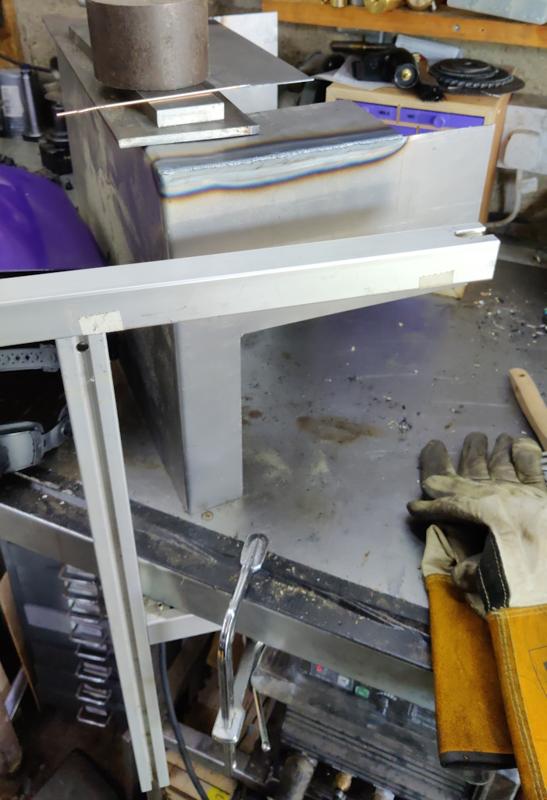
The angle grinder then hides all the evidence:
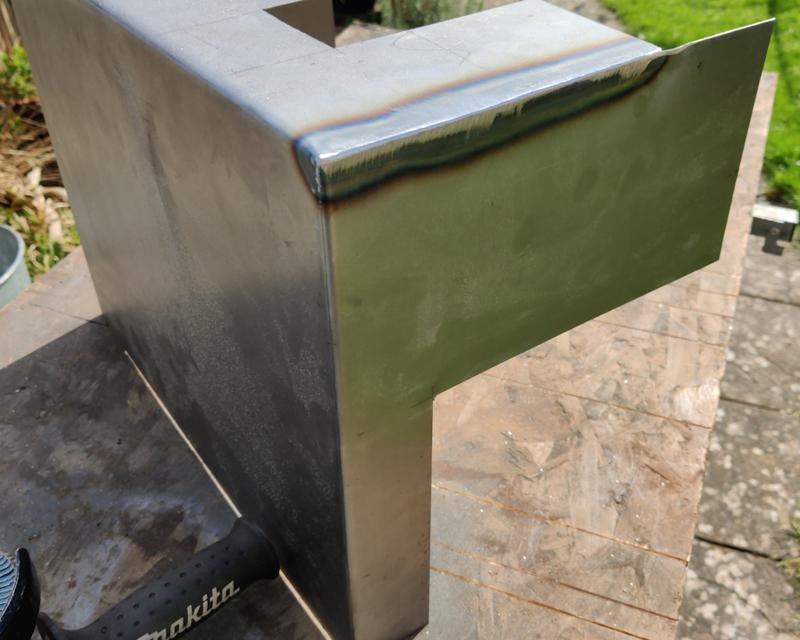
When I made the shield, I hadn't really thought about how to mount it (although I had realised I needed to, I'd just put off the thinking!)
I rummaged around in my various metal stores and found a promising looking bit of aluminium angle. It already had a couple of holes in it; I added some more:
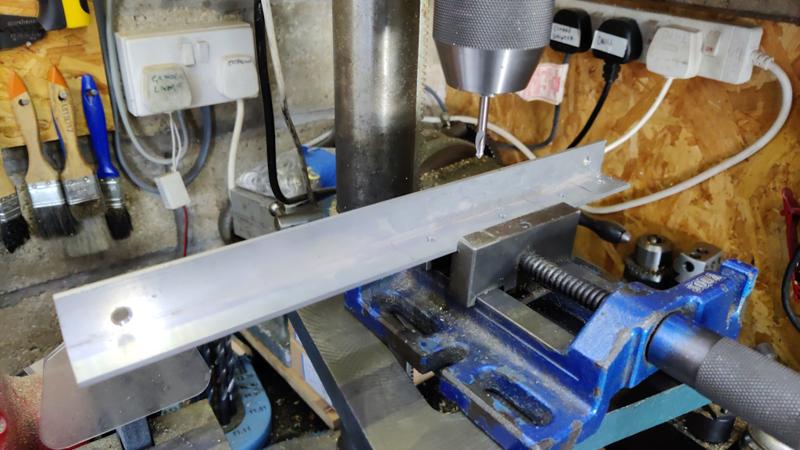
I then clamped it to the steel sheet with another bit of scrap aluminium at the back and then drilled through:
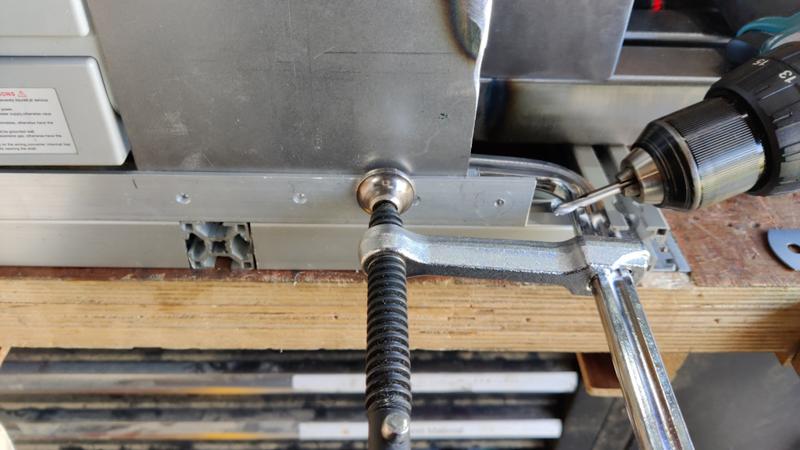
I did a similar process on the back end of the shield as well and with that, the shield is finished (give or take some rounding off of edges and some paint at some point):
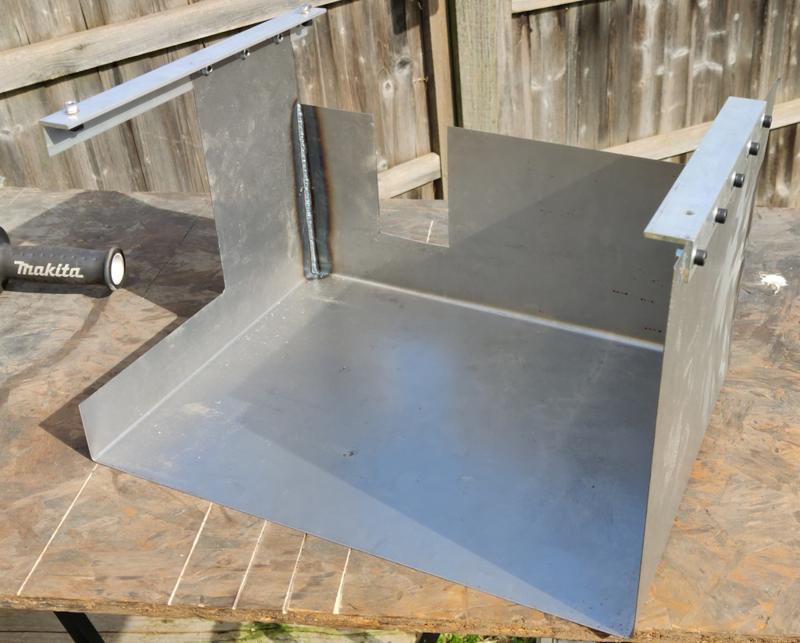
It's held to the 3030 extrusion with two drop-in t-nuts at the front; the back just rests on the extrusion. I wanted it to be quick to remove as it'll have to be removed to adjust belt tension or to dismantle the lathe for storage. I thought I'd taken a photo of the finished shield in situ, but I can't find it. No doubt more photos will be taken in due course!