Plug Welding
Plug welding is an alternative to spot welding used by vehicle manufacturers where there is insufficient access for a spot welder. For DIY car restoration it's generally used instead of spot welding on panels flanges that would have originally been spot welded.
Plug welds when done properly tend to be stronger than the original spot welds. Rally car builders often use the technique, and it is acceptable in a UK MOT test as an alternative to spot welds where repairing older cars (it would not be suitable for modern high tensile steels).
Plug welding
Start off by drilling 7.5mm holes in the front sheet of metal at a spacing of normally 25mm to 40mm (or whatever the original spot weld spacing was). Then clamp this sheet onto the back sheet.
7.5mm is a reasonably good hole size for 0.8 or 1.0mm sheet. Thicker sheet might require a slightly larger hole size. Try a little test piece out like this one before welding a whole sill onto a car and check the weld has penetrated through both sheets.
Welding through the hole
Position the welding torch with the wire in the center of the hole contacting the back sheet of metal. It is important to arc against this back sheet rather than on the edge of the hole, otherwise the weld might not penetrate into the back sheet. The torch should ideally be pointing directly into the hole rather than at the angle in the photograph.
Start welding in this position and don't move the welder until the hole is almost full of weld. Then move the welder outwards in ever increasing circles until the weld is completed.
The completed welds
If the sheets are the same thickness then the power setting used for plug welding would be the same as you would use for 1.5 times the thickness of one of the sheets.
Plug welding can be seen in action on the Aston Martin sills page.
Weld penetration
This is the sort of penetration you would expect from a plug weld. The molten pool is just breaking out of the reverse of the back sheet.
The heat marks indicate the weld has arced against the back sheet rather than at the side of the hole. If you don't get these marks then consider a little seam welding just to be sure.
Plug welding clamp
There is a special clamp designed for plug welding that makes life really easy. The parts you see in the photograph are attached to a normal mole grip. This clamp came in a set of three random welding clamps all of which are extremely useful.
The clamp holds together the flanges and there is space in the middle for the torch to weld the plug weld. The rear face of the clamp is offset so it can fit over flanges.
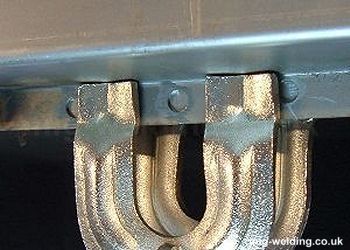
MIG Spot Welding
One alternative to plug welding is "MIG spot welding". It is similar to plug welding, although a hole is not drilled in the front sheet of metal. Instead the power of the MIG is relied upon to fully melt the top sheet and penetrate into the back sheet.
This technique would require less preparation work than plug welding, but the two sheets need to be in tight contact and high amps used to complete the weld or else the weld could be very weak. Plug welding is a much more suitable technique for all but the most experienced welders.