Needed to make a couple of stub axles for the wheels on the bandsaw table I am making. All a bit of a voyage of discovery as haven't really had a lot of time to play with the lathe since I got it a couple of years back, so was quite a nice learning project.
Had some EN16T (at least thats what I think it is going by bright finish and white paint on the end
) in 30mm.
Drilled some 25mm holes in the legs and the idea was to turn the rod down to 25mm, leaving a shoulder that would locate on the outside of the leg.
Then turn it down to 19mm which is the bore of the cast iron wheel, before ending with a M12 thread. I was going to weld in the stub axle but didn't fancy that in the end so by playing with the length of the various shoulders I have managed to mechanically fix and leave enough clearance so the wheel turns freely but doesn't wobble.
First challenge was turning the EN16T. Spent a wee while trying to work out speeds and feeds - not something I have every done before
.
I couldn't find a SFM for EN16 but as it is a bit harder than mild steel I reckoned on about 70-100? I was turning a 30mm bar so figured somewhere in the 200-300 rpm. The other imponderable was the feed speed.
I initially started it at what I thought was quite slow but it was just creating ridges/threads until I realised I was using the rapid transverse (or whatever it is called)
. Once I engaged the leadscrew feed at about .005"/rev it all started to come together.....
That was after grinding about 6 different HSS profiles before I got any that worked/were sharp enough.
So, 2 hours later and I could actually start turning the stub axle
- great learning experience though.
This was the chip when pushing a bit to hard/fast
And once I had it dialled in a bit better got them coming out like this with a 20 thou DOC
Even started to understand the value of chipbreakers as I dissapeared in a birdsnest of hot steel!
Eventually got the stub turned down and was quite pleased with the finish. Not polished but pretty smooth and way better than previous attempts
And after a beer even had time to clean down the shop ready to turn the other one tomorrow
Cheers,
MM
Had some EN16T (at least thats what I think it is going by bright finish and white paint on the end

Drilled some 25mm holes in the legs and the idea was to turn the rod down to 25mm, leaving a shoulder that would locate on the outside of the leg.
Then turn it down to 19mm which is the bore of the cast iron wheel, before ending with a M12 thread. I was going to weld in the stub axle but didn't fancy that in the end so by playing with the length of the various shoulders I have managed to mechanically fix and leave enough clearance so the wheel turns freely but doesn't wobble.
First challenge was turning the EN16T. Spent a wee while trying to work out speeds and feeds - not something I have every done before

I couldn't find a SFM for EN16 but as it is a bit harder than mild steel I reckoned on about 70-100? I was turning a 30mm bar so figured somewhere in the 200-300 rpm. The other imponderable was the feed speed.
I initially started it at what I thought was quite slow but it was just creating ridges/threads until I realised I was using the rapid transverse (or whatever it is called)

That was after grinding about 6 different HSS profiles before I got any that worked/were sharp enough.

So, 2 hours later and I could actually start turning the stub axle

This was the chip when pushing a bit to hard/fast

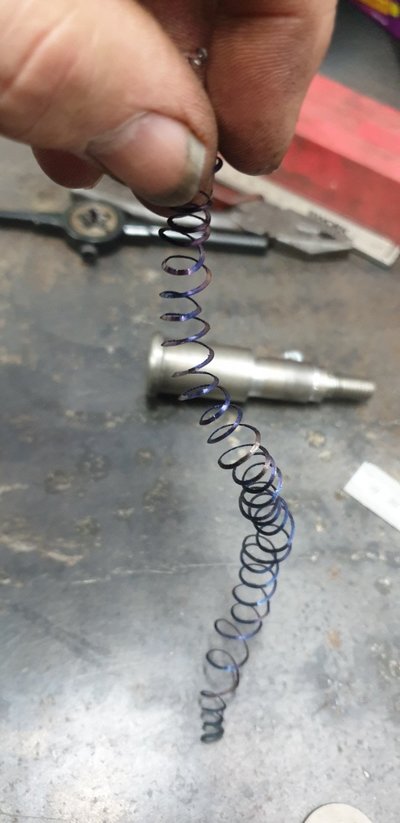
And once I had it dialled in a bit better got them coming out like this with a 20 thou DOC
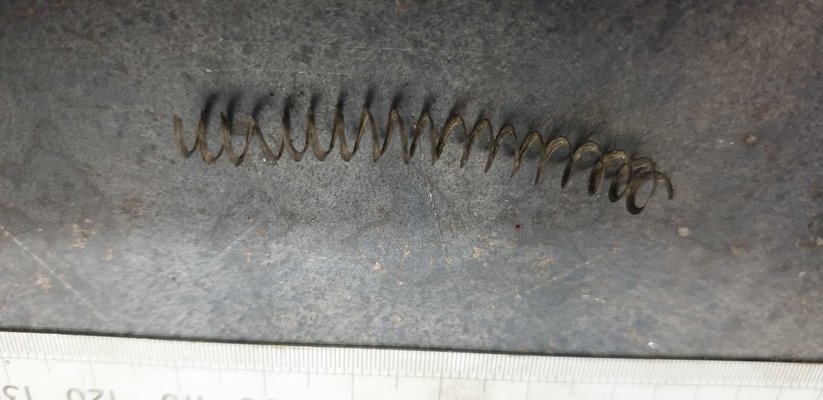
Even started to understand the value of chipbreakers as I dissapeared in a birdsnest of hot steel!
Eventually got the stub turned down and was quite pleased with the finish. Not polished but pretty smooth and way better than previous attempts
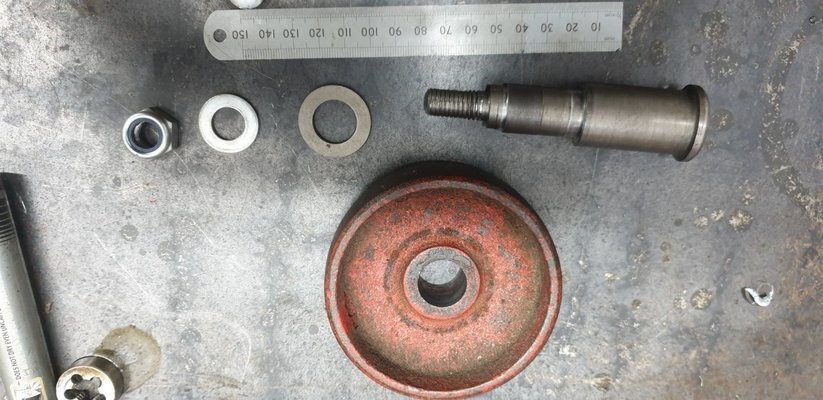
And after a beer even had time to clean down the shop ready to turn the other one tomorrow

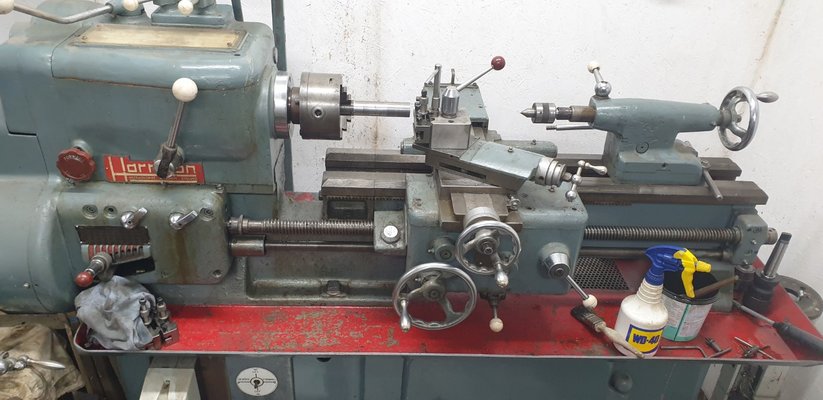
Cheers,
MM